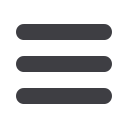
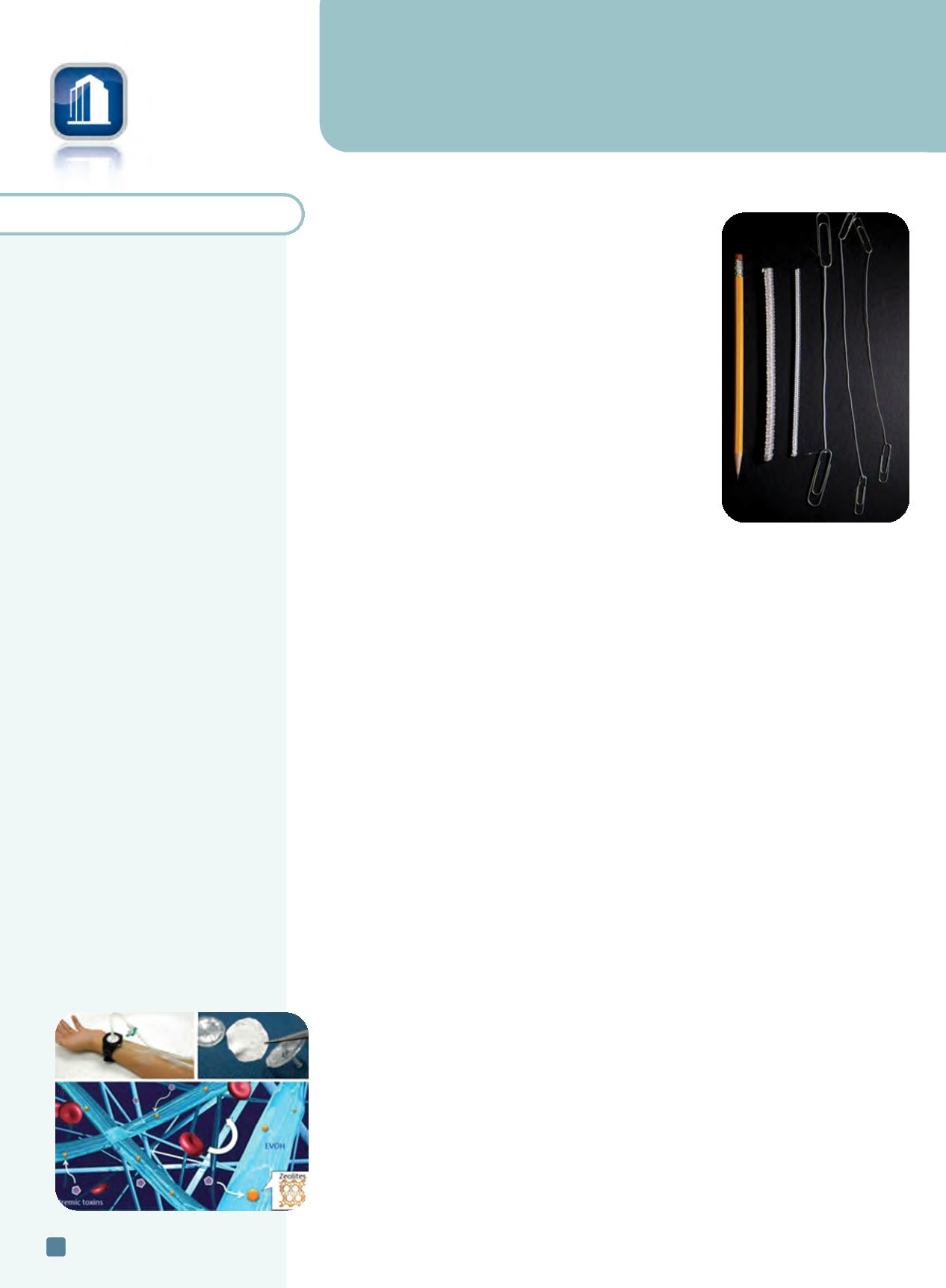
news
industry
briefs
The
National Science Foundation
(NSF)
announced a new
Center
for Dielectrics and
Piezoelectrics
to be collocated at
Penn State
and
North Carolina
State University.
NSF will provide
$830,000 over five years to
support operations and
infrastructure, and additional
funding will come from member
companies and organizations.
