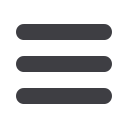
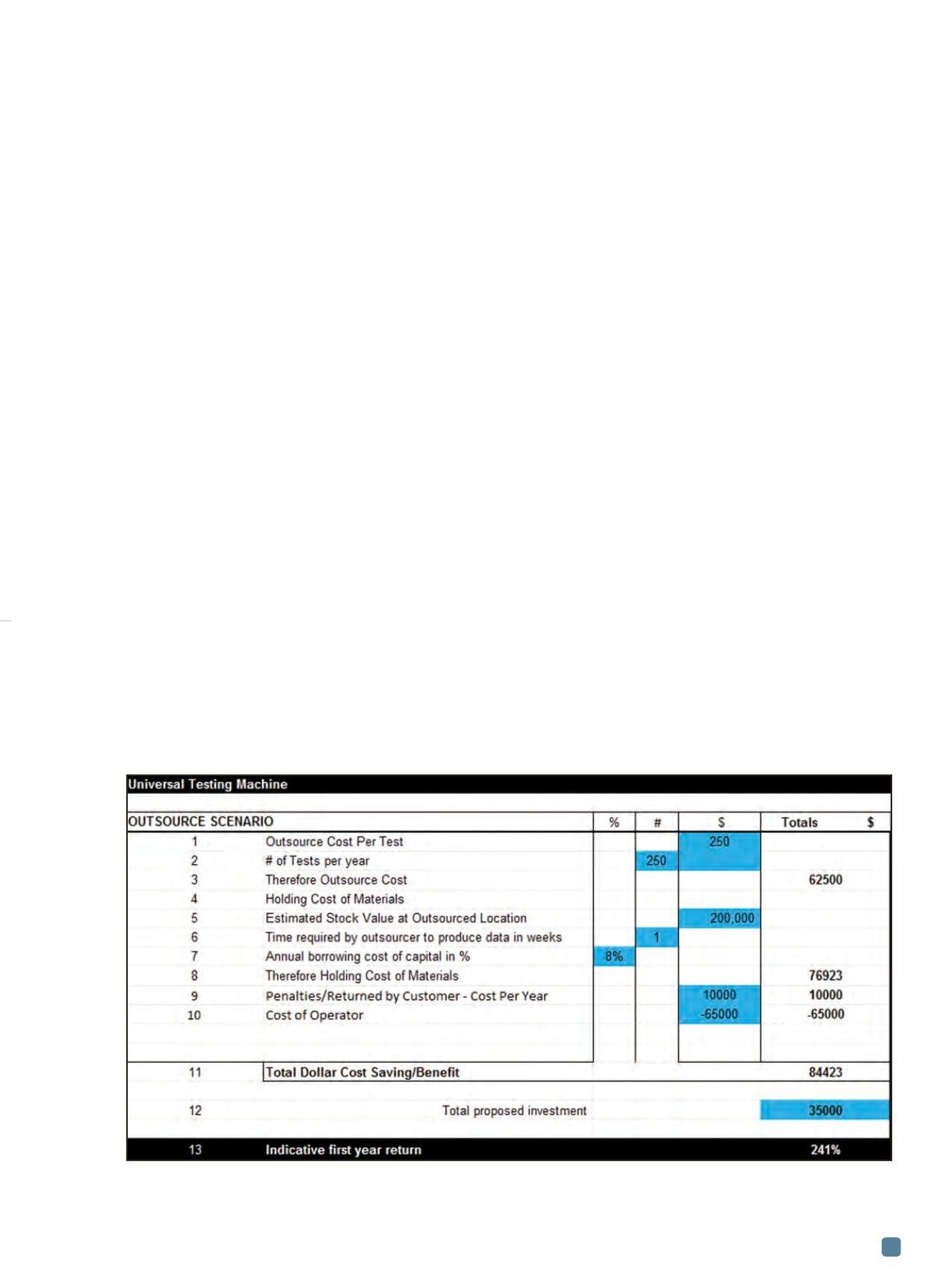
In-House vs. Outsourced Materials Testing:
How to Decide
M
any companies are revisiting their decision to
bring materials testing in-house. Some own
aging testing equipment and must decide
whether or not to invest in upgrades, while others currently
outsource testing, and debate if an estimated 200% return-
on-investment (ROI) for universal testing equipment is
enough to bring testing activities back on site. When mak-
ing this choice, quality and time are as important as ROI in
the final analysis. By reviewing the impact on quality con-
trol and timeliness, issues can be better understood and a
blueprint for gaining bottom-line cost efficiencies can be
developed.
Quality results
Materials testing represents a key quality threshold in
the manufacturing process—specific, clear, and relevant
data from which material qualities and overall product
quality can be accurately assessed is needed. What is being
tested, how quality is defined for specific products, and
overall business strategies must be considered when decid-
ing whether to insource or outsource testing functions.
When reviewing day-to-day operations, including
manufacturing processes, the business and operational im-
pact of testing must be determined. Testing data that lacks
credibility, is difficult to use, or negatively impacts inven-
tory can destroy performance. Is testing a major part of
new product development or continuous improvement of
existing products? Is it connected to brand management?
For example, companies that tout their products as being
the most flexible or strongest in the market rely on testing
and documentation to back up those claims. When these
results are central to branding claims, being confident in
the testing process is critical.
Another consideration is the role of testing in work-
flow iteration adjustments. The more significant these on-
going testing results are to workflow, the greater the need
for real-time or near real-time adjustments to testing
schedules. External testing firms may or may not be able to
accommodate testing timetables that can keep pace as
quickly as an internal process. How does testing align with
overall business strategies? For some companies, expand-
ing or updating testing capabilities can help set the stage
for business growth.
Other quality factors include regulatory requirements
such as ASTM or ISO standards. If meeting these bench-
marks is vital to new business, companies must be confi-
dent in their tester’s ability to deliver accurate results.
Testing complexity also plays a role in decision-mak-
ing—some materials require highly complex tests; other ma-
terials are straightforward. Amix of testing needs can result
in a variety of testing sources, including both outsourced
and in-house options, rather than making an either-or deci-
sion. Once the impact of testing quality is determined, test-
ing quality measurements can then be determined. This is
particularly important when considering a move from in-
house to outsourced testing, or vice versa. Measuring ROI is
challenging when quality specifications vary.
Quantity must also be considered: How many tests and
ADVANCED MATERIALS & PROCESSES •
APRIL 2014
27
TECHNICAL SPOTLIGHT
Fig. 1 —
ROI calculation for in-house vs. outsourced testing. Tests conducted by the new equipment in this scenario include
tension, compression, peel, and bend. When considering all factors—quality, time, and cost—it is clear that in-house testing is the
better option for many companies.