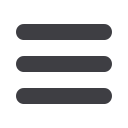
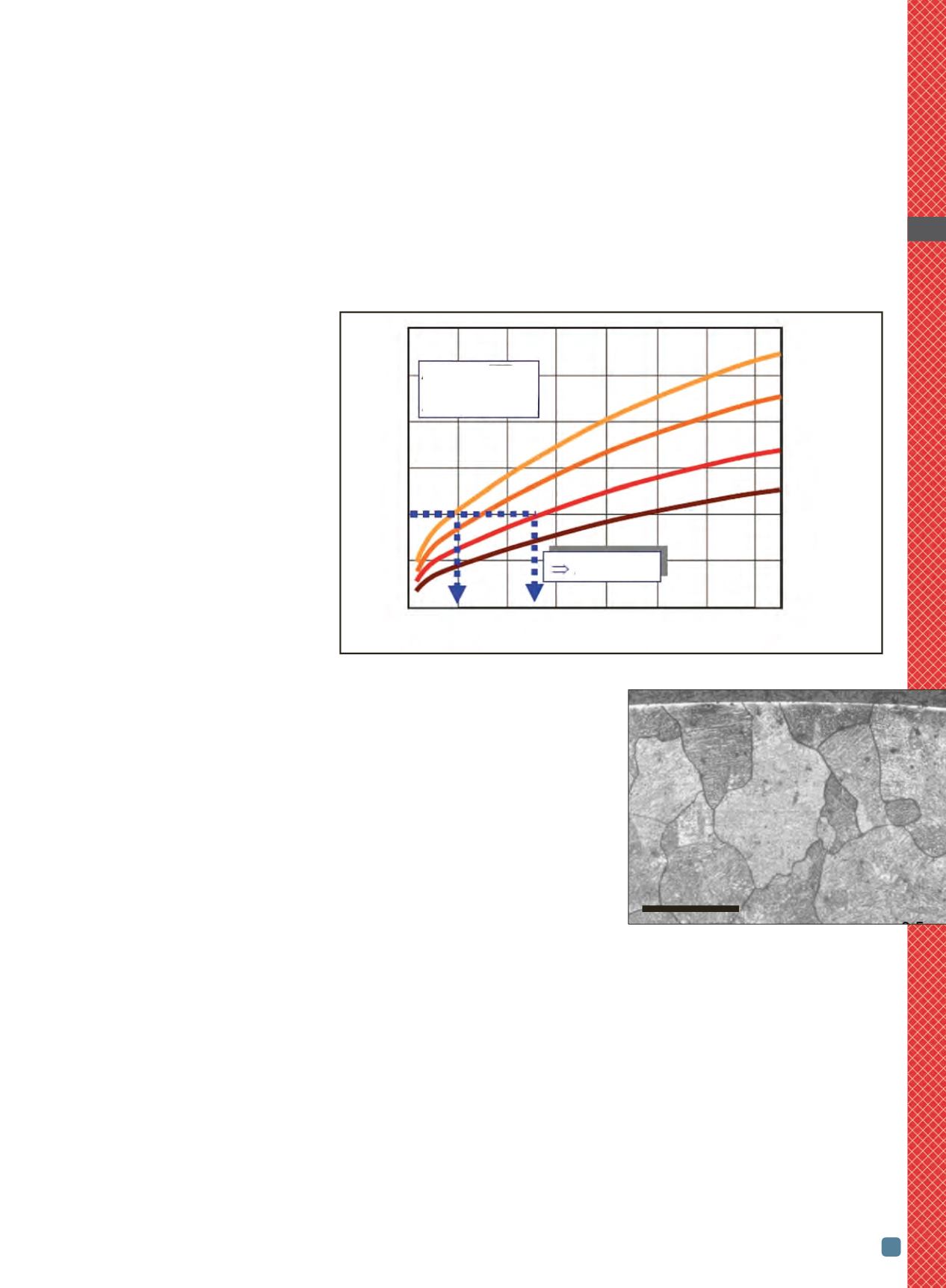
ADVANCED MATERIALS & PROCESSES •
SEPTEMBER 2014
53
HTPRO
7
DEVELOPMENTS IN MICROALLOYED,
COARSENING-RESISTANT STEELS FOR
HIGH TEMPERATURE CARBURIZING
THERE IS GROWING INTEREST IN STEELS MICROALLOYED WITH TITANIUM, NIOBIUM,
AND MOLYBDENUM FOR USE IN HIGH-TEMPERATURE CARBURIZING APPLICATIONS.
