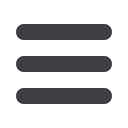
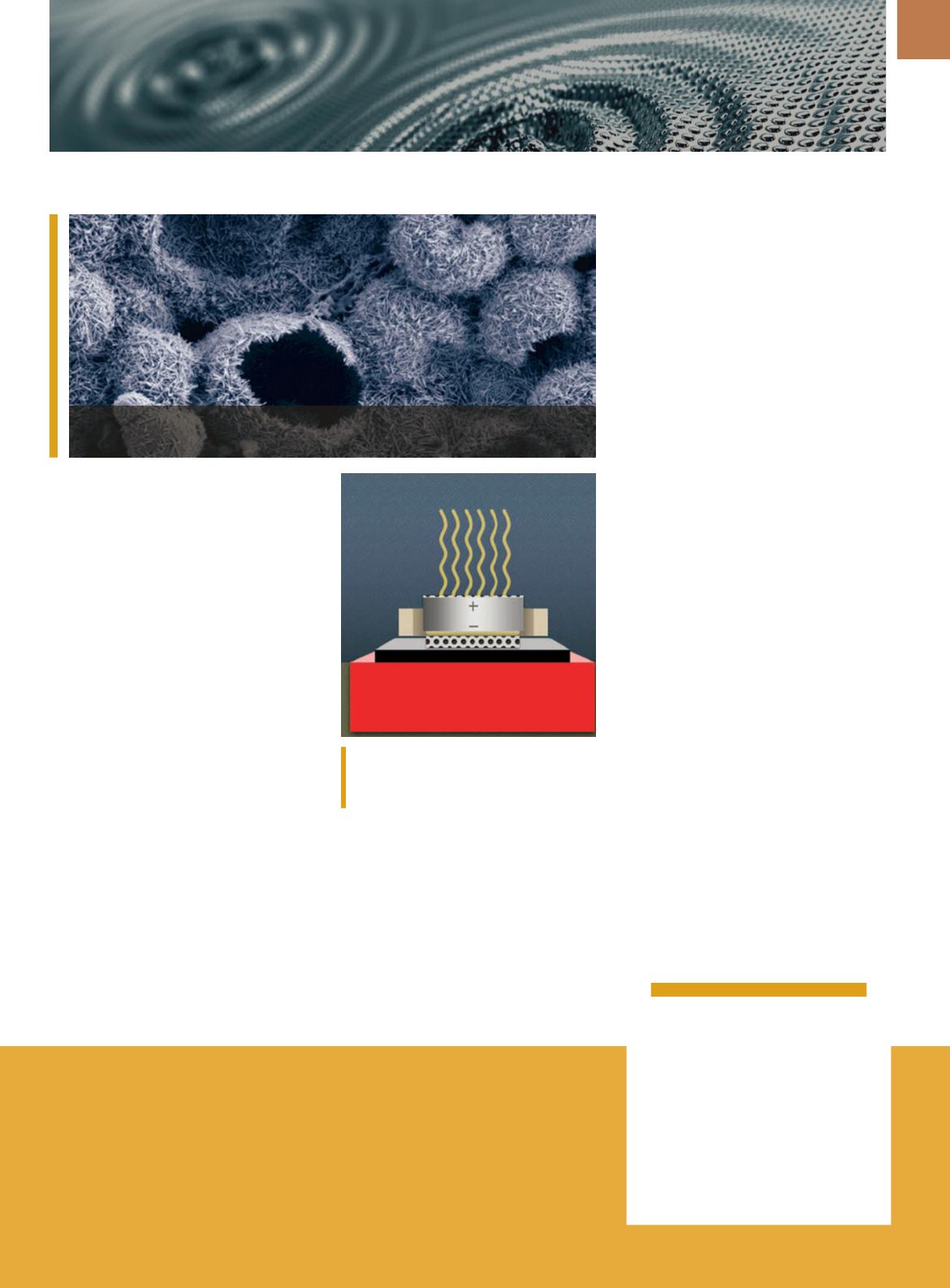
A D V A N C E D
M A T E R I A L S
&
P R O C E S S E S |
M A R C H
2 0 1 5
1 5
BRIEFS
Aleris, Cleveland, offers a new 7017 aluminum alloy in North America for commercial
plate and defense uses. After extensive review and testing, the U.S. Army Research
Lab issued MIL-DTL-32505 for use in armor applications. 7017 offers high strength,
good weldability, and corrosion resistance. It is currently used in Europe and Asia on
combat vehicles to achieve superior ballistic protection.
