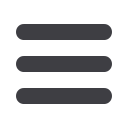
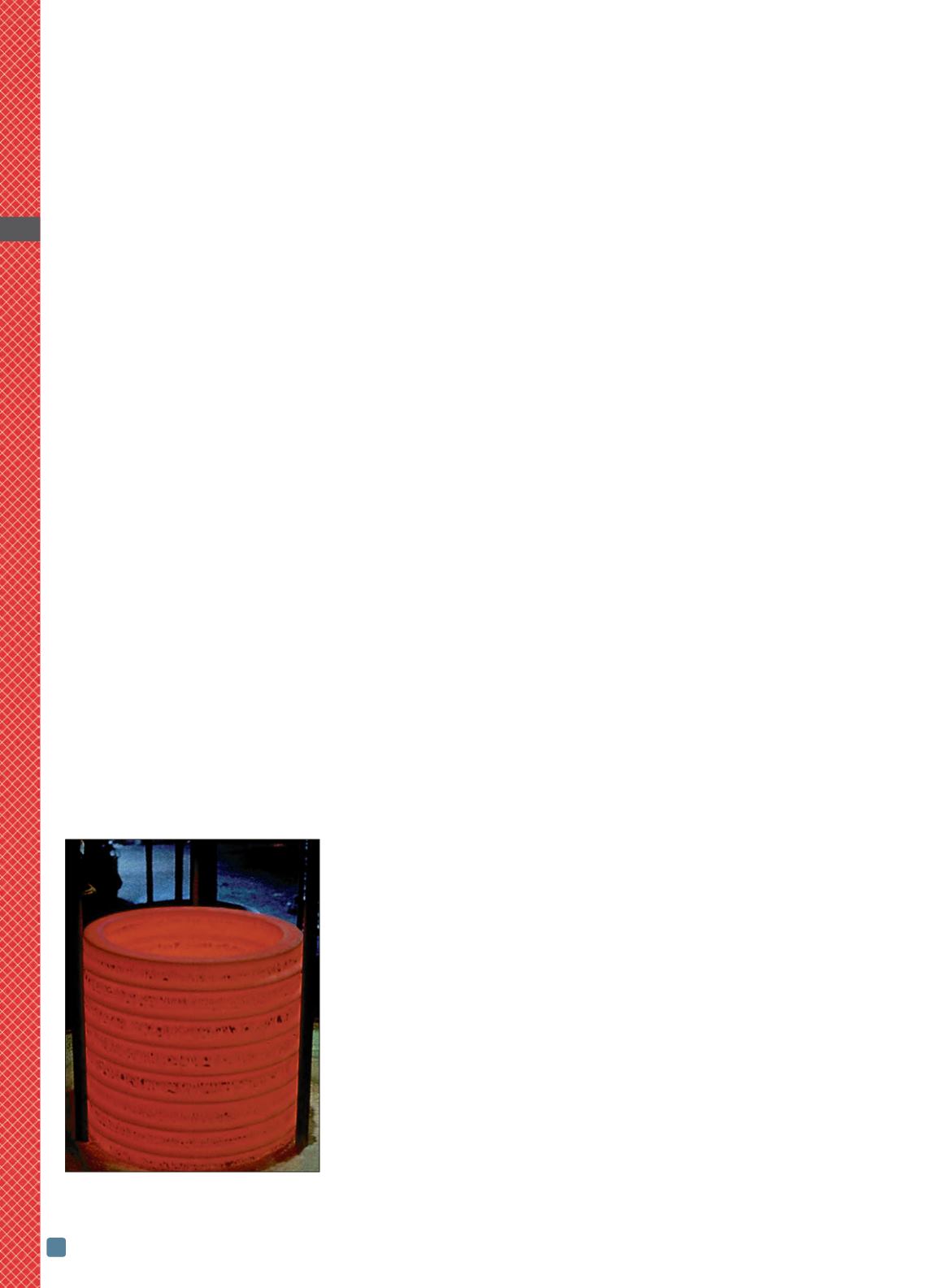
ADVANCED MATERIALS & PROCESSES •
JUNE 2014
42
The size of a batch immersion quench
tank depends on the dimensions of the
workload, as well as the allowable tem-
perature rise. The temperature rise per-
mitted is dependent on whether the
quenchant is oil, water, or polymer.
In a batch operation, care should be
taken to ensure that a sufficient amount
of quenchant covers the top of the work-
load. The physical dimensions of the
tank should be large enough to ensure
full immersion of the quench load and
fixtures, and, at the same time, should
allow enough space for agitators and ma-
nipulators. Depending on the size of the
workload, it is generally appropriate to
have at least 150–300 mm (6–12 in.) of
fluid over the top of the workload, and
preferably more.
