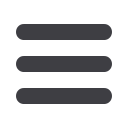
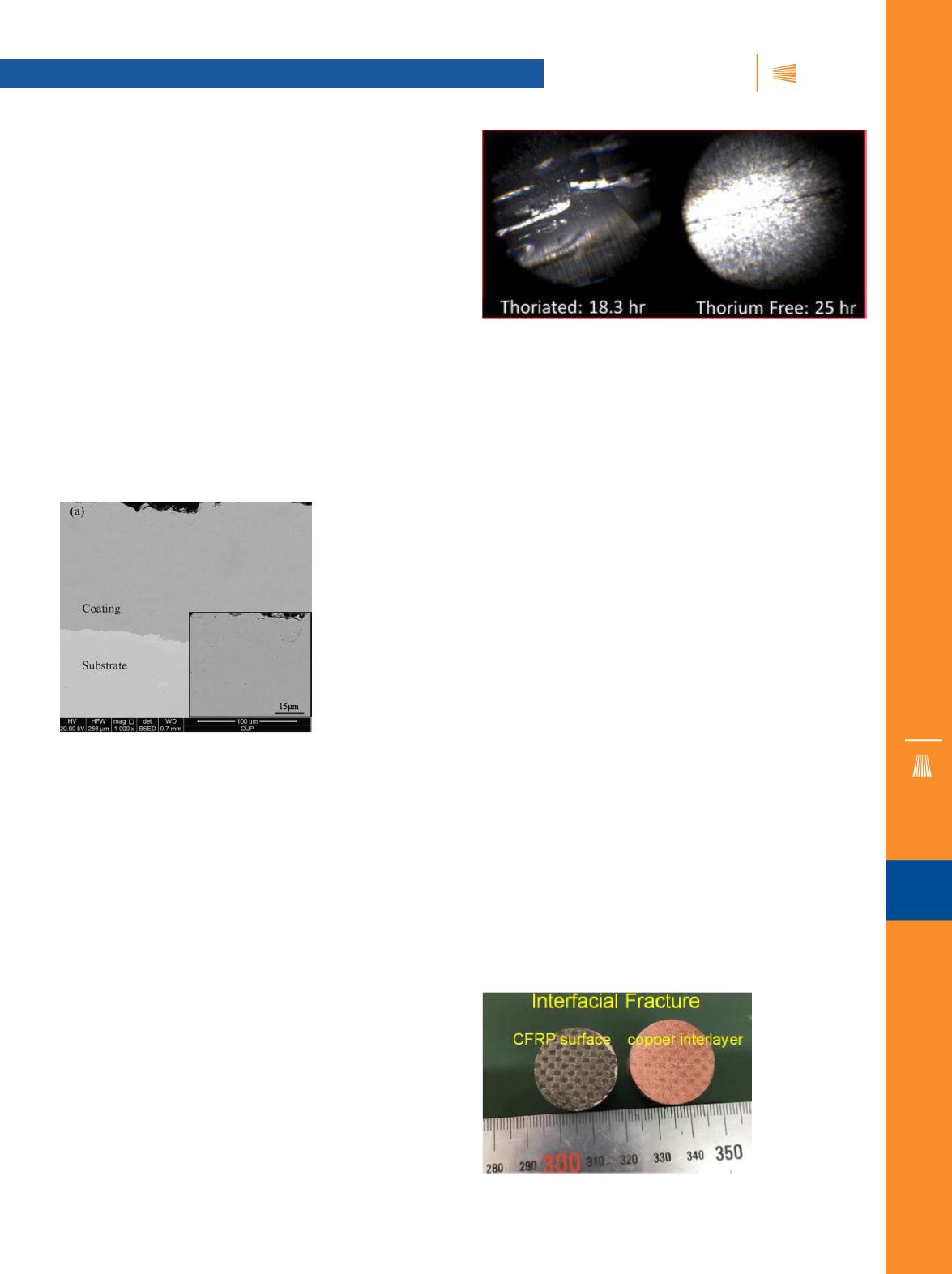
iTSSe
TSS
A D V A N C E D
M A T E R I A L S
&
P R O C E S S E S |
A P R I L
2 0 1 6
5 1
JTST
HIGHLIGHTS
13
iTSSe
TSS
“HOTCORROSIONBEHAVIOROFLOW-PRESSURE
COLD-SPRAYED CoNiCrAlY COATINGS”
L.W. Zhang, X.J. Ning, L. Lu, Q.S. Wang, and L. Wang
CoNiCrAlY coatings were deposited by low-pressure cold
spraying and pre-oxidized in a vacuum environment, and its
hot corrosion behavior in pure Na
2
SO
4
and 75 wt% Na
2
SO
4
+
25 wt% NaCl salts was investigated. The pre-oxidation treat-
ment resulted in the formation of a dense and continuous
α
-Al
2
O
3
scale on the coating surface. After being corroded for
150 h at 900°C, the pre-oxidized coating exhibited better corro-
sion resistance to both salts than the as-sprayed coating. The
presence of preformed Al
2
O
3
scale reduced the consumption
rate of aluminum by delaying the formation of internal oxides
andsulfides andpromoting the formationof adenser andmore
adherent Al
2
O
3
scale. Moreover, we investigated the corrosion
mechanismof cold-sprayed CoNiCrAlY coatings in the two salts
and discussed the effect of the pre-oxidation treatment (Fig. 3).
