
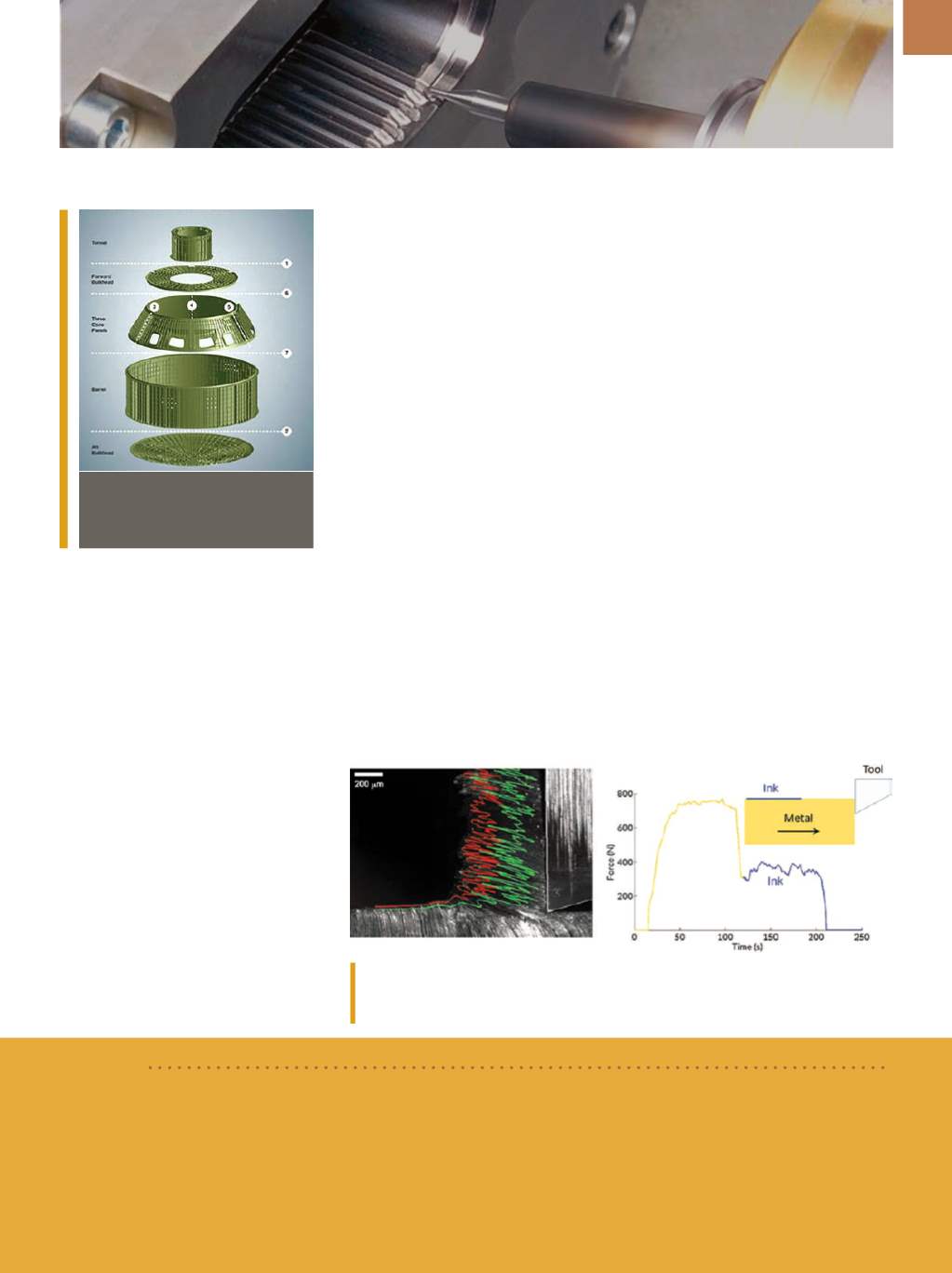
A D V A N C E D
M A T E R I A L S
&
P R O C E S S E S |
N O V E M B E R / D E C E M B E R
2 0 1 5
1 3
PROCESS TECHNOLOGY
the metal during fabrication. Prior to
beginning work on the pieces destined
for space, technicians practiced their
process, refined their techniques, and
ensured proper tooling configurations
by welding together a pathfinder, a full-
scale version of the current spacecraft
design. NASA’s prime contractor for the
spacecraft, Lockheed Martin, is working
on the crew module at Michoud. The
number of welds for the crew module
was reduced by more than half since
the first test version of Orion’s primary
structure was constructed and flown
on the Exploration Flight Test-1 last
December. The Exploration Mission-1
structure will include just seven main
welds, reducing weight.
nasa.gov/orion.CONTROLLING SINUOUS
FLOW SAVES ENERGY
Discovery of a previously unknown
type of metal deformation called sinu-
ous flow could lead to more efficient
machining by reducing the force and
energy required to process metals, say
researchers at Purdue University, West
Lafayette, Ind. The team discovered the
phenomenon by using high-speed mi-
crophotography and analysis to study
what happens while cutting ductile
metals. They found that the metal is de-
formed into folds while it is being cut—
contrary to assumptions that metals
are sheared uniformly—and also that
sinuous flow can be controlled by sup-
pressing the folding behavior.
Results show that cutting force
can be reduced by 50% simply by paint-
ing the metal with a standard marking
ink. Because the painted layer is found
to suppress sinuous flow, not only can
energy consumption be reduced by
50%, but also machining can be done
faster and with improved surface qual-
ity, says Srinivasan Chandrasekar, pro-
fessor of industrial engineering. In one
set of experiments, only half of a sam-
ple was inked. When the cutting tool
reached the inked portion, the amount
of force dropped immediately by half.
purdue.edu.
Orion’s primary structure and the
order in which it will be welded
together. Courtesy of NASA.
ORION SPACECRAFT
COMING TOGETHER
Technicians at NASA’s Michoud As-
sembly Facility in New Orleans welded
together the first two segments of the
Orion crew module that will fly atop
NASA’s Space Launch System (SLS)
rocket on a mission beyond the moon.
The primary structure of Orion’s crew
module is made of seven large alumi-
numpieces thatmust bewelded togeth-
er. The first weld connects the tunnel to
the forward bulkhead, which houses
critical systems such as parachutes
that deploy during reentry. The tunnel
will allow workers to move between the
crew module and other spacecraft.
Toprepare forwelding, technicians
cleaned the segments, coated them
with a protective chemical, and primed
them. Next, each element was outfitted
with strain gauges and wiring to monitor
Sinuous flow, left, shows that metal is deformed into folds while it is being cut. New research,
right, reveals that cutting force can be reduced 50% by painting metal with a standardmark-
ing ink. Courtesy of Purdue.
BRIEFS
H.C. Starck,
Germany, acquired a minority stake in
Metasphere Technology,
Sweden. Metasphere developed a new
technology for producing spherical metal powders for use in additive manufacturing and other fields. The companies
will build a new production line in Lulea, Sweden.
hcstarck.com.
United Technologies Corp.,
Hartford, Conn., will sell its Sikorsky Aircraft business to
Lockheed Martin Corp.,
Bethesda, Md., for $9 billion in cash. The transaction is projected to close by year-end or in the first quarter of 2016.
lockheedmartin.com.