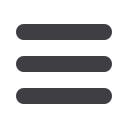
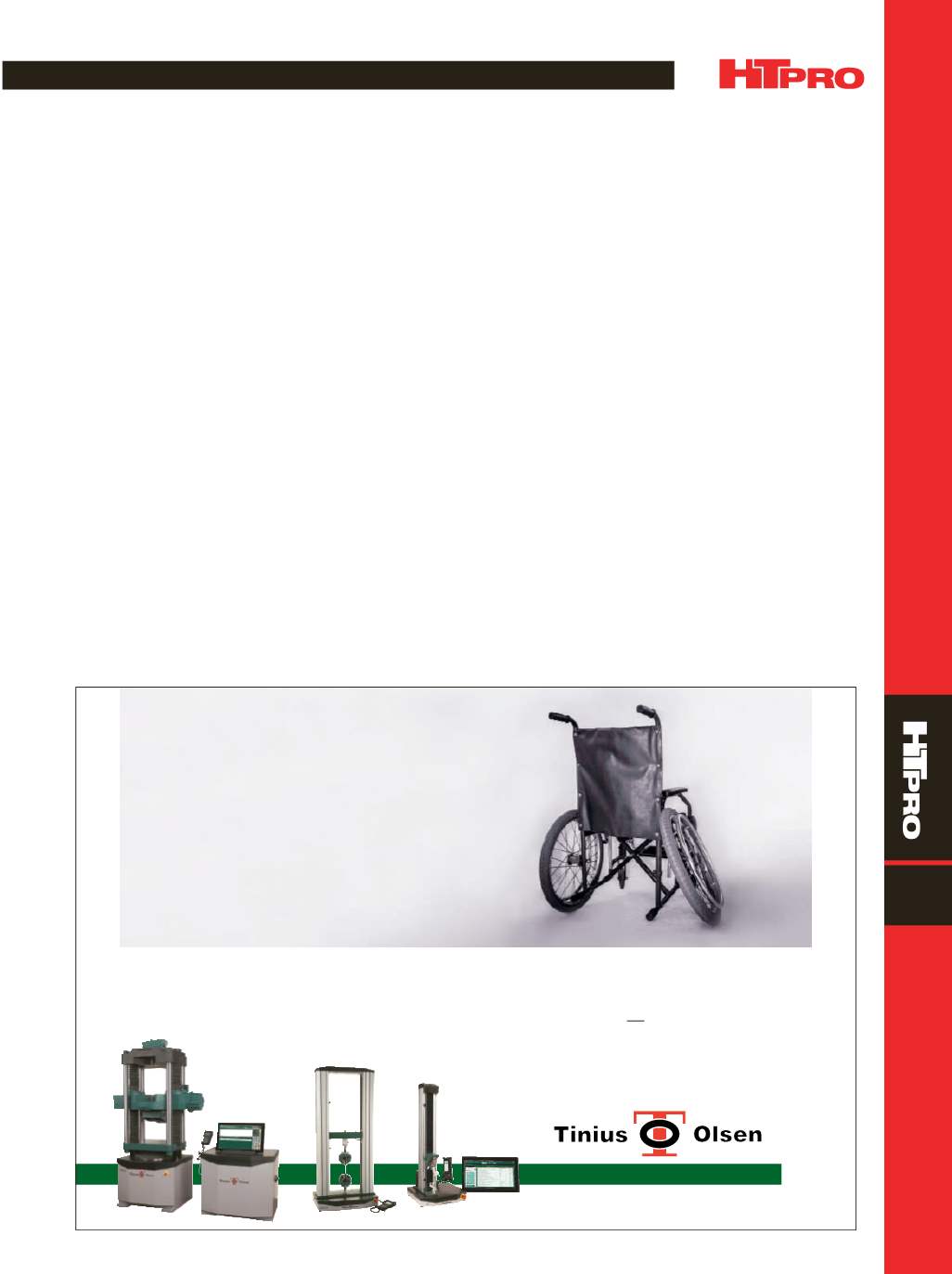
FEATURE
A D V A N C E D
M A T E R I A L S
&
P R O C E S S E S |
S E P T E M B E R
2 0 1 6
4 1
9
further possible answers would not help prevent a recur-
rence, reduce erratic results, or provide cost savings
[6]
.
Applying corrective actions.
After determining root
causes for all internal audit findings, the corrective action
taken to address the issuemust be defined and the timing of
the implementationcited. If a correctiveaction implemented
as a result of an internal audit has not yet been fully applied
due to time constraints, the Nadcap auditor might not write
an NCR for the same finding as long as you are working to
apply corrective actions. This depends on the exact finding,
as well as the auditor’s ability to later verify that the correc-
tive action was truly implemented.
For example, if a nonconformance was identified in
relation to a typographical error that had no product impact
in the calibration report for the overtemperature control-
ler, the root cause might be a lack of quality resources for
reviewing calibration reports. However, if the calibration ser-
vice provider is not available to correct the root cause within
the 30 days before the scheduled audit, it should be noted
in the internal audit report that the corrective action will be
fully implemented and verified during the next calibration
with the future date. After the official audit, the auditor will
verify that the corrective action was implemented by the
aforementioned date. Documenting the implementation of
any corrective actions after the internal audit is required as
auditorswill verify that the corrective actions are still inplace
during the official Nadcap audit. Generally, implementing
corrective actions for internal audit findings is one of the
final steps in performing an internal audit. After that, ensure
that all proper documentation from the internal audit is sub-
mitted to PRI at least 30 days before the official audit.
The final part of this series will discuss the official audit,
auditor interaction, and finishing the audit process.
For more information:
Nathan Durham is an electrical solu-
tions manager at Ipsen. For technical information, contact
technical@ipsenusa.comor 844.464.7736 (select 1). Ipsen
USA, 984 Ipsen Rd., Cherry Valley, IL 61016, ipsenusa.com.
References
1. Performance Review Institute, AC7102/8: Nadcap Audit
Criteria for Heat Treating Pyrometry, p 1, 2014.
2. Performance Review Institute, AC7102 Rev. H: Nadcap
Audit Criteria for Heat Treating, p 6, 2014.
3. P. Evans and E. Jacklin, Nadcap Supplier Tutorial, Per-
formance Review Institute, p 28, 2013.
4. Ibid.
5. Performance Review Institute, Root Cause Corrective
Action – Nadcap Style, p 1-11, 2014.
6. Ibid., 7.
www.TiniusOlsen.com The first name in materials testing. Like Humpty Dumpty, it is hard to put the pieces back together once a real world product quality disaster strikes. The ultimate cost of a recall will be far, far greater than any savings from cutting corners or not investing in a quality assurance program in the first place. With our broad spectrum of physical testing machines, software, and technical support, Tinius Olsen can help you assure quality from material to end product. To international standards and your toughest specifications. Reputations (yours and ours) depend on it. Busted! This company’s QA program AND reputation