
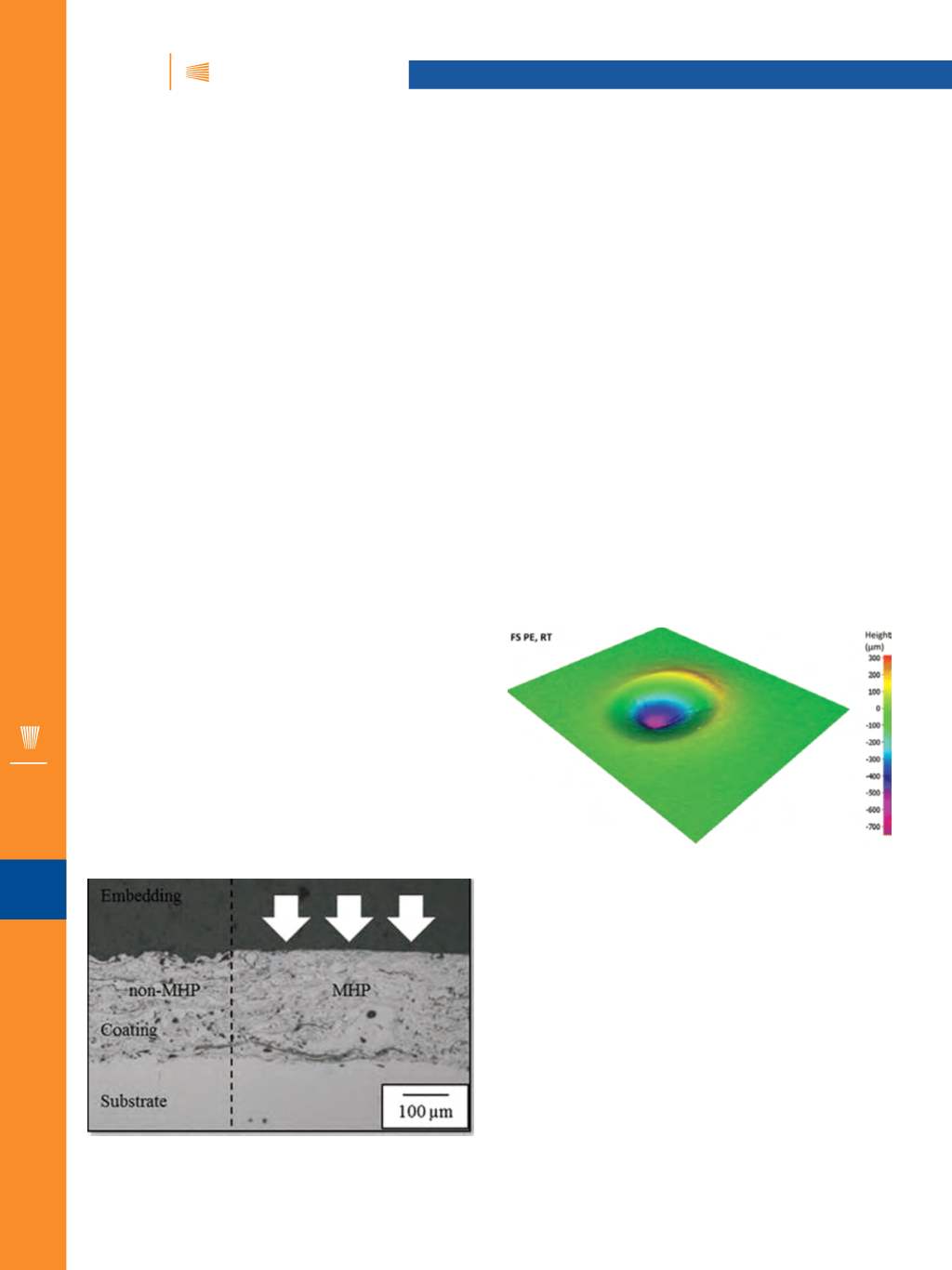
iTSSe
TSS
A D V A N C E D M A T E R I A L S & P R O C E S S E S | F E B R U A R Y / M A R C H 2 0 1 7
4 6
iTSSe
TSS
INVESTIGATION ON THE TRIBOLOGICAL
BEHAVIOR OF ARC-SPRAYED AND HAMMER-
PEENED COATINGS USING TUNGSTEN
CARBIDE CORED WIRES
W. Tillmann, L. Hagen, and P. Schröder
Due to their outstanding properties, WC-W
2
C iron-based
cermet coatings are widely used in the field of wear protec-
tion. Regarding commonly used WC-W
2
C reinforced coating
systems, it has been reported that their tribological behavior is
mainly determined by the carbide grain size fraction. Although
the manufacturing route for arc-sprayed WC-W
2
C cermet coat-
ings is in an advanced state, there is still a lack of knowledge
concerning the performance of cored wires with tungsten car-
bides as filling material and their related coating properties
when post-treatment processes are used, such as machine
hammer peening (MHP). A major objective was to character-
ize WC-W
2
C FeCMnSi coatings deposited with different carbide
grain size fractions as a filling using cored wires, with respect
to their tribological behavior. Moreover, deposits derived from
cored wires with a different amount of hard phases are inves-
tigated. According to this study, polished MHP surfaces are
compared to as-sprayed and polished samples by means of
metallographic investigations. With the use of ball-on-disk and
dry rubber wheel tests, dry sliding and rolling wear effects on
a microscopic level are scrutinized. It has been shown that the
MHP process leads to a densification of the microstructure for-
mation. For dry sliding experiments, the MHP coatings obtain
lower wear resistances, but lower coefficients of friction than
the conventional coatings. With regard to abrasion tests, the
MHP coatings possess improved wear resistance. Strain hard-
ening effects at the subsurface area were revealed by the me-
chanical response using nanoindentation. However, the MHP
process caused a cracking of embedded carbides, which favor
breakouts, leading to advanced third-body wear (Fig. 3).
ANTI-ICING BEHAVIOR OF THERMALLY
SPRAYED POLYMER COATINGS
Heli Koivuluoto, Christian Stenroos, Mikko Kylmälahti,
