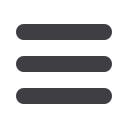
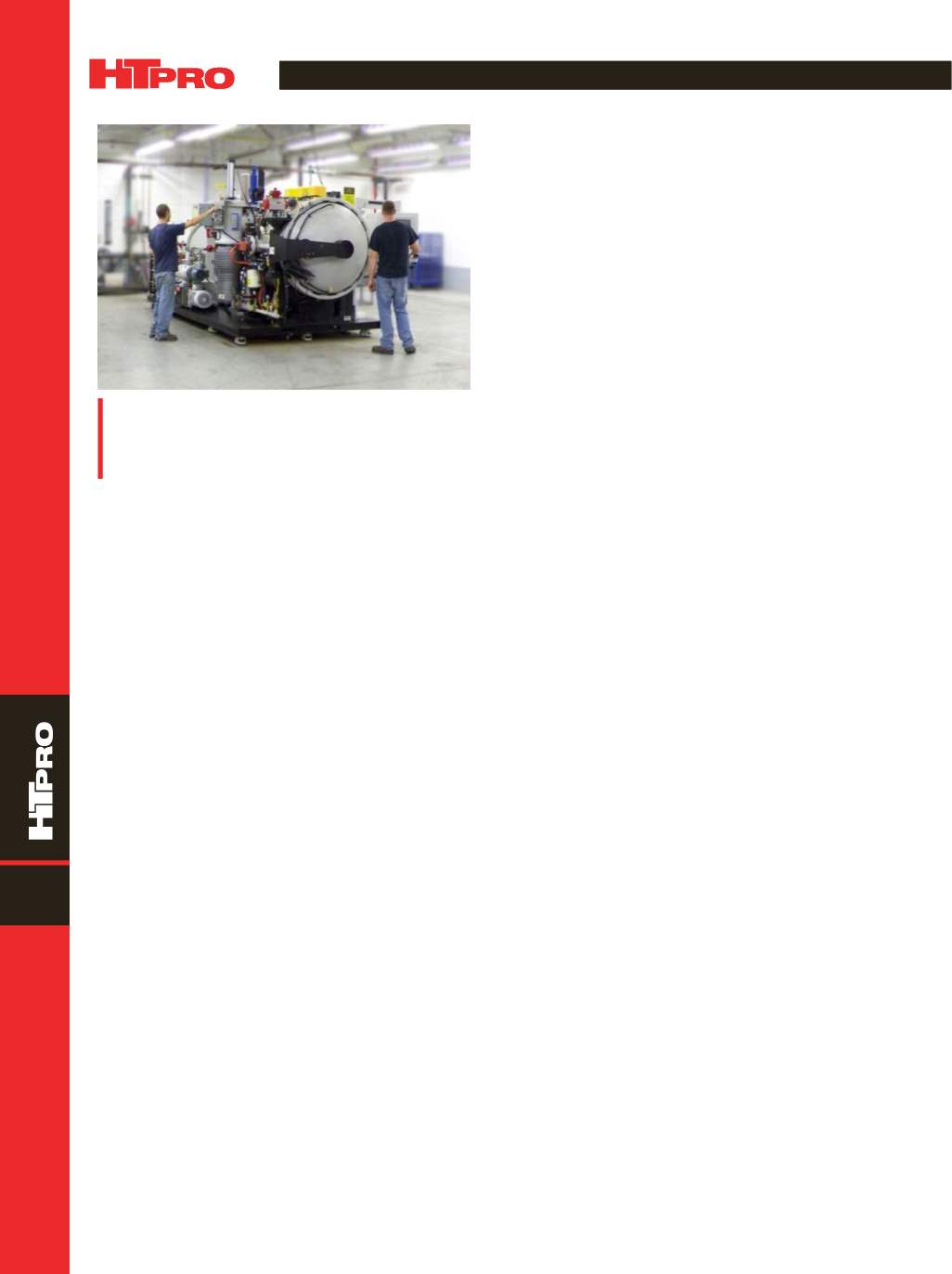
FEATURE
A D V A N C E D M A T E R I A L S & P R O C E S S E S | S E P T E M B E R 2 0 1 6
4 0
8
general knowledge of the processes that are run within
their company’s equipment, as well as having a procedure
in place for training, retraining, and periodic employee eval-
uations. The checklist question asks, “Do records indicate
that training is scheduled and attended in accordance with
procedures and documented…Do records indicate that the
evaluations are performed at documented frequencies and
the results reviewed with employees in a program of con-
tinuous improvement of personnel?”
