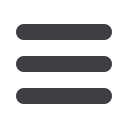
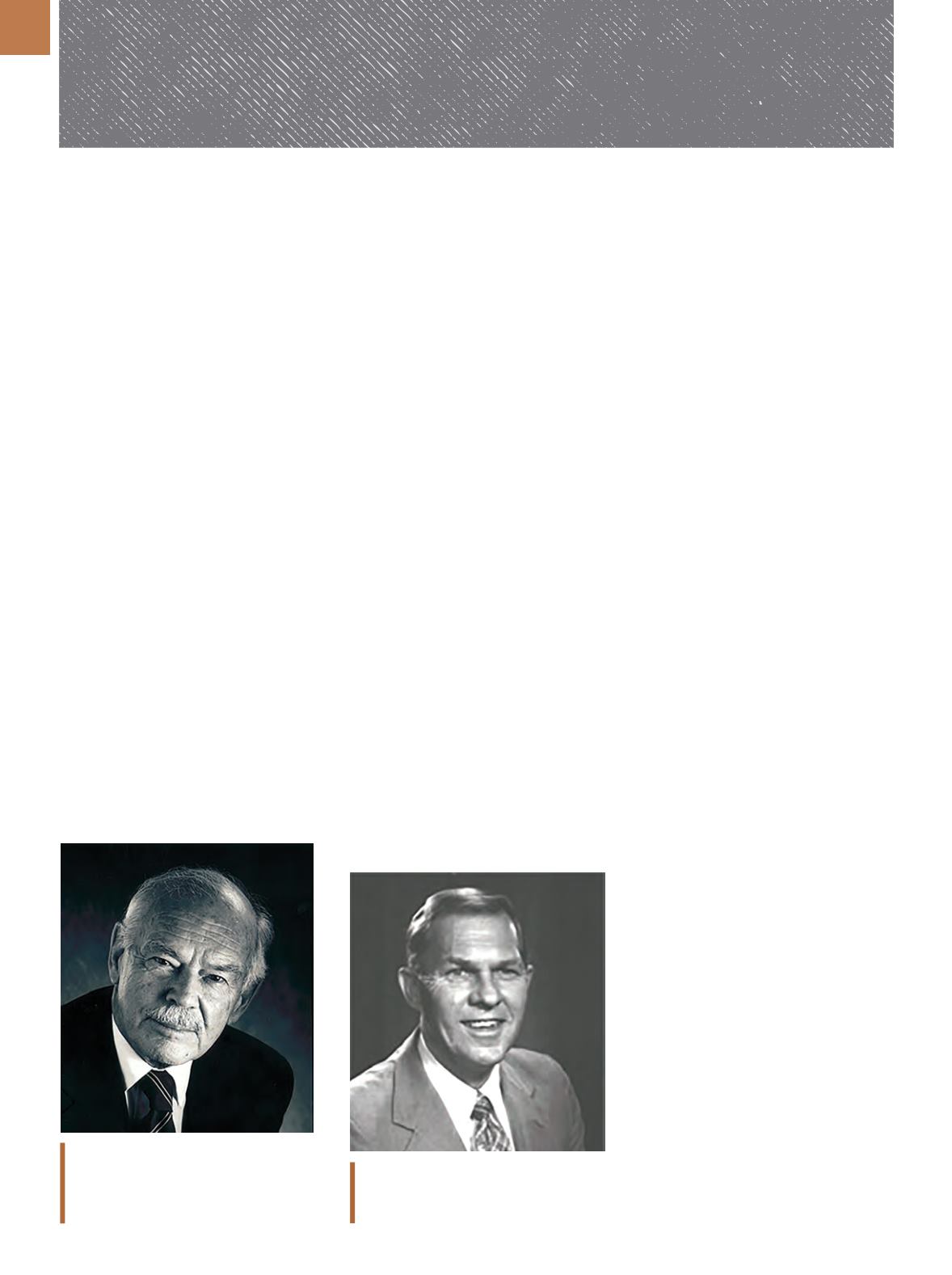
A D V A N C E D M A T E R I A L S & P R O C E S S E S | J U N E 2 0 1 5
2 8
METALLURGY LANE
Metallurgy Lane, authored by ASM life member Charles R. Simcoe, is a continuing series dedicated to the early history of the U.S.
metals and materials industries along with key milestones and developments.
