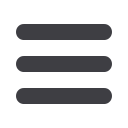
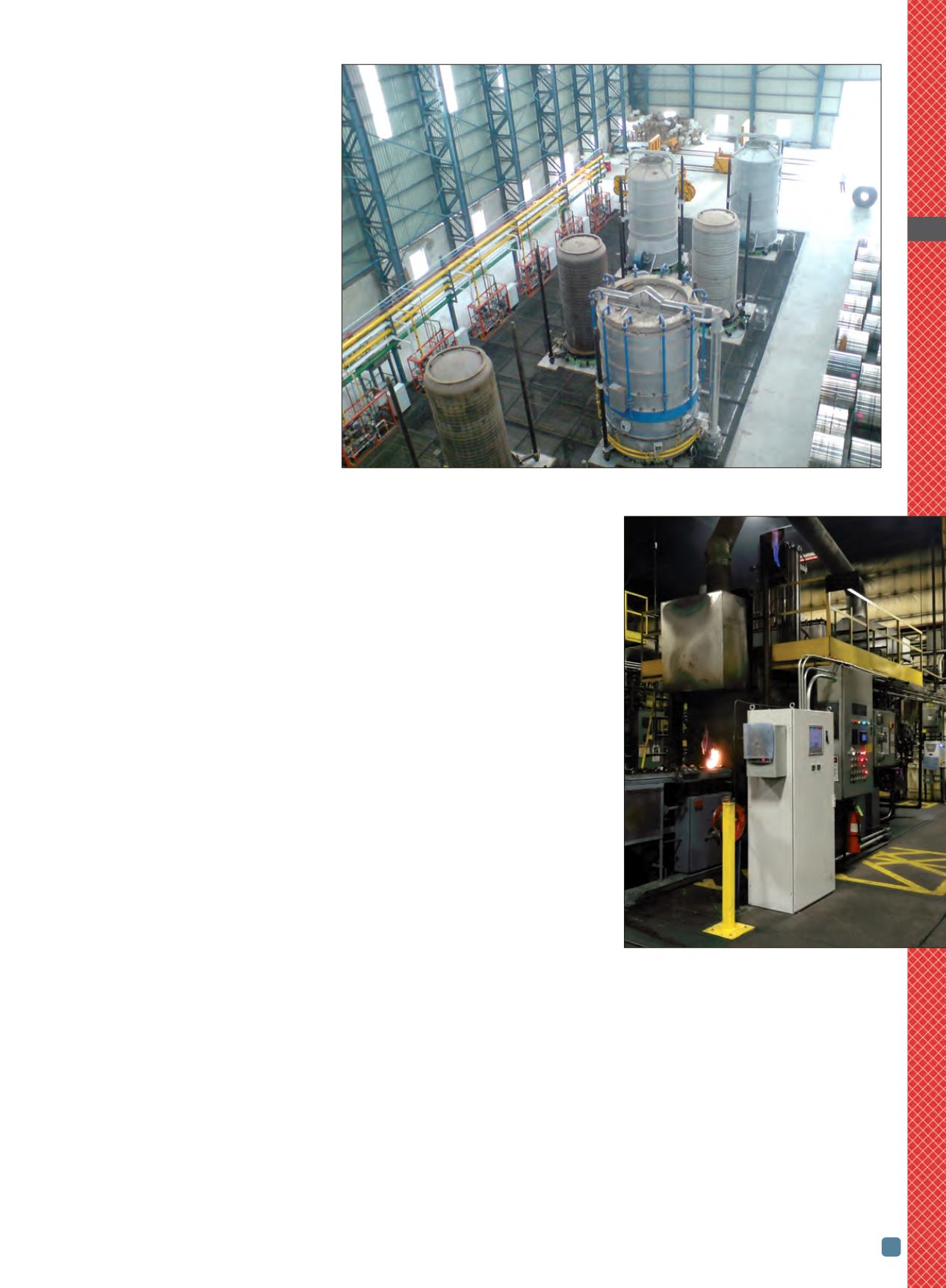
ADVANCED MATERIALS & PROCESSES •
MARCH 2014
45
come worse as more stringent quality
specifications in mechanical proper-
ties (e.g., hardness variations across
the coil) were anticipated.
Three recommendations were offered
after examining the operation by com-
bining results of process analytics with
process model (phenomenological and
neural-network) simulations: (1) clas-
sifying coils in a different manner for
stacking in the furnace charge, (2) es-
tablishing new chemical composition
specifications for coils to be annealed,
and (3) creating new model-based
process cycles (temperature and soak-
ing time) for different coil classes. The
integrated approach reduced overall
rejection rates and downgrading rates
for two major products by 44 and 60%,
respectively, thereby enabling the de-
sired tightening of quality specifica-
tions. The reduction in rework and
downgrading also significantly re-
duced the plant’s specific energy con-
sumption. Achieved benefits were
monitored and sustained for more
than one year
[2]
.
Automated coil batch annealing.
In an-
other study, an automated batch an-
nealing operation in an integrated steel
plant was analyzed and optimized
[3]
.
The modern operation was equipped
with a model-based control system,
which simulated the process and de-
rived optimized recipes before heat
treating individual stacks of coils. In the
study, process and quality data were an-
alyzed and compared with physics-
based models, which showed that the
thermal model used in the control sys-
tem was very conservative in estimat-
ing heat transfer across the coils. As a
result, process cycle time did not vary
with the thickness of the coil stack. In
addition, the control system was only
based on thermal differential across the
coils, so nonisothermal effects arising
from complex recipitation/recrystal-
lization/grain growth mechanisms were
not captured. Because of the non-
isothermal effect, accelerated annealing
kinetics with a reduction in heating rate
was observed through physics-based
modeling and laboratory kinetics ex-
periments. An appropriate thermal
conductivity model and nonisothermal
models were used to create transfer
functions for the process recipe derived
from the control system to modify the
resulting recipes. This approach was
validated on an industrial scale, and
overall productivity of the 1-million
ton/year integrated steel plant was im-
proved by 9%
[3]
together with a consid-
erable reduction in specific energy cost.
Batch carburizing.
In a recent study, a
carburizing operation of a modern
heat treating shop was analyzed, mod-
eled, and optimized. The heat treating
operation has 12 quench-sealed fur-
naces for heat treating transmission
components such as gears and shafts.
About 500 MB of data comprising
charge characteristics (dimensions,
number of parts, charge configuration,
and weight), process parameters (fur-
nace temperature-time and carbon po-
tential-time records of various
segments, and oil temperature-time)
and quality (case depth, microstruc-
ture, hardness, and retained austenite)
were extracted for the operation for a
one-year period. All data were
recorded with different periodicity. For
example, furnace process data were
recorded every minute, whereas qual-
ity data were recorded per batch. Raw
process data (time, temperature, and
carbon potential) were transformed
from a per minute basis into a per
batch basis with the mean and stan-
dard deviations values. Subsequently,
process data were merged with charge
HTPRO
9
Fig. 2 —
Representative coil batch-annealing operation.
Fig. 3 —
Representative carburizing
operation with integral quench furnaces.