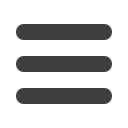
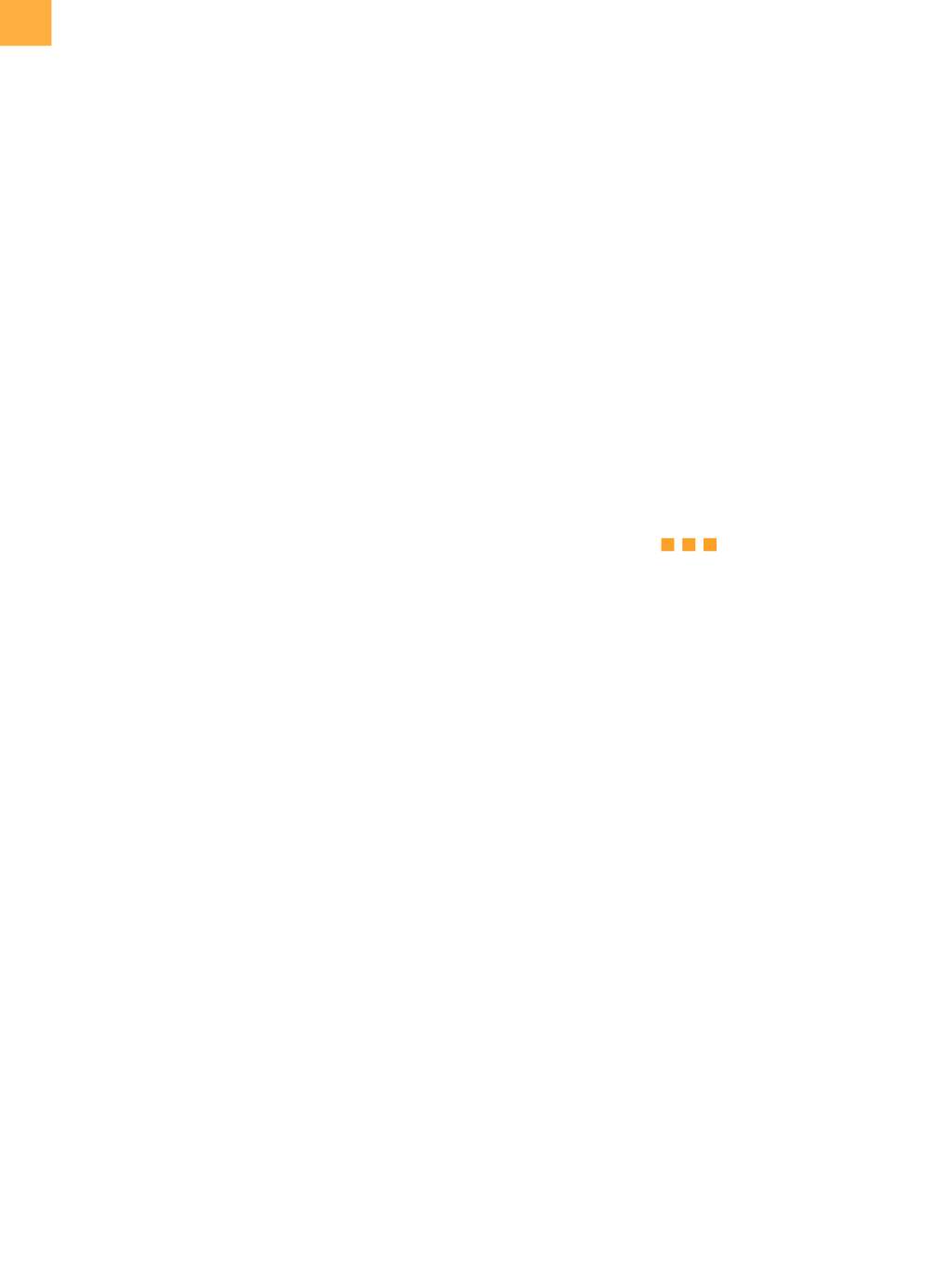
edfas.org
ELECTRONIC DEVICE FAILURE ANALYSIS | VOLUME 19 NO. 1
4
EDFAAO (2017) 1:4-8
1537-0755/$19.00 ©ASM International
®
FAILURE ANALYSIS ON SOLDERED BALL GRID ARRAYS:
PART I
Gert Vogel, Siemens AG, Digital Factory Division, Control Products, DF CP QM SQA 5
gert.vogel@siemens.comB
all grid arrays (BGAs) are widely used on complex
printed circuit board assemblies (PCBAs). Ball grid
arrays are a type of surface-mount package, where
it is not possible to directly visually inspect solder connec-
tions because they are hidden as an array of small solder
balls underneath the devices. X-ray imaging canbe used to
automatically control the balls regarding soldering faults,
but this only provides information about failure types that
lead to a deformation of the balls, such as electrical short
circuits or voids in the soldered balls.
A detailed analysis of these failures—and also other
types of failures that are only accessible by electrical
measurements—can usually be conducted only through
destructive physical analysis, which involves cross sec-
tioning solder joints. However, BGAs can have more than
1,000 solder balls, and not every type of failure can be
identified by taking a cross section.
This article demonstrates new approaches to failure
analysis on BGA balls aswell as the related failure analysis
on printed circuit boards (PCBs).
INTRODUCTION
Failures of BGAs on PCBAs are primarily related to the
solder connection andnot to aproblemat the silicon level.
There are failures that can be measured electri-
cally, such as short circuits or open circuits in the array
of solder balls, as well as failures found by performing an
x-ray inspection. For example, voids do not represent an
immediate threat but area long-termquality risk. (A failure
is defined as a void percentage of more than 30% of the
ball area in the x-ray image, in accordancewith IPC-A-610,
“Acceptability of Electronic Assemblies.”)
Voids such as these in the solder joints of BGAs are very
aggravating because they normally cannot be repaired by
simply resoldering; even replacing an expensive compo-
nent with a new one is not always successful. A recourse
against the supplier is usually futile becausemany factors
may be responsible for these types of failures. In most
cases, the supplier is right. Even if deep oxidized needle
indents in a singular instance can be responsible for voids
in BGA balls, the balls are not normally responsible for
these types of failures.
FAILURE ANALYSIS OF SOLDER JOINTS
THAT CANNOT BE VISUALLY INSPECTED
A further complication when analyzing failed BGA
balls is that the solder joints cannot be visually inspected.
Therefore, obtaining information about the location of an
open or short circuit is only possible by making electrical
measurements or by performing an x-ray inspection.
Experience shows that the PCB is predominantly the
main source relating to problems involving soldering
of BGA balls; however, the solder paste or the solder-
ing process itself can also be responsible for problems.
Process problems such as oxygen intrusion during reflow
can lead to so-called “champagne voids,” which aremany
small voids on the interface between the solder mate-
rial and the pad metallization (Fig. 1). The inadvertently
added oxygen consumes a high amount of the reducing
organic acids from the flux in the solder paste, which was
balanced for use under nitrogen atmosphere. If all of the
acid is consumed, a web of remaining tin oxide, originat-
ing from the grain boundaries of the solder balls, blocks
the escape of the gas bubbles that develop. Such a root
“THIS ARTICLE DEMONSTRATES NEW
APPROACHES TO FAILURE ANALYSIS ON
BGA BALLS AS WELL AS THE RELATED
FAILURE ANALYSIS ON PRINTED
CIRCUIT BOARDS (PCBs). ”