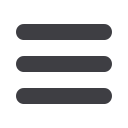
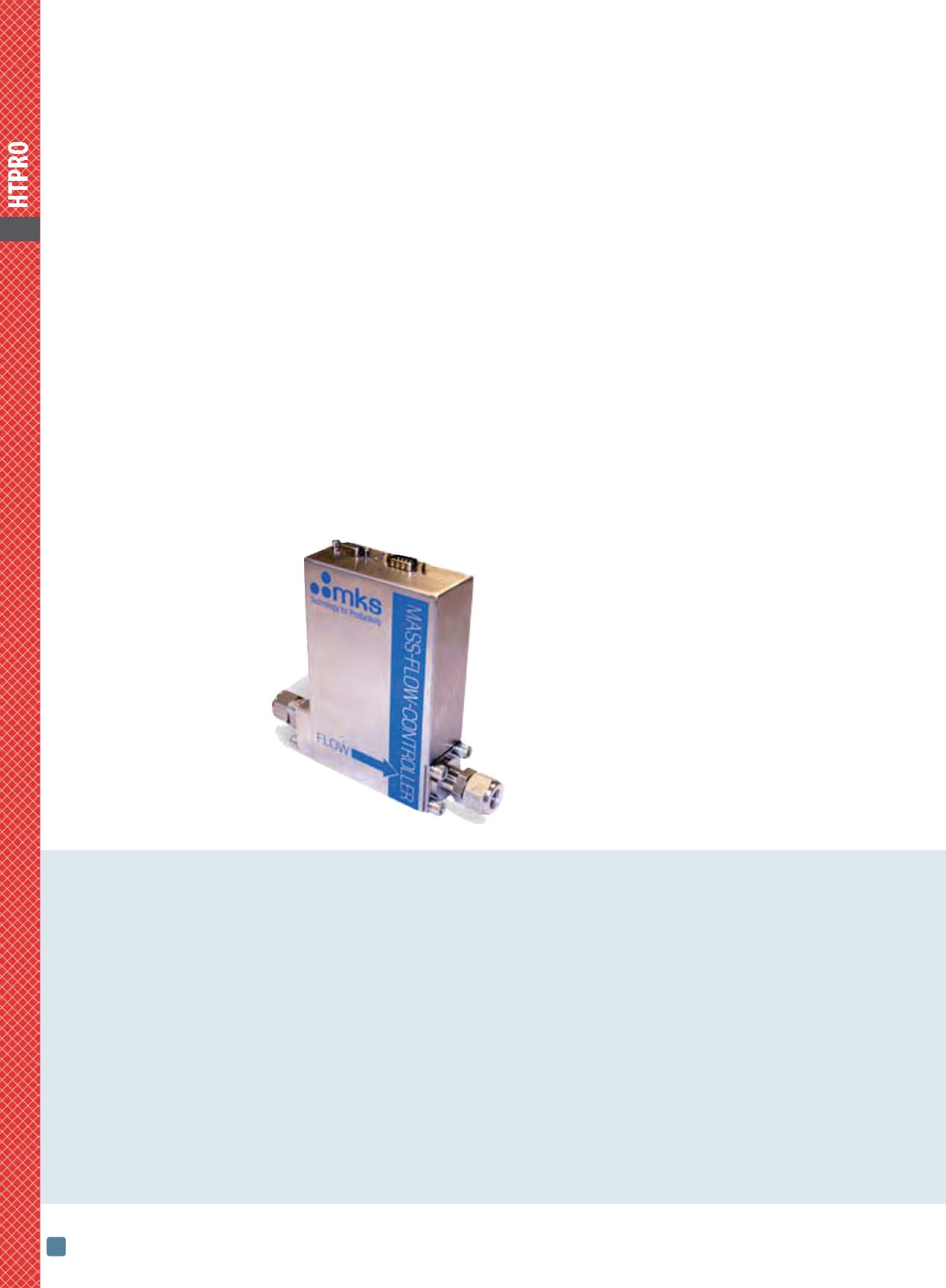
OPERATIONAL PRINCIPLES
OF FLOWMETERS
ONCE A “SET IT AND FORGET IT” TECHNOLOGY, FLOW MEASUREMENT IS AN INCREASINGLY IMPORTANT
PART OF QUALITY CONTROL SYSTEMS IN THE HEAT TREATING INDUSTRY.