STEEL MINIMILLS—PART I
FROM 1900 TO 1960, THERE WAS LITTLE CHANGE IN THE STEELMAKING INDUSTRY.
STEEL MINIMILLS CAME ON THE SCENE IN THE LATE 1960s.
F
rom 1900 to 1960, there was not
much change in the steelmaking in-
dustry. Thebusinesswas dominated
by a few large companies, led by United
States Steel Corp. Steel minimills came
on the scene in the late 1960s and into
the 1970s. Besides being much smaller
than the big mills, minimills feature three
distinct factors that set them apart: Only
scrap is used in the charge for the melting
furnaces; electric arc furnaces (EAFs) are
used formelting; andsteel is solidified into
billets using continuous casting, which
feeds billets directly into the rolling mills.
Scrap had been melted in EAFs since the
early part of the 20th century, but only for
making tool steels, high alloy steels, and
stainless steelswhere scraphad tobehigh
quality to meet specifications. Scrap was
also used in large quantities in the open
hearth process to make ordinary carbon
steels and engineering alloy steels.
During the 1960s, big steel compa-
nies were changing production meth-
ods to the new basic oxygen converter
that removed carbon from the molten
metal delivered from blast furnaces.
This reduced the scrap market to very
low levels with low prices, giving further
advantage to minimills against big steel
and its capital requirements for blast
furnaces and basic oxygen converters.
At the same time, big steel was adjust-
ing to conversion to continuous cast-
ing. All these factors opened the door
for minimills to make small bars and
shapes not required to meet the speci-
fications of higher quality steel.
THE FIRST MINIMILL
The first continuous caster was
installed in 1959 at the Premium Steel
Co. in Alberta, Canada. The work was
done under Gerald Heffernan, a metal-
lurgical engineer from the University of
Gerald Heffernan built the first minimill
in North America in Ontario, Canada, and
the secondmill in St. Paul, Minn. Courtesy
of
amm.com.
Toronto. Only a portion of production
was put through the caster with the
rest turned into ingots, which had to be
rolled or forged into billets. Premium
Steel was purchased in 1963 by Stelco,
a big steel company in Ontario, to gain
access to this growing western market.
With his share of the sale and other fi-
nancial backing, Heffernan built the
first minimill in North America in 1964,
called Lake Ontario Steel Co. (Lasco).
Lasco was the first steel plant to put all
hot metal through a continuous caster.
Heffernan adopted a new management
philosophy, developing training for
many different job requirements with a
focus on safety. His management style
would become standard for the mini-
mill industry.
The second plant built in North
America was North Star Steel Co. in St.
Paul, Minn., also engineered by Heffer-
nan. North Star was financed by Cargill
with minority stockholders including
Heffernan. It went on stream in 1968,
producing 200,000 tons per year in bars
and shapes. One potential customer
was Vulcraft in Norfolk, Neb., a com-
pany that assembled small bars and
angle shapes into roofing beams for
shopping malls and big box buildings.
Vulcraft’s president, F. Kenneth Iver-
son, visited North Star to discuss buy-
ing steel, but came away determined
to build his own minimill to supply five
assembly plants. The parent company,
Nuclear Corp. (Nucor), selected a site
in Darlington, S.C., near one of the fab-
rication plants. This minimill became
the third in North America and had ca-
pacity of 200,000 tons per year. Startup
difficulties, combined with Heffernan
F. Kenneth Iverson, CEO of Nucor, led the
minimill industry for the first 25 years.
Courtesy of
aimehq.org.