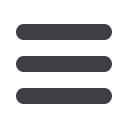
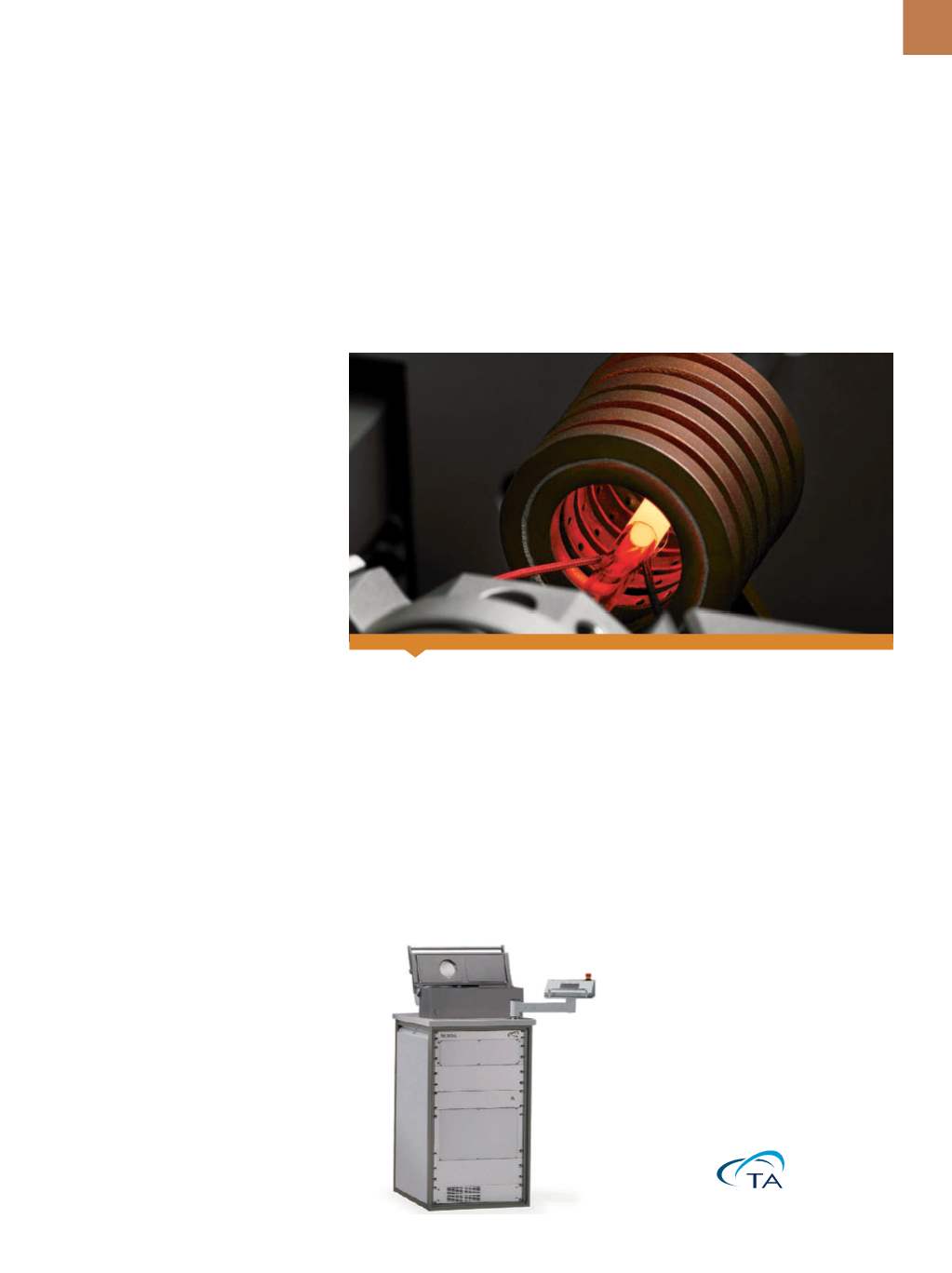
A D V A N C E D
M A T E R I A L S
&
P R O C E S S E S |
S E P T E M B E R
2 0 1 5
2 5
a stream of gas in a two-story chamber,
resulting in spherical particles. Helium,
argon, and ultimately nitrogen were
all used as atomization gases. An SEM
micrograph of atomized Be powder is
shown in Fig. 7.
Spherical particles pack together
with no relation to crystal orientation.
Because each particle is randomly ori-
ented, no large regions can develop.
Properties level themselves out, lead-
ing to an essentially uniform surface.
In conjunction with HIP consolidation,
this results in a predictable mirror
with equal thermal contraction in all
directions. In addition, oxide particles
degrade the performance of a mirror
because each oxide particle acts as a
separate scattering source. Therefore,
lower oxide translates into improved
optical performance. The solid optical
blanks made from the atomized optical
grade of beryllium powder, O-30, have
less than 0.35% beryllium oxide. Recall
that I-70A and S-200F have 0.7% and
1% oxide respectively. Atomized pow-
der is therefore an excellent choice for
a mirror material
[7]
.
Once the powder is made, it is
compacted into a solid. Historically,
powder was vacuum hot pressed into
solid cylinders ranging from roughly
8 to 72 inches in diameter. Aerospace
components requiring the highest level
of stiffness to density were made from
these cylinders. For example, the Space
Shuttle umbilical doors were machined
from large-diameter hot pressed cyl-
inders, as were the window frame,
brakes, and navigation base. The
Advanced Inertial Reference Spheres
(AIRS) of the Peacekeeper ICBM (inter-
continental ballistic missile) were
likewise machined from vacuum hot
pressed beryllium. This hot pressing
method leaves less than 0.5% voids,
but does not totally eliminate them.
For the JWST Telescope, all voids had
to be eliminated, leading to use of hot
isostatic pressing (HIP)
[2]
.
Although HIP was developed by
Battelle at its Columbus, Ohio, head-
quarters in the 1940s for cladding nu-
clear reactor fuel rods, its uses have
greatly expanded to include casting
densification, powder consolidation,
and diffusion bonding. In HIP, powder
is poured into a metal can that is evacu-
ated and sealed. This is then placed into
the HIP unit, which is pressurized with
argon and heated. A typical pressure
compressing the can and its contents is
15,000 to 30,000 psi and temperatures
to 2000°C can be applied. The solid
that emerges after the can is removed
is completely free of voids. Another ad-
vantage of HIP is that the pressure is ap-
plied in all directions so it maintains the
non-directionality of the final product
better than uniaxial vacuum hot press-
ing. The microstructure of consolidated
O-30 is shown in Fig. 8.
Technologists who worked on mir-
rors in the 1960s reported that beryllium
atomization trials were unsuccessful. In
particular,veryhighoxidelevelsresulted.
Much effort was spent making certain
that the new atomizer was airtight to
control the oxygen level. HIP’ing beryl-
lium powder had also been tried, but
failed because voids were formed when
Discover More Steel Research Capability www.tainstruments.com DIL 805 Quenching and Deformation Dilatometer The DIL 805-series quenching and deformation dilatometers provide the most accurate measurements over the widest range of heating, cooling,anddeformationconditions,allowingforthemostsophisticated characterization and optimization of steel processing conditions. The DIL 805 provides critical data for the construction of time-temperature- transformation (TTT) , continuous-cooling-transformation (CCT) , and time-temperature-transformation after deformation (DTTT) diagrams as well as stress-strain curves. Powerful inductive heating and an innovative helium quench system enable heating rates up to 4000 K/s and quenching rates as high as 2500 K/s to capture the extremes of modern processing conditions.