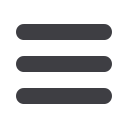
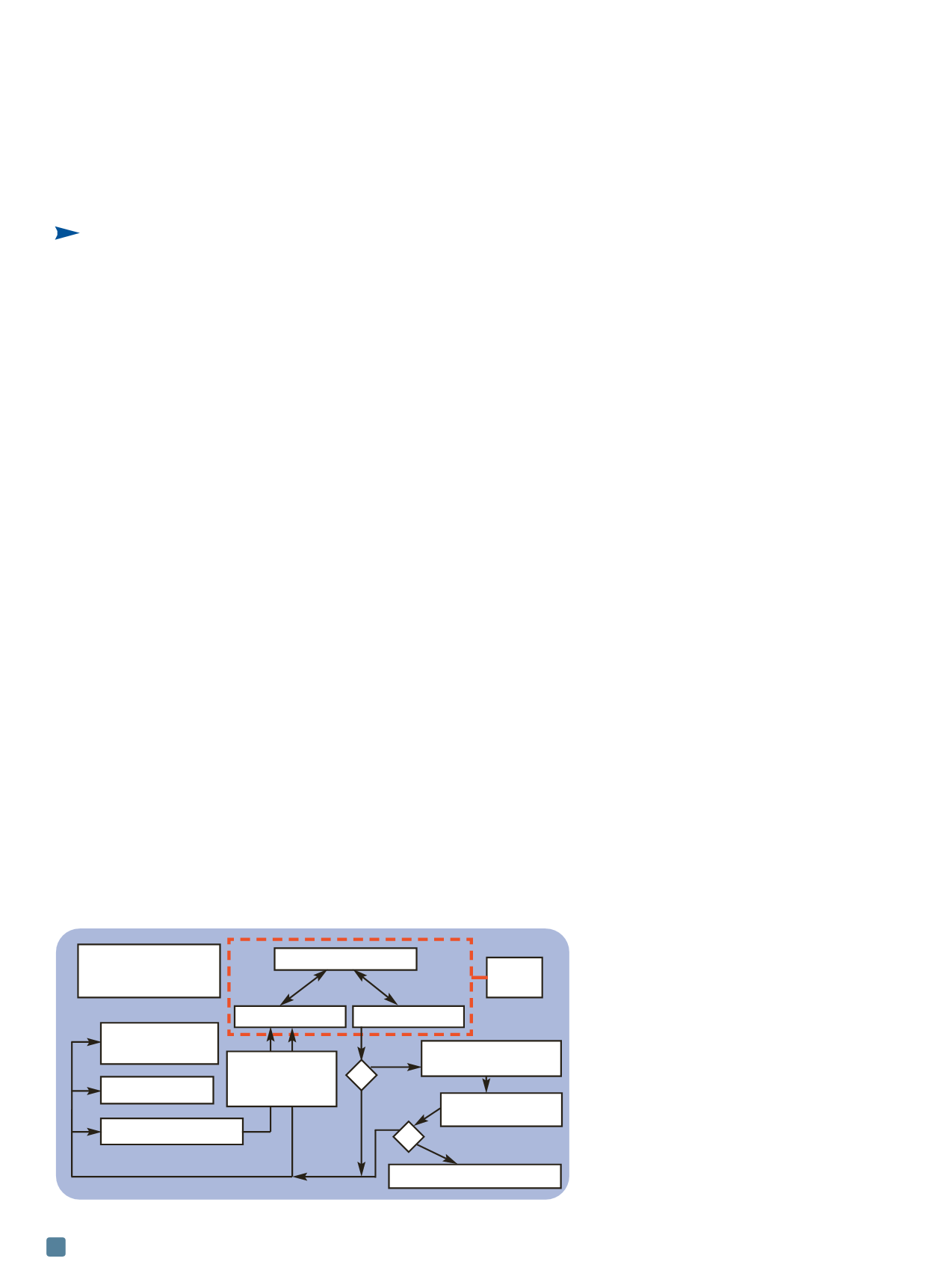
I
ntegrated Computational Materials Engi-
neering (ICME) is a relatively new discipline
that shows great promise for reducing the
cost and time required to design and deploy
new materials, manufacturing technologies,
and products. It has been successfully used in
some product development programs to date.
