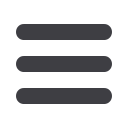
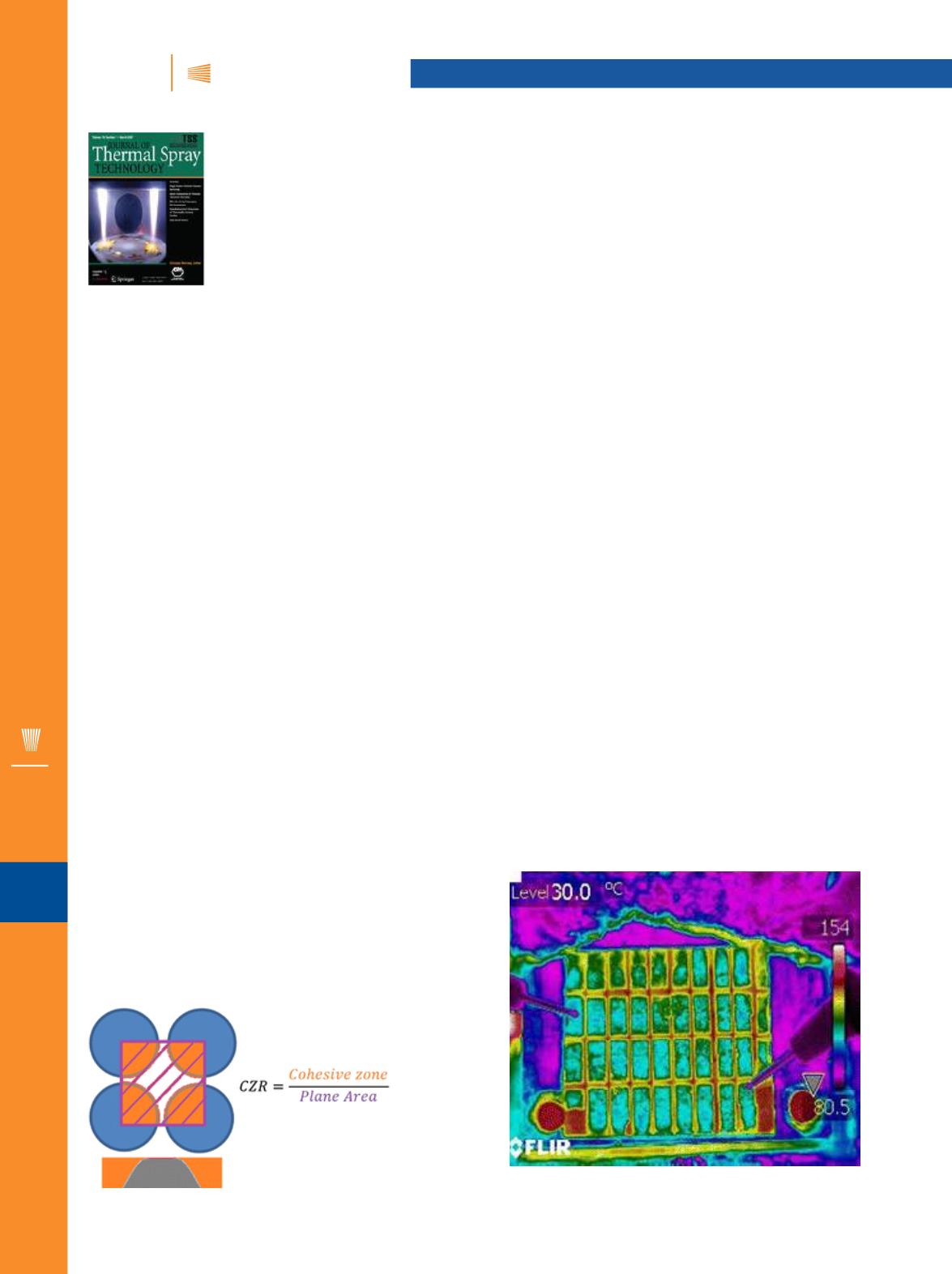
iTSSe
TSS
A D V A N C E D M A T E R I A L S & P R O C E S S E S | A P R I L 2 0 1 6
5 0
iTSSe
TSS
12
JTST
HIGHLIGHTS
The
Journal of Thermal Spray Technolo-
gy (JTST),
the official journal of the ASM
Thermal Spray Society, publishes con-
tributions on all aspects—fundamental
and practical—of thermal spray science,
including processes, feedstock manu-
facture, testing, and characterization.
