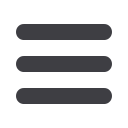
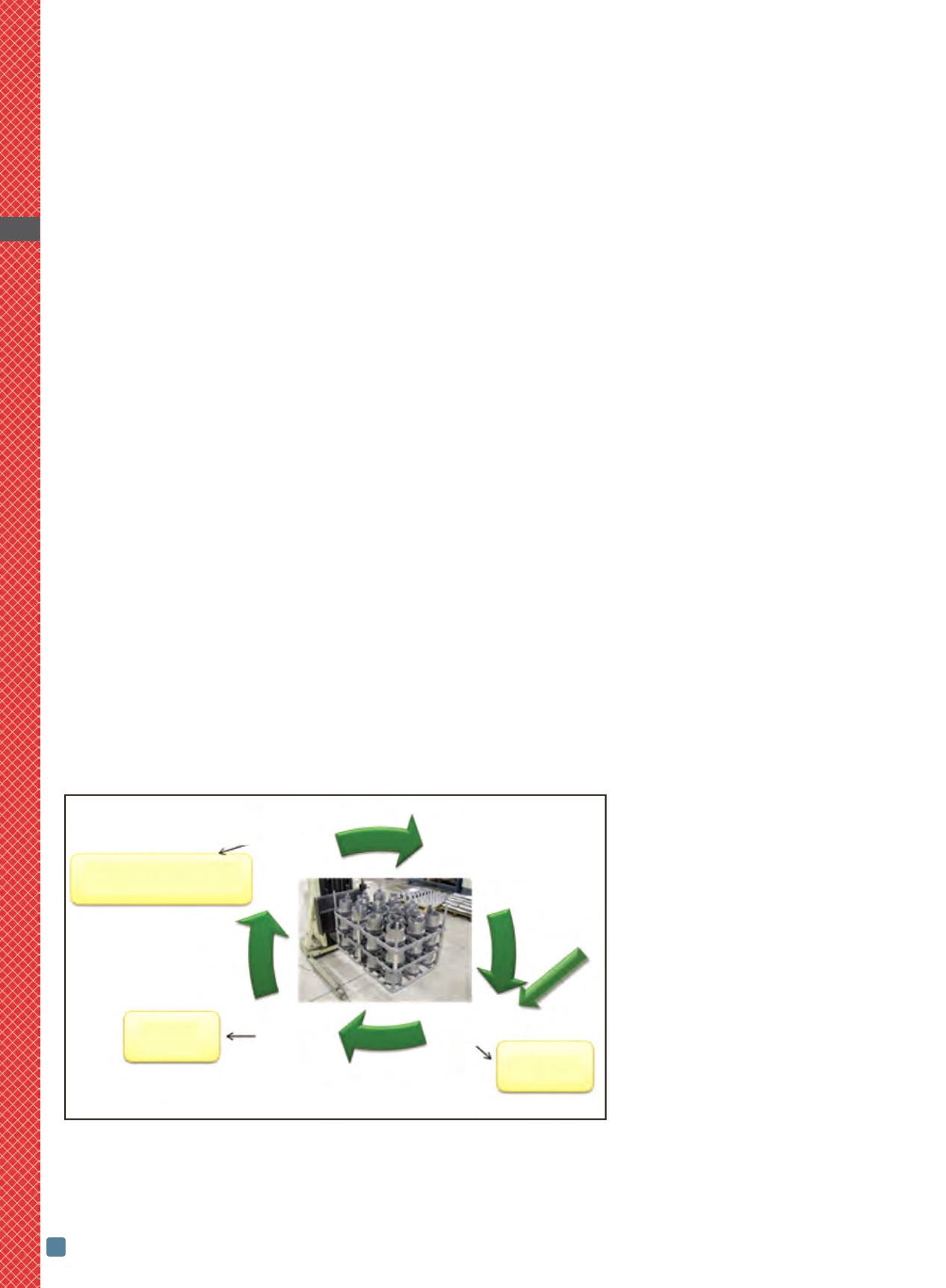
ADVANCED MATERIALS & PROCESSES •
MARCH 2014
44
Modern industrial heat treating oper-
ations have sophisticated IT architec-
tures, where significant amounts of
data in GB/TB per year are generated
including characteristics of input ma-
terial (chemistry, prior material qual-
ity, charge dimensions, quantity, and
configuration), process parameters
(furnace temperature, carbon poten-
tial, and quenching oil-temperature
variation with time) and product qual-
ity (hardness, microstructure, case
depth, and distortion) are generated.
