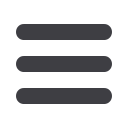
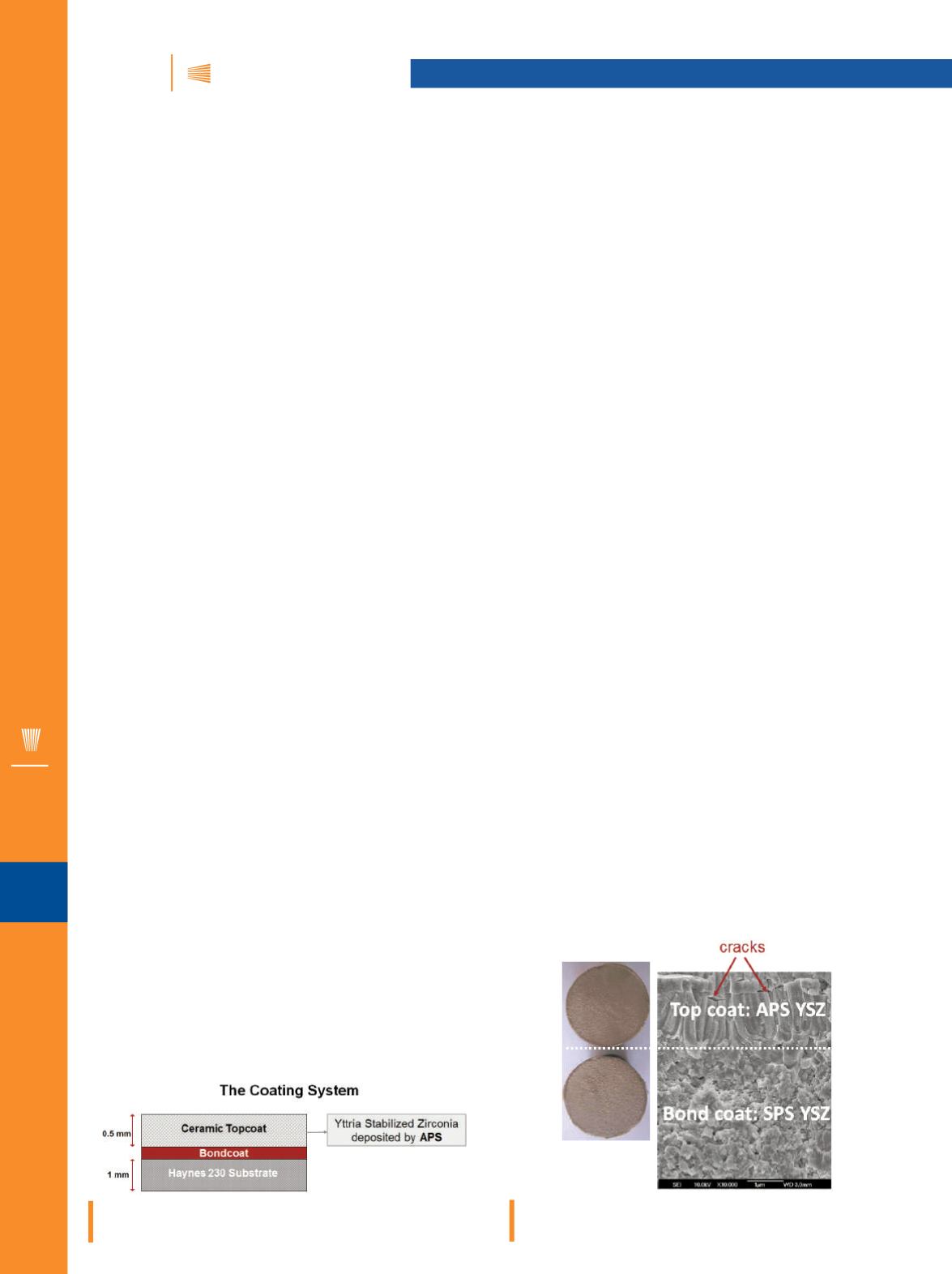
iTSSe
TSS
A D V A N C E D M A T E R I A L S & P R O C E S S E S | A P R I L 2 0 1 6
4 6
iTSSe
TSS
8
RESEARCH SPOTLIGHT
A
rmelle Vardelle, FASM, is a professor at the University
of Limoges, France. She is
co-chair of the Department
of Materials (Surface Treatments and Environment),
which trains roughly 120 engineering students in surface
and coating technologies
with an emphasis on saving ener-
gy and rawmaterials
. Her research interests include
thermal
spray and thermal plasma processes; modeling of plasma
processes and torch operation; transport and chemical rate
phenomena at high temperature; thermal spray coatings;
and green manufacturing. Vardelle has been a member of
TSS for more than 10 years and served on the TSS board
from 2009-2015. She was the lead editor of the
Journal of
Thermal Spray Technology
from 2009-2015 and is now the
chief editor. In addition, she is a
Fellow of both ASM Interna-
tional and
the International Plasma Chemistry Society.
