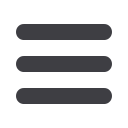
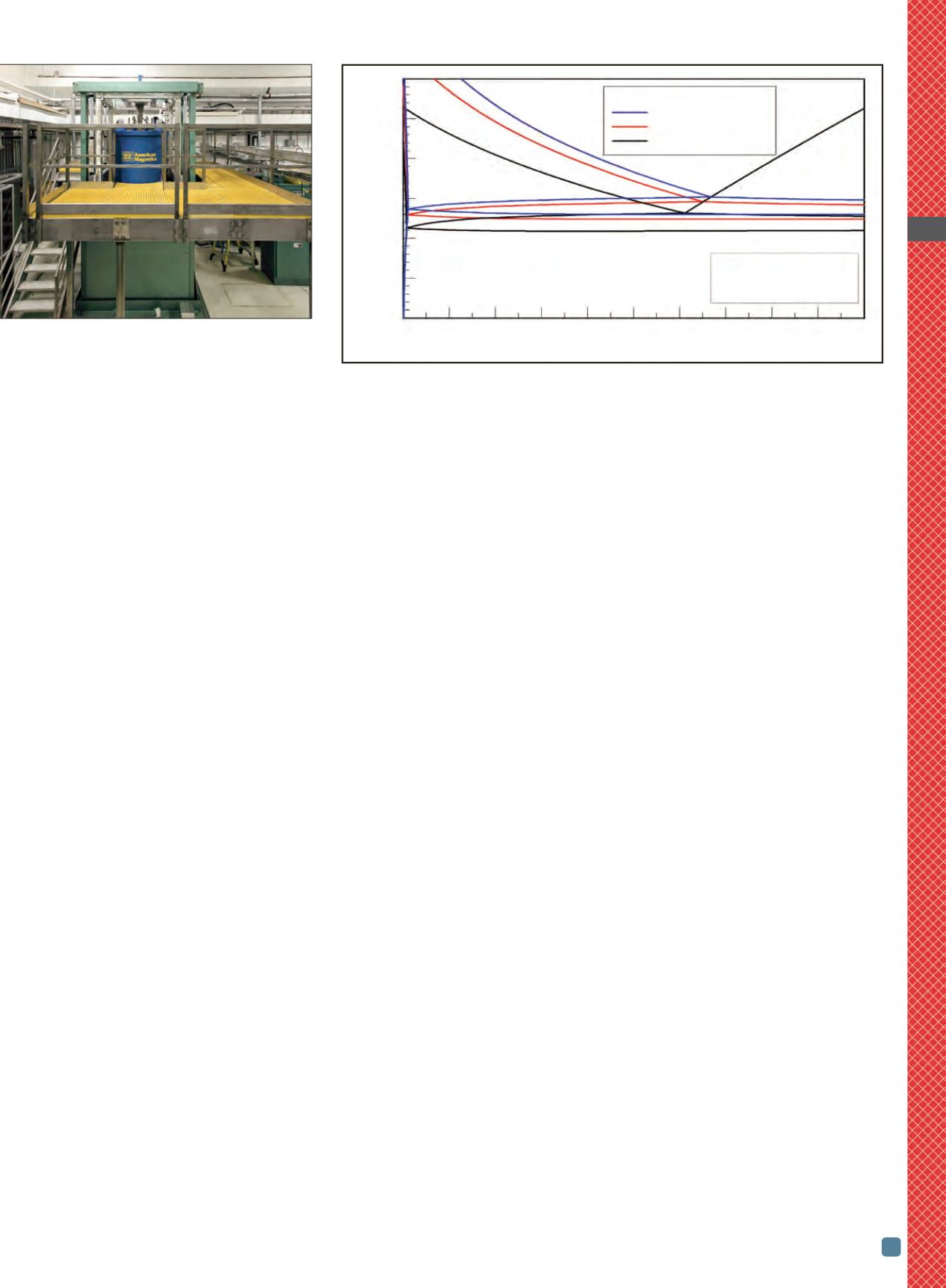
ADVANCED MATERIALS & PROCESSES •
MARCH 2014
43
HTPRO
7
less) and complex dynamic thermal geo-
metric profiles, these dynamics cannot be
accurately recorded nor can they graphi-
cally display the part’s internal thermal re-
sponse and reactions. The dynamics
inhibit a more complete understanding
and evaluation of the multiple reaction is-
sues involved, limiting the ability to estab-
lish an optimal process. However,
because induction heating is electrically
applied and fully electronically controlled,
it can be mathematically modeled and ob-
jectively simulated (via “what if” studies).