These manufacturing data are prima-
rily used for process audits and trou-
bleshooting specific batches that have
quality issues.
Much of this collected data goes un-
used. However, it could be significantly
leveraged to generate process insight
and optimize processes to improve
manufacturing efficiency and product
quality for an overall reduction in oper-
ational and energy costs. Figure 1 illus-
trates that this could be achieved in a
closed loop, where the manufacturing
data together with heat treating knowl-
edge can be synthesized with physics
and data-based modeling approaches to
generate insight for process optimiza-
tion and control. Actionable outcomes
at different phases of the loop are also
shown in the figure. For example, many
surprises about process and product
can emerge from process analysis and
modeling, where the insight generated
from this approach could directly im-
pact product quality and design recom-
mendations. This could enhance key
process efficiency metrics—namely, op-
erational and energy costs, productiv-
ity, and quality.
This approach is an expanded, generic
view of a typical smart-manufacturing
circle
[1]
comprising Data-Analyze-
Model-Apply. Big data, data analytics,
and data-based modeling approaches
(neural network, principal compo-
nent analysis, and other advanced sta-
tistical methods) are emerging as key
areas to analyze manufacturing oper-
ations. Data-based approaches are ef-
fective to generate predictions within
a current operating regime from
which data are derived.
In contrast, physics-based models can
also lead to an optimum operating
condition, which is far removed from
current conditions. Physics-based
models for heat treating operations
incorporate mass and energy conser-
vation, laws of heat transfer, metallur-
gical thermodynamics, and chemical
reactions and kinetics. Some impor-
tant physics-based models with re-
spect to carburizing include thermal
models, diffusion kinetics, quenching
models, residual stress, and distortion
models. A judicious synthesis of these
two approaches and modeling
methodologies is far more effective
than focusing on individual compo-
nents of the process.
Case studies
Coil batch annealing.
This generic ap-
proach was effectively demonstrated
by the significant improvement in
first-pass yield of an industrial batch
annealing operation in a secondary
cold-rolling mill
[2]
. The operation had
many operating challenges including
the need to process coils with high
variability from different sources,
pressure to maintain a low inventory
level, and a lack of a process model
that could customize cycle design for
individual coil stacks. As a result,
more than 50% of annealed coils
failed to meet target quality require-
ments, resulting in product down-
grade, or rework that added
significant cost to meet product qual-
ity. The situation was expected to be-
ANALYTICS, MODELING, AND OPTIMIZATION OF
INDUSTRIAL HEAT TREATING PROCESSES
MANUFACTURING DATA ARE PRIMARILY USED FOR PROCESS AUDITS AND TROUBLESHOOTING
SPECIFIC BATCHES THAT HAVE QUALITY ISSUES, BUT COULD BE LEVERAGED TO GAIN INSIGHT
FOR OVERALL PROCESS OPTIMIZATION AND CONTROL.
Satyam S. Sahay, FASM* and Goutam Mohapatra,
John Deere Asia Technology Innovation Center, Pune, India
Robert Gaster*,
John Deere Moline Technology Innovation Center, Ill.
Hema Guthy*,
John Deere Coffeyville Works, Kan.
8
HTPRO
*Member of ASM International
Fig. 1 —
Manufacturing data together with heat treating knowledge can be synthesized
with physics and data-based modeling approaches in a closed loop to provide insight
for improving process efficiency and product quality for overall reduction in operating and
energy costs.
Optimize
and
control
Data
Heat treat
knowledge
Analysis,
Insight modeling
and
recommendations
Surprises?
R&A, design
Process efficiency
Cost, productivity, quality