
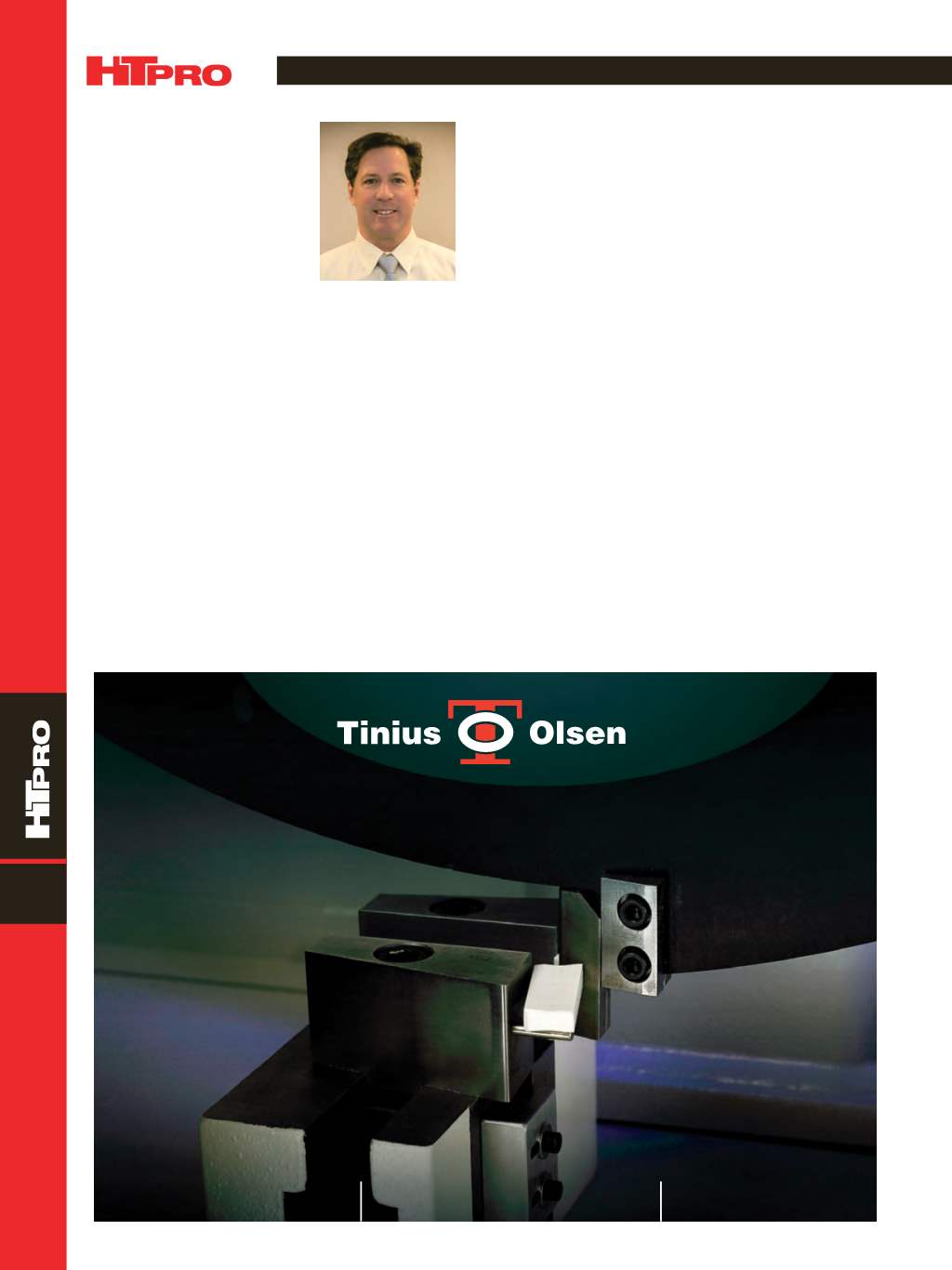
2
A D V A N C E D M A T E R I A L S & P R O C E S S E S | F E B R U A R Y / M A R C H 2 0 1 7
5 2
GUEST EDITORIAL
These new challenges push heat treaters to demand
innovation from equipment suppliers to deliver products
that can perform. In the induction heat treat world, the past
few years have seen advancements in use of multiple fre-
quencies, dual frequencies, computer-aided coil designs,
and FEA analysis to take the “Black Art” out of induction
heat treating. Going forward, a new power supply tech-
nology will provide an even higher level of capability by
enabling independent, stepless, and instant adjustment of
frequency and power during the heat cycle. This technol-
ogy may be the biggest change in the induction heat treat
industry since motor generators and tube oscillators.
State-of-the-art power supply technology allows
the physics and reference depth data of electromagnetic
induction to be coupled with innovative computer pro-
grams to “map out” the exact output necessary for precise
heat treating along vastly changing component geome-
tries. For example, precise heat treating specifications for
gears and half shafts will be able to be programmed, rather
than taking a trial and error approach.
With these new tools being offered to induction heat
treaters, we say to component designers, “Bring it on!”
Gary A. Doyon
President/CEO, Inductotherm Group
Chairman/CEO, Inductoheat Inc.
CHANGE CREATES
CHANGE
C
ars and airplanes. Two dif-
ferent modes of transporta-
tion, two essential products
undergoing radical designchanges
that demand new results from
heat treating providers in terms of
both equipment technology and process capabilities.
Airplanes are undergoing radical redesigns to improve
fuel efficiencies by 15-20% or lengthen range. Whether it
is a new geared turbofan engine or metallic components
throughout the aircraft and landing gear, use of smaller
metal parts and gears demands improved longevity and
lighter weight.
Automobiles are going through exhaustive redesign
every year to meet government fuel targets and custom-
er-driven expectations for higher MPG. Every metallic part
in the engine, drivetrain, frame, and safety and exhaust
systems is being revised to minimize weight and optimize
critical mechanical properties and residual stress dis-
tribution. It often seems that designers do not bother to
consider the practicalities involved in heat treating these
parts—as they add hole after hole, reduce cross sections,
and use “crazy” shapes and exotic alloys.
•
Tension
•
Compression
•
Flexure
•
Shear
•
Puncture
•
Melt index
•
Peel
•
Tear
•
COF
•
Impact
•
Vicat /HDT
•
Hardness
The first name in materials testing
All tests can be
performed in
accordance with
ASTM, ISO and
industry specific
standards
www.tiniusolsen.comsales@tiniusolsen.com
215 675 7100