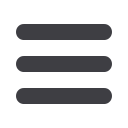
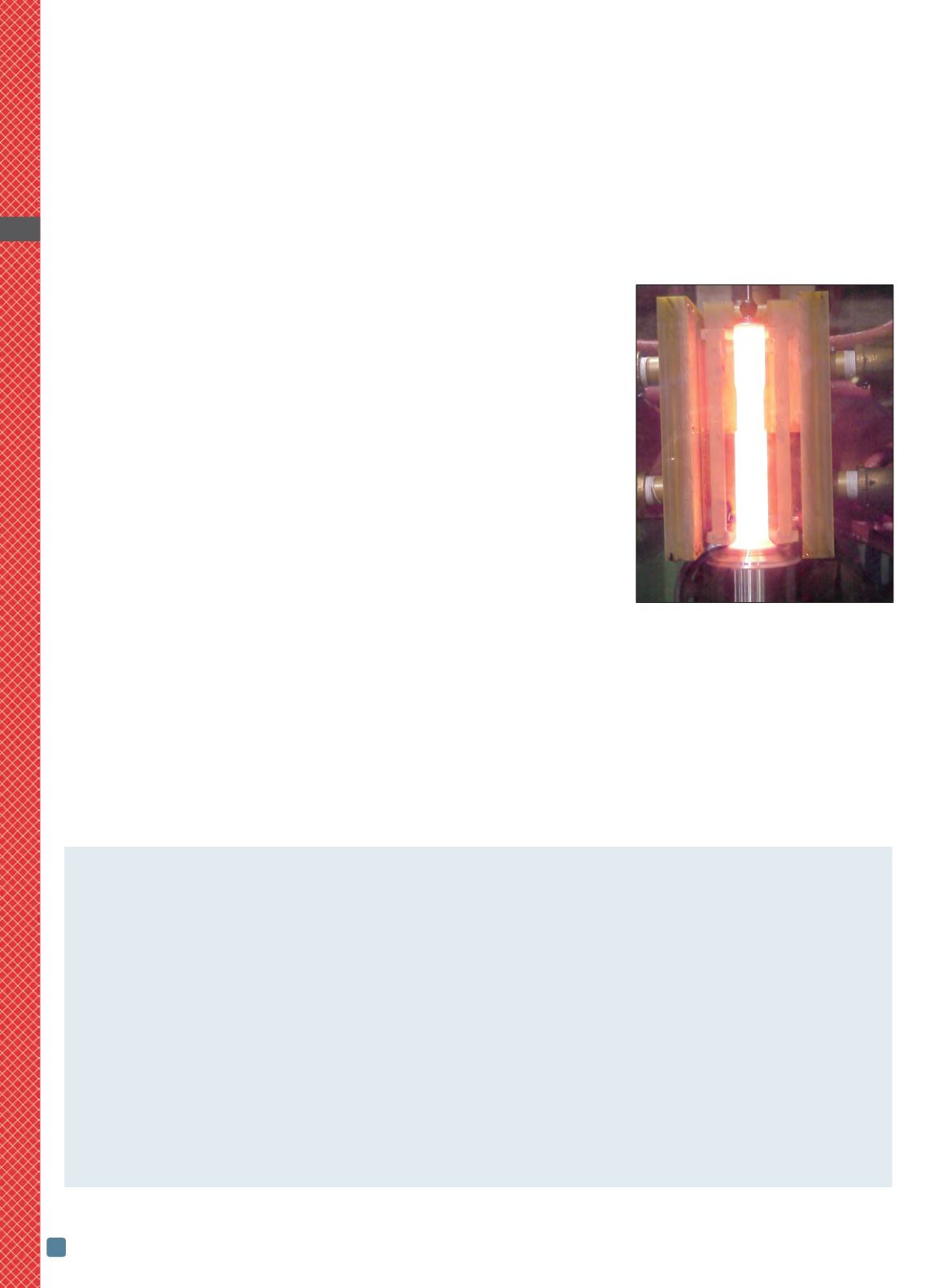
ADVANCED MATERIALS & PROCESSES •
MARCH 2014
42
Increasing demand from the durable
goods market (e.g., automotive, agricul-
ture, aerospace) for lighter weight, more
efficient, and highly durable products re-
quires a significant increase in
material/component strength and per-
formance capability. Traditional ther-
mally activated processes used to
improve materials strength and per-
formance have evolved empirically and
are largely isothermally based, equilib-
rium reactions. Using this approach,
heat input, flow, and its redistribution
are driven only by an applied elevated-
temperature differential. Therefore, the
desire to accelerate thermal transfer re-
quires the application of higher surface
temperatures and longer times, which
can result in several undesirable effects
and other process capability limitations.
