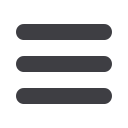
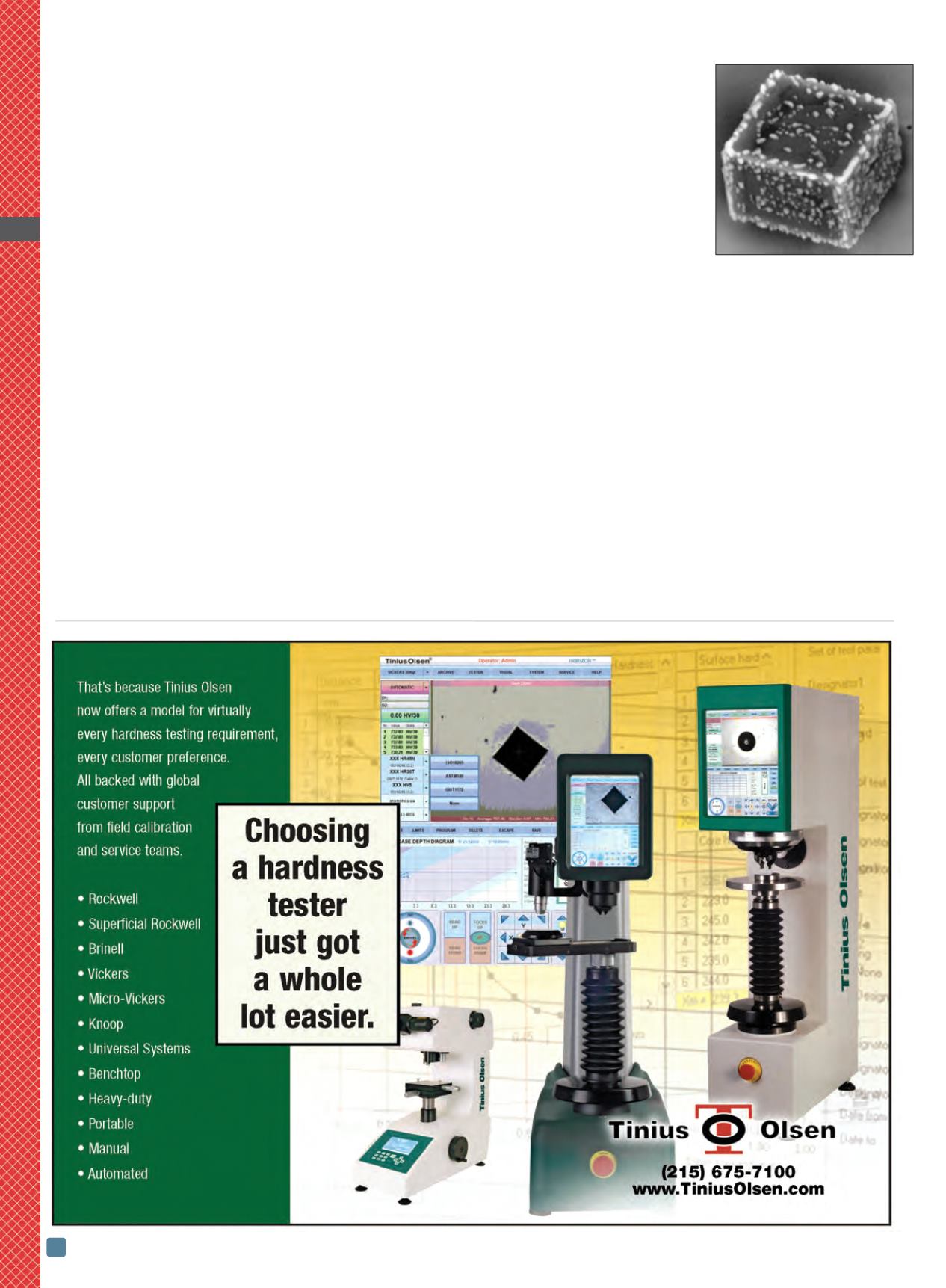
ADVANCED MATERIALS & PROCESSES •
SEPTEMBER 2014
54
HTPRO
8
ture region. Then, as the steel is hot worked, niobium carbide
(NbC) and/or carbonitride precipitates also form, sometimes on
preexisting TiN nuclei. For example, Fig. 3 shows a TiN cuboid
approximately 30–40 nm in size (gray phase) containing numer-
ous coprecipitated Nb(C,N) particles (white phase).
Molybdenum additions
Additional research indicates that supplementing titanium and
niobium microalloy additions with molybdenum can be particu-
larly attractive for improving austenite grain coarsening resistance.
For example, a recent U.S. Department of Energy study shows that
a modified SAE 4120 steel containing nominally (wt%) 1.1 Cr,
0.4 Mo, 0.02 Ti, 0.06 Nb, and 260 ppm nitrogen has substantially
better coarsening resistance during simulated carburizing cycles
than a similar modified SAE 4120 steel without Ti and Nb addi-
tions
[2]
. Figure 4 shows the prior austenite grain size of this
quenched and tempered microalloyed steel after various thermal
cycles. After holding at 1050°C for 8 hours, the material still ex-
hibits an ASTM grain size number of 6 or finer. For comparison,
the control material with no Ti or Nb additions shows a duplex
prior austenite grain size ranging from ASTM grain size number
5 down to 2 after holding at 900°C (1650°F) for 8 hours.
Researchers at the Colorado School of Mines, Golden, are work-
ing to better understand the role that molybdenum plays in im-
proving austenite grain coarsening resistance. In a recent study,
Enloe looked at several microalloy-modified SAE 4120 steels
containing nominally (wt%) 0.01 Ti, two different levels of Nb
(0.04 and 0.1), and two different levels of Mo (0.01 and 0.3)
[4]
.
These steels were given various
thermal processing sequences and
examined using a combination of
optical and electron microscopy,
precipitate extraction, and atom
probe tomography. Results show
that molybdenum additions cause
a significant decrease in the rate of
carbide and nitride precipitate
coarsening. In addition, molybde-
num tends to partition from the
precipitates to the austenite during
extended holding times at elevated
temperature. However, molybde-
numenrichment at the precipitate-
matrix interface is not observed. Accordingly, the observed
decrease in carbonitride particle coarsening is probably not due to
Mo segregation at this interface.
Commercialization
Despite extensive ongoing research, commercialization of mi-
croalloyed coarsening-resistant steels appears to be proceeding
slowly due to several factors. Because these alloys are likely to be
of greatest value to companies interested in low-pressure carbur-
izing, market pull for these materials is somewhat smaller than
that for other steels. In addition, because development of microal-
loyed, coarsening-resistant steels is a dynamic international re-
search topic, a careful review of global patent literature may be
needed before determining how new intellectual property can be
Fig. 3 —
A 30–40 nm cuboidal
titanium-nitride (TiN) particle
(gray) containing fine niobium
carbonitrides Nb(C,N) (white).
Source: Ref 3.