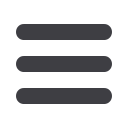
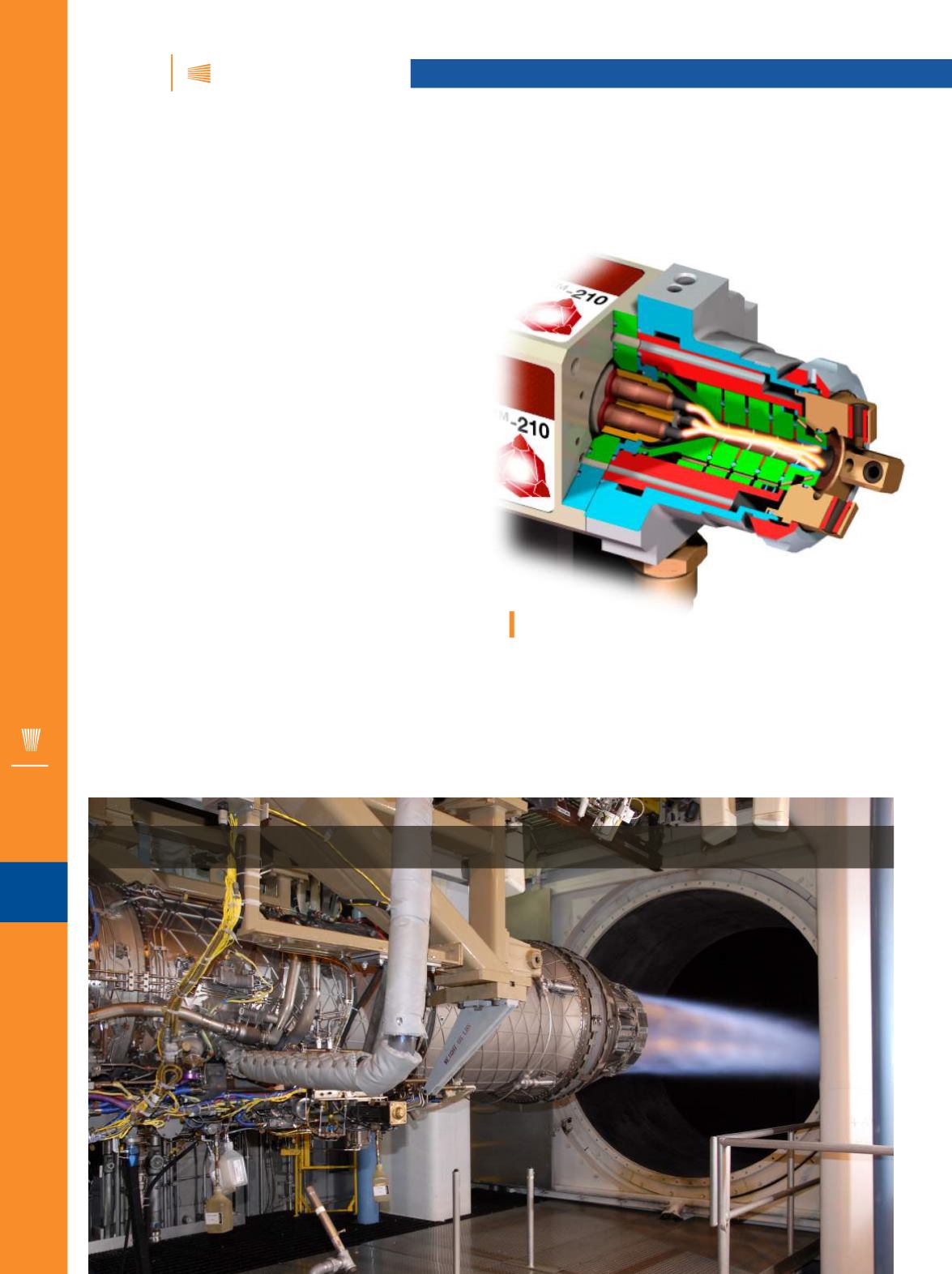
iTSSe
TSS
A D V A N C E D M A T E R I A L S & P R O C E S S E S | A P R I L 2 0 1 6
4 4
iTSSe
TSS
6
CASE STUDY
REASON TO CONSIDER SURFACING
Today’s aero gas turbine engines employ higher-
pressure ratios and higher turbine inlet temperatures to
improve efficiencies. Thermal barrier coating (TBC) sys-
tems consist of a heat-insulating ceramic coating such as
a yttrium-stabilized zirconium oxide applied over an
oxidation-resistant metallic bond coat, usually an MCrAlY,
that results in reduced heat transfer to the base material.
Benefits include improved mechanical properties and ad-
ditional life expectancy. TBCs are widely specified and their
use abounds throughout the hot section of modern turbines
on transition ducts, combustors, heat shields, nozzle guide
vanes, blades, and augmenters (afterburners).
Augmenters are used almost exclusively on military air-
craft turbine engines, an example of which is the F100 engine
that powers F-15 and F-16 military aircraft. Here, already hot
exhaust gases are reignited to burn residual fuel, giving the air-
craft additional thrust when needed. The TBC system ensures
the service life and mission-readiness of the augmenter, both
of which would be severely degraded without it.
VALUE OF COATING
The F100 augmenter is a large part with an interior sur-
face area (depending on the engine model) of approximately
6.3 m
2
(68 ft
2
). The MCrAlY bond coat (Amdry 9622) is applied
FASTER THERMAL BARRIER COATING
APPLICATION ON MILITARY
AIRCRAFT AUGMENTERS
to a thickness of 0.075 to 0.125 mm (0.003 to 0.005 in.) and
the top coat (Metco 204NS) is applied 0.2 to 0.3 mm (0.008 to
0.010 in.) thick. Although the overall coating thickness is rela-
tively thin for a TBC coating, spray process times are quite long
as a result of the large part size. Using conventional plasma
F100 engine in the test cell. Courtesy of Arnold AFB AEDC.
Cascading arc technology.