As part of Vardelle’s research interests, she and her team
in the Laboratory of Science of Ceramic Processing and Surface
Treatments are developing thermal spray coatings for applica-
tion in fourth generation nuclear plants. This work is carried
out with CEA, the French Alternative Energies and Atomic En-
ergy Commission. France is involved in development of two
reactors, while six reactor concepts have been chosen by the
Generation IV Forum. France has decided to focus on two con-
cepts—sodium-cooled fast reactors (SFRs, reference system)
and gas-cooled fast reactors (GFRs, longer-term option). The
work with the SFR reactor is not yet finished, while the coating
systemdeveloped for theGFRhas resulted inapatentwithCEA.
GAS-COOLED FAST REACTORS
The Generation IV gas-cooled fast reactor (GFR) nuclear
system features a fast-neutron-spectrum and helium-cooled
reactor. It maximizes the usefulness of uranium resources by
breeding plutonium and can contribute to minimizing both
the quantity and radiotoxicity of nuclear waste by actinide
transmutation in a closed fuel cycle. The helium-cooled reac-
tor operates with an outlet temperature of 850°C and uses a
direct-cycle, helium turbine for electricity (42% efficiency at
850°C) and process heat for the thermochemical production
of hydrogen
[1,2]
. Challenging issues for the GFR design include
development of in-core and out-of-core materials capable
of resisting fast-neutron damage and high temperatures in
accident situations. Protective coatings are visualized to pro-
tect various parts of the system and also protect the system in
extreme cases where the functional temperature can increase
up to 1250°C and there is depressurization from 70 bars to at-
mospheric pressure.
Such coatings must withstand high temperature, de-
pressurization, and specific conditions of wear linked to ero-
sion by high-speed (about 280 m/s) helium gas flow. They
wouldbedepositedonmaterials1mmthickthatareresistant
to heat and erosion and exhibit stable mechanical proper-
ties at high temperatures, e.g., Haynes 230, a solid solution-
strengthened nickel-base alloy. This work involves a
double-layer plasma-sprayed zirconia coating for protecting
the out-of-core metal alloy structures against depressuriza-
tion events. The coating system consists of a thin nanostruc-
ture layer and a thick microstructure layer. The first layer
deposited by suspension plasma spraying provides adhesion
of the coating on the smooth and thin (1-mm thick) metal
(Haynes) substrate while the top layer, deposited by conven-
tional plasma spraying, acts as a thermal barrier coating.
CERAMIC COATINGS
Ceramic coatings deposited by plasma spraying are po-
tential candidates for use as protective coatings. However,
both the procedures used to prepare the substrate before
deposition and the spray process itself must be adapted to
the thinness of the substrate and its low surface roughness
(average roughness, Ra, of 0.4
µ
m). The principal objective
of surface preparation is to achieve proper adhesion of the
thermal spray coating to the substrate. The procedure gener-
ally combines abrasive blastingwith other surface preparation
techniques to create the appropriate degree of surface clean-
liness and roughness. However, roughening of the surface by
grit-blasting induces compressive stresses that bring about a
THERMAL SPRAY COATINGS FOR
NUCLEAR PLANTS
Coating systemdeposits yttria stabilized zirconia (YSZ) using
atmospheric plasma spraying (APS).
ASTM C633 tensile testing shows that the point of failure occurs
close to the interface between the ceramic layers.