As the primary vehicle for thermal spray
information transfer, its mission is to syn-
ergize the rapidly advancing thermal spray industry and relat-
ed industries by presenting research and development efforts
leading to advancements in implementable engineering appli-
cations of the technology. Articles from the February and April
issues, as selected by
JTST
Editor-in-Chief Armelle Vardelle, are
highlighted here. In addition to the print publication,
JTST
is
available online through
springerlink.com. For more informa-
tion, visit
asminternational.org/tss.“LASER PATTERNING PRETREATMENT
BEFORE THERMAL SPRAYING: A TECHNIQUE
TO ADAPT AND CONTROL THE SURFACE
TOPOGRAPHY TO THERMOMECHANICAL
LOADING AND MATERIALS”
Robin Kromer, Sophie Costil, Jonathan Cormier, Laurent
Berthe, Patrice Peyre, and Damien Courapied
Coating characteristics are highly dependent on sub-
strate preparation and spray parameters. Hence, the surface
must be adaptedmechanically andphysicochemically to favor
coating-substrate adhesion. Conventional surface preparation
methods such as grit blasting are limited by surface embrittle-
ment and produce large plastic deformations throughout the
surface, resulting in compressive stress and potential cracks.
Among all such methods, laser patterning is suitable to pre-
pare the surface of sensitive materials. No embedded grit par-
ticles canbe observed, andhigh-quality coatings are obtained.
Finally, laser surface patterning adapts the impacted surface,
creating large anchoring area. Optimized surface topogra-
phies can then be elaborated according to thematerial as well
as the application. The objective of this study is to compare
the adhesive bond strength between two surface preparation
methods, namely grit blasting and laser surface patterning,
for two material couples used in aerospace applications: 2017
aluminum alloy and AISI 304L stainless steel coated with NiAl
and YSZ, respectively. Laser patterning significantly increases
adherence values for similar contact area due to mixed-mode
(cohesive and adhesive) failure. The coating is locked in the
pattern (Fig. 1).
“THERMOELECTRIC DEVICE FABRICATION
USING THERMAL SPRAY AND LASER
MICROMACHINING”
Mahder Tewolde, Gaosheng Fu, David J. Hwang, Lei Zuo,
Sanjay Sampath, and Jon P. Longtin
Thermoelectric generators (TEGs) are solid-state devic-
es that convert heat directly into electricity. They are used in
many engineering applications such as vehicle and industrial
waste-heat recovery systems to provide electrical power, im-
prove operating efficiency, and reduce costs. State-of-the-art
TEG manufacturing is based on prefabricated materials and
a labor-intensive process involving soldering, epoxy bonding,
and mechanical clamping for assembly. This reduces their du-
rability and raises costs. Additivemanufacturing technologies,
such as thermal spray, present opportunities to overcome
these challenges. In this work, TEGs have been fabricated for
the first time using thermal spray technology and laser micro-
machining. The TEGs are fabricated directly onto engineering
component surfaces. First, current fabrication techniques of
TEGs are presented. Next, the steps required to fabricate a
thermal spray-based TEG module, including the formation of
the metallic interconnect layers and the thermoelectric legs,
are presented. A technique for bridging the air gap between
two adjacent thermoelectric elements for the top layer using
a sacrificial filler material is also demonstrated. A flat 50.8 mm
× 50.8 mm TEG module is fabricated using this method, and
its performance is experimentally characterized and found to
be in agreement with expected values of open-circuit voltage
based on the materials used (Fig. 2).
Fig. 1 —
Cohesive zone ratio computation.
Fig. 2 —
Measurement of top-side temperature with an infrared
camera.