[2]
. When reviewing this
question during a typical official audit, the auditor not only
wants to confirmthat procedures for training, retraining, and
evaluations are in place, but also verify that procedures state
the rate at which retraining and evaluations will occur.
Our experience with companies striving to receive Nad-
cap accreditation shows that not having documentation of
these events, or not having a procedure in place, will result
in a nonconformance as they are bothmajor findings. There-
fore, when creating procedures for training, retraining, and
evaluations, it is not only required that you include intervals
for retraining and retesting employees, but that you also
define these intervals and provide documentation.
Overall, nonconformances can result from a range of
oversights, from noncertified overtemperature thermocou-
ples to not documenting the uniformity tolerance at each
surveyed temperature. This is why it is imperative you eval-
uate every item referenced on the applicable Nadcap audit
checklists, AMS specifications, and PRI’s list of common non-
conformances prior to the official audit.
FINISHING THE INTERNAL AUDIT
After concluding the internal audit, the proper steps
outlined by PRI must be followed in preparation for the offi-
cial audit, including:
•
Reviewing findings (i.e., nonconformances)
•
Performing root-cause analysis
•
Implementing corrective actions
Reviewing findings.
A finding is essentially a nonconfor-
mance identified during the internal audit, or that the audi-
tor identifies during the official audit. Nonconformances are
classified as minor and major. A minor nonconformance is
“any single system failure or lapse in conformance with the
applicable standard or audit criteria”
[3]
. A major nonconfor-
mance is either “the absence of, or systemic breakdown of,
the process control and/or quality management system” or
“any nonconformance where the effect impacts or has the
potential to impact the integrity of the product”
[4]
. In other
words, a minor nonconformance is a small deviation from
Nadcap/AMS specifications or customer standards that does
not impact the product (e.g., a typographical error). By com-
parison, amajor nonconformance can imply a lack of control
over the process or product quality, or that the safety of the
product is significantly compromised. However, if a minor
nonconformance could affect the product (e.g., not having
a thermocouple calibration document on hand), then it
becomes a major nonconformance.
When reviewing findings of the internal audit, you
should prioritize the findings and establish the order in
which they should be addressed. Once this step is complete,
the root cause of each nonconformance should be deter-
mined. The recommended approach is to starting with the
most drastic finding(s), e.g., major nonconformance so as to
immediately ensure basic product safety and quality.
Performing root-cause analysis.
Determining a root
cause (i.e., the reason why a nonconformance occurred)
requires defining the “5-Whys” noted by PRI
[5]
. This helps
identify chronological events that led to the ultimate root
cause. If answers to the “why” questions are “as a result of”
or “because,” then the true root cause has not yet been iden-
tified and further investigation is required.
A commonmisconception concerning appropriate root
causes is that you can list the immediate contributing factors
or simply list human error (e.g., the operator did not adhere
to the correct process when positioning the load thermocou-
ples in the furnace). However, the root cause was not human
error. Rather, a more acceptable root cause might be that
a procedure was not in place to provide the operator with
appropriate training and retraining at regular intervals.
Consider how a root cause of an issue might be deter-
mined. For example, if the problem is that you were late to
work, you might ask yourself, “Why was I late?” An answer
of “the car wouldn’t start,” is a contributing cause, mean-
ing the true root cause has not yet been identified. As such,
more “why” questions are required (e.g., “why didn’t the
car start”) until the answers are no longer “as a result of” or
“because” and you discover the true root cause, such as “the
battery was old.” The true root cause has been found when
continuing to ask “why” no longer adds value, meaning any
During performance of the internal audit, it is important to
review past leak tests andmaintenance logs, as well as past
surveys, System Accuracy Tests, and industry specifications
for heat treatment. Courtesy of Ipsen.