Although considerable effort has been put
into model development over the past three
decades, and while many of these computational
models are now in use, significant challenges to
comprehensive development and implementa-
tion of these models in ICME remain. This
article introduces an ICME implementation
framework for product development using a
welding process and discusses requirements for
a welding process modeling tool for ICME. De-
velopment of the friction stir welding (FSW)
process modeling tool is discussed in detail.
Implementation framework
A proposal for implementing ICME to de-
velop products using manufacturing processes
such as welding is shown in Fig. 1. The frame-
work includes three major blocks: Product re-
quirements, manufacturing process modeling
tools, and the final product. Product require-
ments include property requirements, design,
and materials. Manufacturing process model-
ing tools include process parameters, a thermal
model, microstructure model, and property
model, as well as performance prediction tools.
The final product must be validated and veri-
fied with regard to materials and design.
The process tool is the engine of ICME, as
shown in Fig. 1. The thermal model is optional
because some manufacturing processes such as
cold forming do not experience a temperature
change. For thermally-related processes such as
welding and heat treatment, the thermal model
predicts temperature by conducting heat trans-
fer analysis.
To develop a welding process modeling
tool, model development, validation, and appli-
cation are necessary. This article explores how
ICME is used to develop a friction stir welding
(FSW) modeling tool, which can also be used
in a FSW process to develop products.
Numerical models for FSW
FSWwas originally intended for aluminum
alloys but now includes a variety of materials
such as magnesium, copper, titanium, and steel.
The process is extremely successful with alu-
minum alloys but has not progressed as
smoothly with steels due to their complicated
physical properties, such as thermal, mechani-
cal, and microstructural effects. It is essential
to develop a process model to improve under-
standing of these physical phenomena and op-
timize process parameters during FSWof steels
in order to use ICME.
A thermal model for FSW was developed
based on the finite element method. In the
model, surface heat flux is applied on the shoul-
der surface and body flux is applied in the pin
volume. A microstructure model developed by
M.F. Ashby and colleagues was implemented in
the FSW process model to predict the distribu-
tion of individual phases such as ferrite, bainite,
and martensite, and the hardness map around
the weld area.
Model validations
Analyses simulated the welding experiment
performed by D.M. Failla and J. Lippold
[1, 2]
to
validate the FSW model. The specimen was
made of HSLA-65, and was 12 mm thick, 150
mm wide, and 300 mm long. Thermal bound-
ary conditions including air convection and
strong cooling on the clamping and support
surface are specified in the thermal analysis.
Mechanical constraint from welding fixtures
was simulated in the thermo-mechanical analy-
ses. Contact between the FSW tool and weld-
ment was modeled by a contact pair.
Thermal analysis
The thermal model conducted transient
thermal analysis by inputting welding parame-
ICME Helps Develop
Friction Stir Welding Process for Steels
Developing a
process model
to improve
understanding
of thermal,
mechanical,
and
microstructural
effects—plus
optimizing
process
parameters—
during the
friction stir
welding of
steels is
essential in
order to
implement
Integrated
Computational
Materials
Engineering.
ADVANCED MATERIALS & PROCESSES •
APRIL 2014
30
Yu-Ping Yang*
EWI
Columbus, Ohio
*Member of ASM
International
Fig. 1 —
ICME implementation framework.
Manufacturing
process development
with ICME
1. Product property
requirement
2. Initial geometry
3. Material composition
Process
tool
6. Microstructure model
5. Thermal model
5. Property model
9. Tools to predict
process performance
10. Develop and test
prototypes
12. Final design configuration
8.
11.
4. Manufacturing
process
parameters
Yes
No
No
Yes