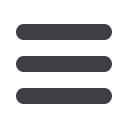
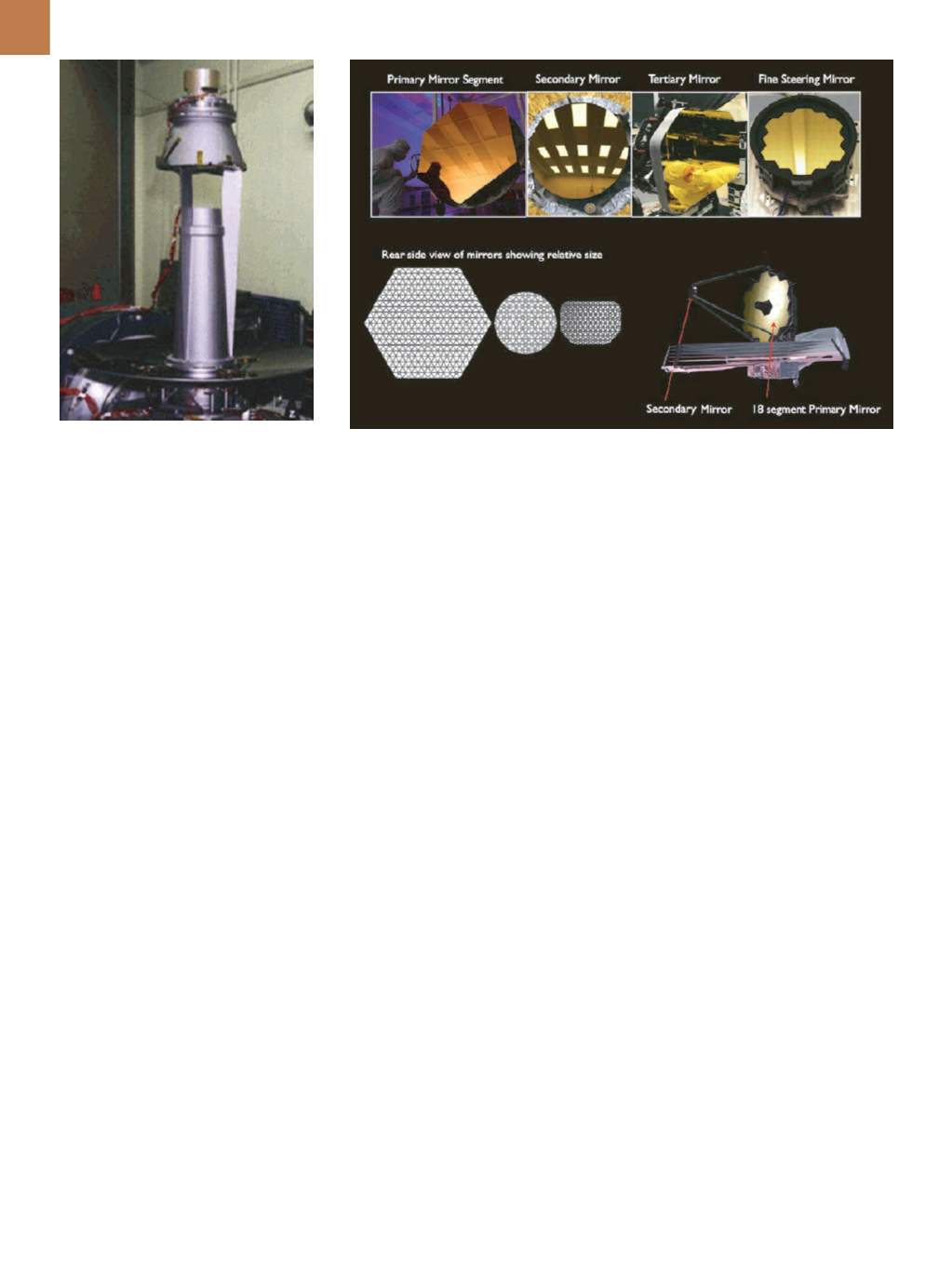
A D V A N C E D M A T E R I A L S & P R O C E S S E S | S E P T E M B E R 2 0 1 5
2 4
Fig. 5 —
Prototype SIRTF telescope under-
going random vibration testing
[5]
.
Fig. 6 —
James Webb Space Telescope and its mirrors
[6]
. Bottom right shows an artist’s concep-
tion of the telescope optics with 18 primary mirror segments. On the bottom row are the three
different mirror segments as seen from the rear showing the honeycomb structure that makes
themboth light and stiff.
a vacuum deposited gold coating,
1000 Å thick. The convex secondary
mirror, though much more difficult to
polish and measure, has a similar figure
accuracy.
BERYLLIUM POWDER:
HISTORICAL DEVELOPMENT
Beryllium processing traditionally
starts with vacuum melting and casting
as part of the refining process. Vacuum
melting removes residual magnesium
and oxides that might be carried over
from the reduction of beryllium hydrox-
ide into metallic Be. Newly refined as
well as recycled Be are input to the vac-
uum casting step. Statically cast beryl-
lium features a typical ingot structure,
with large columnar grains growing
inward from the ingot wall and resid-
ual porosity toward the center. This
results in property anisotropy, difficulty
in machining, and overall poor proper-
ties. However, machining the ingot into
chips prior to powder processing helps
improve properties.
Powder metallurgy was used in
the late 1940s to produce fine grained,
nearly random-structured material.
The more random grain and crystal ori-
entation improves isotropy, particularly
the coefficient of thermal expansion,
while the finer grain size also improves
mechanical properties. In the 1940s and
50s, beryllium powder was produced
by two different processes—ball and
attrition milling. Ball milling uses a
rotating canister filled with chips and
grinding media generally made of hard-
ened steel. Beryllium was crushed and
sheared into fine powder flakes, but
this was a costly batch operation and
resulted in iron contamination from the
grinding media. Attrition milling was a
continuous process in which beryllium
chip was fed into a device similar to old
flour mills. The chip passed between
rotating and stationary berylliumplates
and was sheared into powder particles.
The weakest orientation of the Be crys-
tal is the basal plane and this process
produced powder particles with a slight
flake-like structure by fracture on the
basal plane.
Impact grinding to produce beryl-
lium powder was introduced as a
production process in the late 1970s
and uses high velocity gas to propel
Be chips against a Be target. The air
is dried, and then cools as it expands
from the nozzle. The impact shatters
the chips into powder particles, which
exhibit a blockier shape than ball or
attrition milled powder. This process
was also semi-continuous because
oversized powder particles could be
separated by air elutriation and fed
back into the impact stream. This
process improvement reduced iron and
oxygen contamination, and produced a
powder shape less related to the crys-
tal structure than other processes. This
was important during vibratory loading
of containers in preparation for consol-
idation into a solid. The flat surfaces of
flakes are all basal planes. When flakes
are loaded into a press to consolidate
them, they can stack up like a deck
of cards or sheets of mica, with large
regions having the same crystal orien-
tation. Each of these regions behaves
differently than adjoining regions with
different orientations. When the solid,
polished mirror cools, the difference
between regions gives the surface an
orange-peel appearance, which means
that each region is reflecting a beam of
light at a slightly different angle, scat-
tering the beam rather than reflecting
it in one uniform direction. Each time
the mirror is warmed and cooled, these
regions actually deform one another
slightly. Scattering is unpredictable
and changes on each cooling cycle.
Therefore, additional polishing is not a
solution.
The process that made the most
sense for making powder was inert
gas atomization, developed in the late
1980s for beryllium. A stream of liquid
metal is blasted into small droplets by