The resultant graphics display provides a
detailed representation of the dynamic
interactions involved to help better un-
derstand the process.
Challenges and limitations of under-
standing the process are fully addressed,
and actual dynamics can simulated by
using the latest induction computer
modeling programs—including fully
coupled, electromagnetic/thermal and
FEA/FED modeling. This approach
enables graphical display of complex
thermal logistics and subsequent inter-
reactive reactions to understand the
process, make adjustments, and identify
optimal reactions/process parameters/
dynamics to improve part performance.
Coupling material science and simula-
tion process engineering provides an ad-
vanced understanding and review of
viable alternative solutions.
High magnetic field processing (HMFP)
A new high magnetic field processing
(HMFP) and thermomagnetic field pro-
cessing (TMFP) facility at Oak Ridge Na-
tional Laboratory, Tenn., includes an
industrial-scale HMFP facility with an in-
tegrated induction heating and quench-
ing capability for conducting industrial
experiments (Fig 1). Coupling a high
magnetic field environment with an ap-
plied induction elevated temperature ca-
pability offers an enabling disruptive
technology. This approach enables
achieving stronger, more durable compo-
nents and materials with improved per-
formance. Induction heating plus a high
magnetic field processes parts much
faster than thermal processing alone be-
cause the magnetic field alters the phase
equilibrium diagram (Fig. 2). It shifts
phase-transition temperatures, and phase
solubilities increase with increasing tem-
perature. Other benefits include:
• Accelerated phase transformations
• Enhanced nucleation and growth
during phase transformation
• Smaller grain size
• Less segregation during solidification
• More homogeneous microstructure
and properties
• Higher strength and plasticity
• Lower residual stresses
• Faster diffusion
Such a technology offers the means to
make significant major science and tech-
nological advancements in developing
the next generation of novel structural
and functional materials for use in a
broad range of transportation and mili-
tary applications.
All materials are influenced by high
magnetic fields, so all material systems
from metallic through polymeric and
protein will respond to an induction
thermal high magnetic field (ITHMF)
environment. Major improvements in
performance (from 15 to 300%) can be
manifested in mechanical and/or physi-
cal properties. For example, an ITHMF
(9 T) processed Hy Tuf vacuum arc
remelted high-strength, low-alloy steel
(Latrobe Specialty Steels Co., Pa.) has an
equivalent ultimate tensile strength and
double the toughness of a more expen-
sive conventionally processed 250
maraging steel grade.
Development of nanocrystalline and tex-
tured and/or novel microstructures and
reaction paths is made easier and faster
through the synthesis and catalytic chem-
ical effect of the extreme ITHMF envi-
ronment. In addition, the deformation
behavior (magnetoplasticity) of materials
appears to be influenced by high mag-
netic fields, potentially enabling high- and
low-cycle fatigue damage mitigation (life
extension), superplastic behavior at am-
bient temperature, residual stress relief,
and other visionary applications. It might
even be possible to make classically brit-
tle materials formable under high mag-
netic fields. Therefore, the ITHMF
environment has an impact on phase
equilibria and kinetics and represents a
new synthesis/catalysis paradigm and a
deformation/life enhancement process-
ing breakthrough technology.
HTPRO
Acknowledgement:
The authors thank
Dr. Gerard Ludtka and Dr. Gail Ludtka,
Oak Ridge National Laboratory, Tenn., for
input from their research on this technol-
ogy conducted at ORNL.
For more information:
George Pfaffmann
is vice president of technology, Ajax
TOCCO Magnethermic Corp., 30100
Stephenson Hwy., Madison Heights, MI
48071, 248/691-2281,
gpfaffmann@ ajaxtocco.com,
www.ajaxtocco.com.
Fig. 1 —
ITHMF setup at ORNL consists of
a commercial prototype 9-T, 8-in. diameter
by 9-in. long uniform field strength
superconducting magnet to conduct large-
scale experiments.
Fig. 2 —
The application of a high magnetic field on an AISI 1045 carbon steel shifts all
phase equilibria.
0 0.1 0.2 0.3 0.4 0.5 0.6 0.7 0.8 0.9 1.0
Carbon, wt%
1045 carbon steel
7 T magnetic field
5 T magnetic field
No magnetic field
g
- fcc
a
- bcc
Fe 3 C – orthorhombic
a
+
g
g
Fe 3 C +
g
a
+ Fe 3 C
900
850
800
750
700
650
600
Temperature, ºC