Daniel H. Herring,*
The Herring Group Inc., Elmhurst, Ill.
In most heat treating applications, im-
portant flowmeter selection criteria in-
clude reliability, accuracy, ruggedness,
ease of calibration, and ease of mainte-
nance. Given the high accuracy and reli-
ability of today’s instruments, users can
run their processes more economically.
Part 1 of this article (June 2014
HTPro
)
discussed the most commonly used flow
measurement instruments and com-
pared their operating principles. This
article covers selection basics, sizing,
mass flowmeter overview, and FAQs
about flowmeters.
Flowmeter Selection Basics
There are many flowmeter features
that must be considered to select
the one that best meets the re-
quirements of the application
(Table 1). The first step in selecting
a flow sensor is to determine if the
required flow rate information
should be continuous or total-
ized, and whether these data
are needed locally or re-
motely. If remotely, should the
transmission be analog, digital, or
shared? And, if shared, what is the
required minimum data-update
frequency? Once these questions are an-
swered, the properties and flow charac-
teristics of the process fluid (gas or
liquid), and the properties and configu-
ration of the piping that will accommo-
date the flowmeter should be evaluated.
Next, determine the required flowmeter
range by identifying the minimum and
maximum flows (mass or volumetric)
that will be measured and the required
flow measurement accuracy. Typically,
accuracy is specified in percentage of ac-
tual reading, percentage of calibrated
span, and percentage of full-scale
units. Accuracy require-
ments should be
separately stated
at minimum,
normal, and
maximum flow,
otherwise meter
performance might
not be acceptable
over its full range.
Flowmeter sizing
When purchasing a new flowmeter to
measure gas flow in heat-treating appli-
cations, it is important to remember the
distinction between the operating range
and design range of the instrument.
Some variable-area flowmeters offer
full-scale operation, while others offer a
limited range such as “not below 25%
and not above 90% of scale capacity.” For
example, a flowmeter rated for 0 to 2000
cubic feet per hour (cfh) only provides
accurate readings when the flow is be-
tween 500 and 1800 cfh.
If flow measurement must cover a wide
flow range, select a flowmeter that has a
high turndown. An alternative, but costly,
approach is to install several flowmeters
of different sizes with automatic or man-
ual switching based on flow range.
A rule of thumb for sizing a flowmeter
is to purchase one “in the middle third,“
that is, size it so the actual flow will be
no less than 33% and no higher than 67%
of the scale selected. This enables com-
pensating for unexpected changes in
flow requirements that might occur dur-
ing actual operation. Over the life of a
*Member of ASM International
ADVANCED MATERIALS & PROCESSES •
SEPTEMBER 2014
HTPRO
PART 2
Is it easier to control a gas or a liquid?
Liquids are easier to measure and control because of their small
compressibility. For most volumetric flow applications, it is not
necessary to closely control the incoming pressure in liquid sys-
tems. By their nature, liquids are easily captured and measured to
a high degree of accuracy. By comparison, gases, due to their com-
pressibility, require more complex sensing and control methods.
Should I have my flowmeters recalibrated?
If a change in operating conditions is permanent, such as the de-
sire to constantly operate at a different pressure, then recalibra-
tion of the flow measurement device is strongly recommended.
As a rule, flowmeters used in heat-treating applications are
designed for a maximum temperature of 150°F (65°C) and an op-
erating pressure up to 50 psig (345 kPa). However, application-
specific flowmeters have maximum operating pressures outside
these ranges.
Is it necessary to maintain flow devices?
All flowmeters eventually require maintenance, and some
units require more maintenance than others, so this factor
should be considered when selecting a unit. However, in most
heat-treating operations, the equipment manufacturer has al-
ready made that choice for you, so understanding what main-
tenance is required and when it should be performed is of
paramount importance.
Flowmeters have moving parts and require internal inspection,
especially if the fluid is dirty or viscous. For example, in furnaces
using endothermic gas, flowmeters often become contaminated
with soot (carbon) and must be cleaned by
carefully
disassem-
bling the flowmeter and cleaning all internal moving parts, plus
replacing the dirty fluid in the flowmeter tube. CAUTION: This
involves isolating the flowmeter, or performing maintenance
when the unit is shut down, and must be done in a safe manner
Frequently Asked Questions
Representative
mass flowmeter.
Courtesy of
MKS
Instruments.
10
56