“MICROSTRUCTURE AND MECHANICAL
PROPERTIES OF WARM-SPRAYED TITANIUM
COATING ON CARBON FIBER REINFORCED
PLASTIC”
Amirthan Ganesan, Okada Takuma, Motohiro Yamada,
and Masahiro Fukumoto
Polymer materials are increasingly dominating various
engineering fields. Recently, polymer-based composite mate-
rials’ surface performances—in particular, surfaces in relative
motion—have been improved markedly by thermal spray coat-
ing. Despite this recent progress, thedepositionof high-strength
materials—producing a coating thickness on the order of more
than500
μ
m—remainshighlychallenging. In thepresentwork, a
highly dense and thick titaniumcoatingwas successfully depos-
ited onto the carbon fiber reinforced plastic (CFRP) substrate
using a newly developed high-pressure warm spray (WS) sys-
tem. The coating properties, such as hardness (300 ± 20 HV) and
adhesion strength (8.1 ± 0.5 MPa), were evaluated and correlat-
ed with the microstructures of the coating. In addition, a wipe-
test and in situ particle velocity and temperaturemeasurement
wereperformed tovalidate theparticledepositionbehavior as a
function of the nitrogen flow rate in awarmspray system. It was
found that the microstructures, deposition efficiency (DE), and
mechanical properties of the coatings were highly sensitive to
nitrogen flowrates. The coatingporosity increasedwith increas-
ing nitrogen flow rates; however, the highest density was ob-
served for nitrogen flow rate of 1000 standard liters per minute
samples (SLM) samples due to the high fraction of semi-molten
particles in the spray stream (Fig. 5).
Fig. 3 —
Cross-sectional BSE images of as-sprayed coating.
“THORIUM-FREE VERSUS THORIATED PLASMA
GUN ELECTRODES: STATISTICAL EVALUATION
OF COATING PROPERTIES”
Jose Colmenares-Angulo, Ronald Molz, David Hawley, and
Ramachandran Chidambaram Seshadri
Industries throughout the world today have an increased
awareness of environmental, health, and safety issues. This,
together with recent Nuclear Regulatory Commission changes
concerning sourcematerial (e.g., thorium) has addedcomplex-
ity in the supply chain of thoriated tungsten commonly used in
plasma spray gun spares. In the interest of a safer and more
sustainable work environment, Oerlikon Metco has developed
thorium-free material solutions proven to have longer service
life than conventional thoriated spares. This work reports on
the effect, if any, caused by tungsten compositional changes
and extended service life in coating properties. Microstructure,
coating efficiency parameters, hardness, particle state, in situ
coating stress, and ex situmodulus are evaluated over the ser-
vice life duration of the nozzle, comparing coatings with thori-
ated and non-thoriated nozzles and electrodes with the same
spray parameters (Fig. 4).
Fig. 4 —
Borescope image comparison of thoriated and
thorium-free nozzles after testing.
Fig. 5 —
Fracture surface of adhesion
strength samples
.