When using hot quenching oils, it is nec-
essary to make an allowance for thermal
expansion of the oil, either by making
provision for an overflow system, or by
manual adjustment of the fluid level.
Tank capacity
A quench tank must contain sufficient
fluid to quench the load without an ex-
cessive rise in temperature of the
quenching fluid. In an uncooled tank,
the quantity of quenchant required can
be calculated from the basic equation:
M
m
Cp
m
D
T
m
=
M
q
Cp
q
D
T
q
Where
M
m
is the mass of metal,
Cp
m
is
the specific heat of the metal, D
T
m
is
the decrease in temperature of the
metal being quenched,
M
q
is the mass
of quenchaant,
Cp
q
is the specific heat
of the quenchant, and D
T
q
is the in-
crease in temperature of the quen-
chant. Typical values for specific heat
at 20°C (70°F) are:
Steel — 0.17 cal/g/C (0.17 Btu/lb/F)
Aluminum — 0.23 cal/g/C
(0.23 Btu/lb/F)
Quench Oil — 0.50 cal/g/C
(0.50 Btu/lb/F)
Polymer Quenchant — 0.95 cal/g/C
(0.95 Btu/lb/F)
Water — 1.0 cal/g/C (1.0 Btu/lb/F)
A general guideline for steel quenching
(for a single quench) is that 10 liters of
oil is required for each kilogram of total
charge weight (1 gal/lb). This rule of
thumb results in about a 40°C (70°F)
temperature rise under nominal condi-
tions, which is recommended to prevent
the oil from reaching the flashpoint of
the fluid. It is recommended that the
maximum temperature during quench-
ing using oils always should be at least
55°C (100 °F) below the flash tempera-
ture, which mitigates the potential for a
fire if a hung-up load occurs. This is il-
lustrated in the following example:
Flash temperature of the oil:
175°C (350°F)
Recommended temperature
cushion: 55°C (100°F)
Temperature rise during quenching:
40°C (70°F)
Maximum recommended operating
temperature: 80°C (180°F)
However, with successive quenches,
some form of cooling is necessary to pre-
vent the oil from overheating. The heat
exchanger should be sized to recover the
heat produced by the quenched load
within one heat treating cycle.
For example, in quenching 2270 kg (5000
lb) of steel from 870°C (1600°F), a heat
treater wants to remove the parts from
the oil at 65°C (150°F). The “cold
quench” oil used has a flash temperature
of 175°C (350°F) and operates at a tem-
perature of 60°C (140°F). Based on these
process parameters, the maximum peak
temperature of the oil (considering the
flash point of 175°C), would be 120°C
(250°F). What should the minimum size
of the quench tank be? Using the equa-
tion given above:
M
m
Cp
m
D
T
m
=
M
q
Cp
q
D
T
q
or
M
q
=
M
m
Cp
m
D
T
m
/
Cp
q
D
T
q
therefore
M
q
= 5000 lb (0.17 Btu/lb/F)
(1600 - 150F)/0.50 Btu/lb/F (110F)
M
q
= 22,409 lb (10,185 kg) oil
At a weight of 6.8 lb/gal (0.8 kg/liter), ap-
proximately 3300 gal (12,500 liters) are
required for these conditions. However,
this temperature rise is a bit excessive
and could lead to premature oxidation of
the oil. Alternatively, rearranging the
equations using a fixed size quench tank
allows solving for the temperature rise
during quenching.
Water and polymer quenchants have a
different limitation on temperature. This
is not related to safety, as with quench
oils, but effective cooling for water, and
maximum operating temperatures for
polymer quenching. For water, the max-
imum temperature is 100°C (210°F).
However, this limit is rarely used as the
cost of make-up and cooling becomes
excessive. For polymer quenchants and
water used in quenching aluminum,
aerospace standards specify a maximum
SIZING QUENCH TANKS FOR
BATCH IMMERSION QUENCHING
HTPRO
6
*Member of ASM International and Heat Treating Society.
A QUENCH TANK MUST CONTAIN SUFFICIENT FLUID TO QUENCH THE LOAD
WITHOUT AN EXCESSIVE RISE IN TEMPERATURE OF THE QUENCHING FLUID.
D. Scott MacKenzie,* FASM,
Houghton International Inc., Valley Forge, Pa.
Hot charge ready to be quenched