aleris.com.
SURFACE ENGINEERING
COATINGS HELP TURBINES
HANDLE THE HEAT
Scientists at the Fraunhofer In-
stitute for Chemical Technology ICT,
Germany, developed a coating tech-
nique to protect turbine engine and
waste incinerator components against
heat and oxidation. A topcoat from
micro-scaled hollow aluminum oxide
spheres provides heat insulation and
has already proven more economical
than conventional techniques in the
lab.
The basic coating layer forms
during interaction of aluminumparticles
and the metallic component. Aluminum
powder is depositedon the surface of the
metal and is heated to a suitable tem-
perature over several hours. The result
is an aluminum-rich coating on the com-
ponent’s surface that protects against
oxidation at high temperatures. With
the new procedure, the topcoat from
the hollow aluminum oxide spheres is
formed as well.
www.ict.fraunhofer.de/ en.html.Pico un Oy,
Finland, creat d a new to ic layer deposition ( LD) process for copper
and niobium oxide. The low-t mperatu (<150°C) processes for niobium oxide
and copper are made possible by the second generation of the Pico ot 300 source
system, which allows even lower vaporization temp ratures and efficient, uniform
distribution of the precursor vapor in the reacti n hamber even at low substrate
temperatures.
picosun.com/en/home .HARDIDE COATINGS
LTD., UK,
INCREASED ITS
INSTALLED CAPACITY BY
NEARLY 50% TO COPE WITH
GROWING DEMAND
FOR NANOSTRUCTURED
TUNGSTEN CARBIDE
COATINGS.
hardide.com.
COMPOSITE COATING MAKES
BATTERIES SAFER
Every year, nearly 4000 children go
to emergency rooms after swallowing
button batteries—the flat, round bat-
teries that power toys, calculators, and
many other devices. Ingesting these
batteries has severe consequences,
including burns that permanently
damage the esophagus, tears in the di-
gestive tract, and in some cases, even
death. To help prevent such injuries, re-
searchers at Massachusetts Institute of
Technology, Cambridge, Brigham and
Women’s Hospital, and Massachusetts
General Hospital devised a new way to
coat batteries with a special material
that prevents them from conducting
electricity after being swallowed. In an-
imal tests, they found that such batter-
ies did not damage the gastrointestinal
(GI) tract.
Researchers coated the batteries
with a material that would allow them
to conduct when under pressure, but
would act as an insulator when the bat-
teries are not being compressed. Quan-
tum tunneling composite (QTC), an off-
the-shelf material commonly used in
computer keyboards and touchscreens,
fit the bill perfectly. QTC is a rubber-
like material, usually made of silicone,
embedded with metal particles. Under
normal circumstances, these particles
are too far apart to conduct an electric
current. However, when squeezed, the
particles come closer together and start
conducting. This allows QTC to switch
from an insulator to a conductor, de-
pending on the applied pressure. Be-
cause QTC is relatively inexpensive and
already used in other consumer prod-
ucts, researchers believe battery com-
panies could easily implement this type
of coating.
web.mit.edu.
Hollow spheres of aluminum oxide are filled with gas andmanufactured
economically. Courtesy of Fraunhofer ICT.
This coated battery still conducts
electricity when compressed, but
not if accidentally ingested.