Marvin McKimpson,*
Caterpillar Technical Center, Mossville, Ill.
There is growing interest in steels, par-
ticularly carburizing steels, that have im-
proved resistance to austenite grain
coarsening during heat treating. The
driver for much of this interest is
the increased use of low-pressure (i.e.,
vacuum) carburizing furnaces in com-
mercial heat treating operations. These-
furnaces are capable of processing steels
at higher temperatures and substantially
shorter cycle times than conventional at-
mosphere furnaces. The higher-temper-
ature capability is due to both furnace
construction and a lower potential of the
furnace to cause intergranular oxidation
in the steels being processed.
Figure 1 shows that increasing carburiz-
ing temperature from 950° to 1050°C
(1740° to 1920°F) potentially can shorten
carburizing time by up to 60%
[1]
. How-
ever, when carburized above 950°C,
many current commercial steels show
excessive austenite grain size coarsening.
For example, Fig. 2 shows the grain
growth in a commercially available mod-
ified SAE 4120 steel vacuum annealed at
1100°C (2010°F) for 10 hours. The large
grain size is apparent, with grains ap-
proaching 1 mm in size. Such grain
coarsening degrades both the toughness
and fatigue resistance of carburized
components, and is generally not accept-
able for commercial products.
Grain coarsening control
Most commercial carburizing steels rely
on submicron aluminum nitride (AlN)
precipitates to control grain size coars-
ening during heat treating. The nitrides
pin austenite grain boundaries, restrict-
ing grain growth. Unfortunately, at tem-
peratures above 950°C, the particles
begin to coarsen and dissolve, allowing
austenite grain growth. Research organ-
izations worldwide are exploring ways to
improve coarsening resistance of these
steels by incorporating submicron pre-
cipitates (generally either nitrides or car-
bides) having greater thermal stability
than AlN. The additional precipitates
both increase the volume fraction of par-
ticles available to retard austenite grain
boundary migration and resist precipi-
tate coarsening (i.e., Ostwald ripening)
more effectively than AlN.
Only a few elements, primarily titanium,
boron, and niobium, form nitrides, car-
bides, and carbonitrides likely to be use-
ful for improving austenite grain
coarsening resistance. Early research fo-
cused on using titaniumnitride (TiN) due
to its high thermodynamic stability. This
work showed that titanium additions to
steel can substantially improve grain
coarsening resistance. Unfortunately, as is
well known within the industry, even
small titanium additions often lead to
large cuboidal TiN or Ti(N,C) inclusions
that degrade both the toughness and fa-
tigue resistance of the steel. Accordingly,
using titanium for grain size control in
commercial alloys is likely to require very
careful control of steelmaking practices.
Recent work has focused on using nio-
bium, or a combination of niobium and
titanium, to improve austenite grain
coarsening resistance. Consider, for ex-
ample, a carburizing steel with microal-
loy additions of both titanium and
niobium. If titanium levels are suffi-
ciently low to avoid formation of large
cuboidal TiN particles in the melt (typi-
cally 0.02 wt% or lower), only small TiN
precipitate particles form in the steel as
it cools through the austenite tempera-
Fig. 1 —
Effect of carburizing temperature on carburizing time.
0.5 mm
Fig. 2 —
Grain growth in modified SAE
4120 steel vacuum annealed at 1100°C
(2010°F) for 10 hours. Source: Ref 2.
1050°C (1920°F)
1000°C (1830°F)
950°C (1740°F)
900°C (1650°F)
2 4 6 8 10 12 14
Carburizing time, h
3.0
2.5
2.0
1.5
1.0
0.5
0
Carburizing depth for 0.35%, CD
610
, mm
D
t ~ 60%
EHT
610
~
Ö
Dt
D = D
0
exp
(-Q/RT)
*Member of ASM Heat Treating Society