Advanced induction thermal capabilities
Continual improvement of induction
heating technology has increased the
ability to selectively focus and provide a
highly controlled internal thermal pro-
file of a part, enabling optimization of
specifically programmed, thermally
driven metallurgical reactions for maxi-
mum strengthening results. Notably, the
latest innovations in equipment versatil-
ity and FEA-modeled hardware tooling
provide an unmatched, precise capabil-
ity to accelerate processing speeds and
produce novel metallurgical microstruc-
turally enhanced strength (ultra-grain
refinement approaching the nanoscale
plus unique beneficial microstructure
morphology) in a part.
Induction heating generates heat (with
truly no limit on achievable temperature)
within the part’s subsurface. The depth of
heat distribution can be programmed and
dynamically profiled to produce desired
metallurgical results, which are achieved
by the efficient use of environmentally
clean electrical energy. The part’s internal
heat profile can be optimized using a wide
range of in-situ computerized process-
control parameters. Therefore, process-
ing can be customized to provide
optimally driven reactions for improved
part performance.
Induction heating thermal dynamics are
vastly different from those applied in tra-
ditional isothermal systems. In cases of
short heating times (1 to 2 seconds or
I
NDUCTION COUPLED
HIGH MAGNETIC FIELD EXPANDS
PROCESSING ENVELOPE FOR
HEAT TREAT INNOVATIONS
TRADITIONAL HEAT TREATING PROCESSES HAVE REACHED A PLATEAU
AND ARE NO LONGER GOOD ENOUGH.
George Pfaffmann, FASM*,
Ajax-TOCCO Magnethermic Corp., Madison Heights, Mich.
Aquil Ahmad*,
Metallurgical Consultant, West Bloomfield, Mich.
HTPRO
6
*Member of ASM International
Recognition of the need
A recent U.S. Army Solicitation for Innovative Research on High Magnetic Field Processing illustrates that there is a need for
such disruptive technology. The document reads in part:
The Army is highly interested in the application of electromagnetic fields for development of ultralightweight metals with tai-
lored microstructures and properties. The current methods used to manipulate metal properties involve varying scale, compo-
sition, temperature, and pressure to improve strength, hardness, facture toughness, elastic modulus, density, etc., but the use of
these traditional techniques for tailoring a wide range of chemical and physical properties is reaching a plateau. It is worth not-
ing that significant ongoing research is being dedicated to reengineering and exploring the creation of materials at the nanoscale,
which holds potential for future applications that inherently hinge on surmounting scalability, assembly, and producibility
challenges. However, there is an emerging technology that goes beyond factors of scale, composition, temperature, and pressure,
and holds great promise in facilitating the realization of transformal materials with the aid of externally applied fields. The
application of fields may alter phase transformation pathways, create new microstructures, shift equilibrium favoring new
metastable alloys, align phases, manipulate and shape nanoscale architectures, and produce materials with revolutionary
structural and multifunctional properties otherwise unattainable by conventional processing and production methods. The
application of electromagnetic fields offers the unique opportunity to direct the architecture of materials features across atomic,
molecular, micro, meso, and continuum levels. These fields may either be used to induce a permanent material property im-
provement or to selectively activate enhanced time-dependent properties via dynamic stimulation.
Induction heating a shaft.