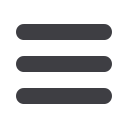
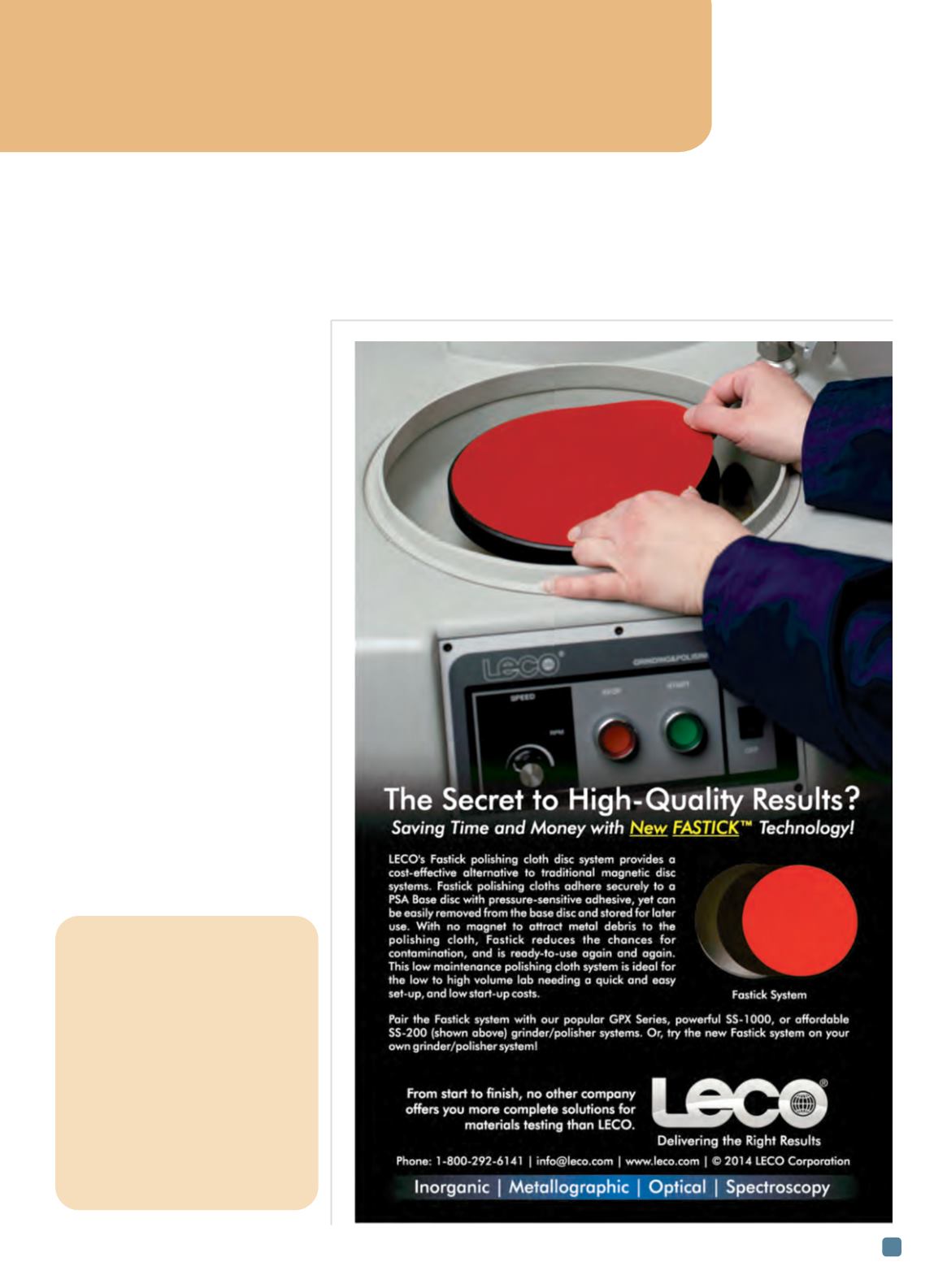
peratures and pressures, opening up their use in new markets such as aerospace, oil and gas, and nu-
clear power. Prof. Andrew Bell spearheaded the research and notes the new materials are compatible
with existing manufacturing methods for piezoelectric ceramics and therefore can be mass-produced
at similar cost to current materials. The fundamental science is the same: Physical changes to the piezo-
electric material’s crystal lattice create an electrical change or, conversely, create physical changes when
an electrical current is applied. However, the new ceramics include novel ingredients such as bismuth
and iron and have a greatly increased tol-
erance.
For more information: Andrew Bell,
44 (0)113 3432370,
a.j.bell@leeds.ac.uk,
www.leeds.ac.uk.
Aluminum smelter and
rollingmill to close in Australia
Alcoa Inc., Pittsburgh, is permanently
closing its Point Henry aluminum smelter
and two rolling mills in Australia. The
smelter will close in August and the
rolling mills by the end of 2014. A com-
prehensive review found that the 50-year-
old smelter has no prospect of becoming
financially viable. The two rolling mills
serve the domestic and Asian can sheet
markets, which have been impacted by
excess capacity. The closures will reduce
the company’s global smelting capacity by
190,000 metric tons (mT) and reduce
their can sheet capacity by 200,000 mT.
Including the closure of the Point Henry
smelter, Alcoa announced closures or cur-
tailments representing 551,000 mT of
smelting capacity, exceeding the 460,000
mT placed under review in May 2013.
Once the Point Henry closure is complete,
the company’s total smelting operating
capacity will be approximately 3,760,000
mT, with approximately 655,000 mT, or
17%, of high cost capacity offline.
www.alcoa.com.
ADVANCED MATERIALS & PROCESSES •
APRIL 2014
9
Allegheny Technologies Inc.,
Pittsburgh, ac-
quired
Dynamic Flowform Corp.,
Billerica,
Mass. Dynamic Flowform uses a precision
flowforming process to produce thin-walled
components in net or near-net shapes across
multiple alloy systems, including nickel-base
alloys and superalloys, titanium and titanium
alloys, zirconium alloys, and specialty and
stainless alloys. “We have identified signifi-
cant growth opportunities for Dynamic Flow-
form’s products, especially in the aerospace
and oil and gas markets. These opportunities
are expected to benefit from ATI’s existing
global marketing and sales capabilities, and
ATI’s supply chain experience and relation-
ships with OEMs,” says ATI chairman, Rich
Harshman.
www.atimetals.com.