Marian Apostol, Jarkko Kiilakoski, and Petri Vuoristo
Surface engineering shows increasing potential to pro-
vide a sustainable approach to icing problems. Icing reduces
safety, operational tempo, and productivity, as well as the
reliability of logistics, industry, and infrastructure. Currently,
several passive anti-icing properties adaptable to coatings are
known, but further research is required to proceed into practi-
cal applications. An icingwind tunnel and centrifugal ice adhe-
sion testing equipment can be used to evaluate and develop
anti-icing and icephobic coatings for potential use in various
arctic environments, e.g., in wind power generation, oil drill-
ing, mining, and logistic industries. The present study deals
with evaluation of icing properties of flame-sprayed polyeth-
ylene (PE)-based polymer coatings. In laboratory-scale icing
tests, thermally sprayed polymer coatings showed low ice ad-
hesion compared with metals such as aluminum and stainless
steel. The ice adhesion strength of the flame-sprayed PE coat-
ing was found to have approximately seven times lower ice
adhesion values comparedwithmetallic aluminum, indicating
promising anti-icing behavior (Fig. 4).
CAN THERMALLY SPRAYED ALUMINUM (TSA)
MITIGATE CORROSION OF CARBON STEEL IN
CARBON CAPTURE AND STORAGE (CCS)
ENVIRONMENTS?
S. Paul and B. Syrek-Gerstenkorn
Transport of CO
2
for carbon capture and storage (CCS)
uses low-cost carbon steel pipelines due to their negligible
corrosion rates in dry CO
2
. However, in the presence of liquid
water, CO
2
forms corrosive carbonic acid. In order to mitigate
wet CO
2
corrosion, use of expensive corrosion-resistant alloys
is recommended; however, the increased cost makes such a
selection economically unfeasible. Therefore, new corrosion
mitigation methods are sought. One such method is the use
of thermally sprayed aluminum (TSA), which has been used to
Fig. 3 —
Cross-sectional images taken by light microscopy showing
the coating morphology across the non-MHP and MHP area at
sample (2,0).
Fig. 4 —
3D optical profiles of impact craters of flame-sprayed PE
coatings after high-velocity impact test at room temperature (RT).
JTST
HIGHLIGHTS
14