Areas of research include high
energy-density electrochemical
capacitors for power electronics
and the energy grid; dielectrics
with low-temperature processing
for flexible electronics; capacitors
for extreme environments; polymer
nanocomposite dielectrics to
enhance energy storage density
and improve insulation for power
distribution; and piezotronic
transistors.
www.mse.ncsu.edu/cdp.The
DOE’s Oak Ridge National
Laboratory,
Tenn., is partnering
with machine tool manufacturer
Cincinnati Inc.,
Harrison, Ohio, to
develop a large-scale polymer 3D
printing system. The partnership
aims to accelerate
commercialization of a new
additive manufacturing machine
that can print large polymer parts
faster and more economically than
current technologies. By building a
system 200-500 times faster, and
capable of printing polymer
components 10 times larger than
today’s additive machines, the
project could introduce significant
new capabilities to the U.S. tooling
sector, according to ORNL
scientists.
www.ornl.gov, www.e-ci.com.
Scientists make muscles with fishing line
An international research team led by The University of
Texas at Dallas, and including University of British Columbia
electrical and computer engineering professor John Madden
and Ph.D. candidate SeyedMohammadMirvakili, created in-
expensive artificial muscles that generate far more force and
power than human or animal muscles of the same size.
“In terms of the strength and power of the artificial mus-
cle, we found that it can quickly lift weights 100 times heav-
ier than a same-sized human muscle can, in a single
contraction,” says Madden.
Artificial muscles constructed out of materials such as
metal wires and carbon nanotubes are expensive to fabri-
cate and difficult to control. Madden and his colleagues
used high-strength polymer fibers made of polyethylene and
nylon instead, which are twisted into tight coils to create ar-
tificial muscles able to contract and relax. The muscles are
thermally powered by temperature changes, which can be
produced electrically by the absorption of light or by the
chemical reaction of fuels. Twisting the polymer fiber con-
verts it to a torsional muscle that can spin a heavy rotor
more than 10,000 rpm. Subsequent additional twisting, so
that the polymer fiber coils like a heavily twisted rubber
band, produces a muscle that dramatically contracts along its length when heated, and re-
turns to its initial length when cooled. If coiling is in a different twist direction than the ini-
tial polymer fiber twist, the muscles instead expand when heated.
Compared to natural muscles, which contract by only about 20%, these synthetic ver-
sions can contract by about 50% of their length. Muscle strokes also are reversible for mil-
lions of cycles as muscles contract and expand under heavy mechanical loads. Twisting
together a bundle of polyethylene fishing lines produces a coiled polymer muscle that can
lift 16 lb. Operating in parallel, similar to how natural muscles are configured, 100 of these
polymer muscles could lift roughly 0.8 tons.
The new muscles were used to manipulate surgical forceps and could find use in robots
and low-cost devices to help people with impaired mobility, according to the researchers.
For more information: John Madden, 604/827-5306,
jmadden@ece.ubc.ca,
www.ece.ubc.ca.
Nanofiber mesh enables wearable kidney dialysis
Mitsuhiro Ebara and colleagues at the International Center for Materials Nanoarchi-
tectonics, National Institute for Materials Science in Ibaraki, Japan, developed a way of re-
moving toxins and waste from blood using an inexpensive and easy-to-produce nanofiber
mesh. The material could be incorporated into a blood purification product small enough
to be worn on a patient’s arm, reducing the need for expensive, time-consuming dialysis.
The mesh is made using two components—a blood-compatible primary matrix polymer
made from polyethylene-co-vinyl alchohol (EVOH) and sev-
eral different forms of zeolites, naturally occurring alumi-
nosilicates. Zeolites have microporous structures capable of
adsorbing toxins such as creatinine from blood. The mesh
was made via an electrospinning process, using an electrical
charge to draw fibers from a liquid. The team found that the
silicon-aluminum ratio within the zeolites is critical to cre-
atinine adsorption. Beta type 940-HOA zeolite had the highest capacity for toxin adsorp-
tion, and shows potential for a final blood purification product. Researchers are confident
that a product based on their nanofiber mesh will soon be a compact and affordable alter-
native to dialysis for kidney failure patients around the world.
www.nims.go.jp.
ADVANCED MATERIALS & PROCESSES •
APRIL 2014
12
E
MERGING
T
ECHNOLOGY
University of Texas at Dallas
researchers and international
collaborators made artificial
muscles in a variety of sizes
from polymer fishing line.
Courtesy of UT Dallas.
A newly-fabricated nanofiber
mesh for removing toxins from
blood, made by WPI-MANA
researchers, may be
incorporated into wearable
blood purification systems
for kidney failure patients.