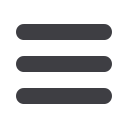
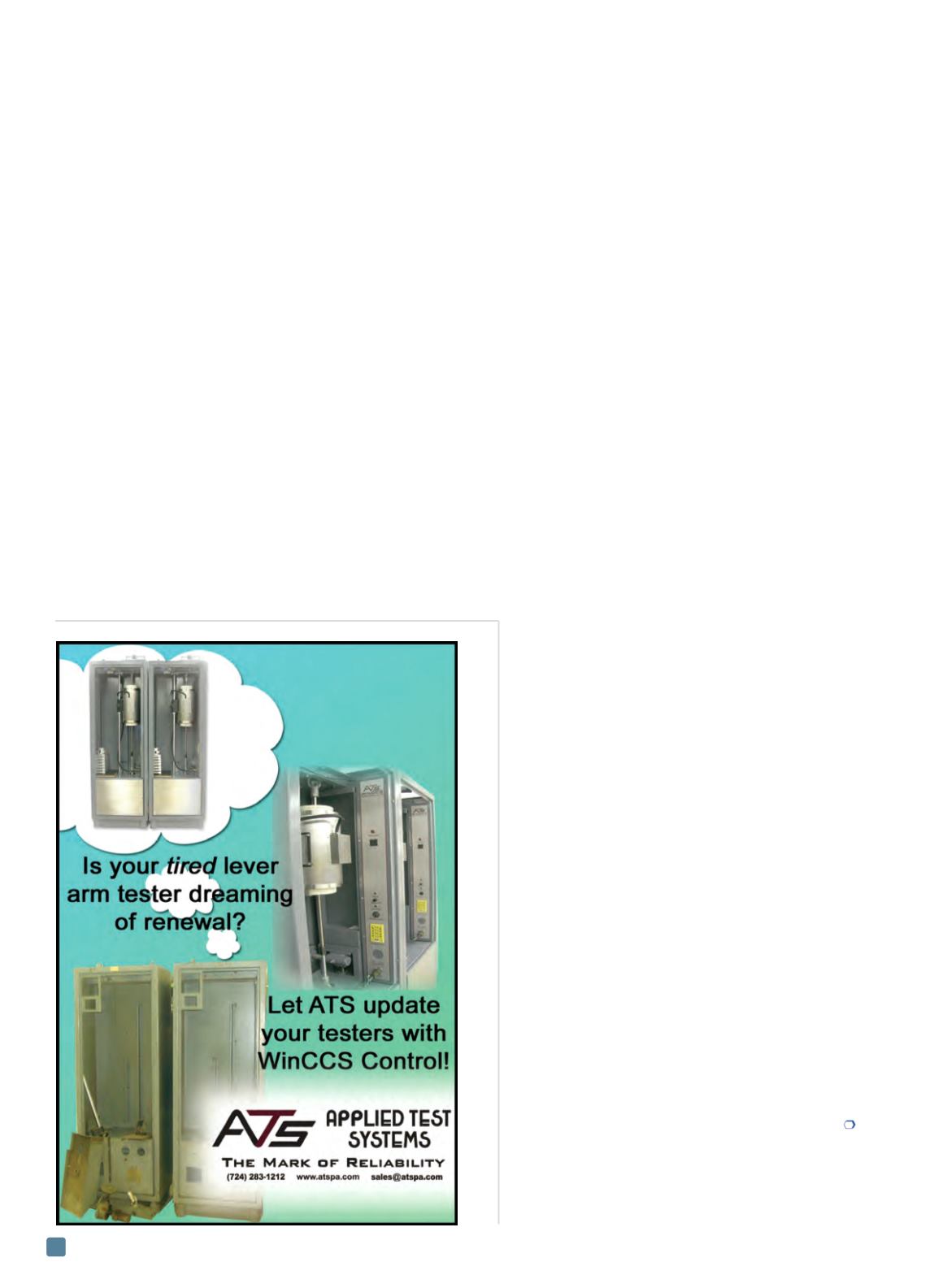
ADVANCED MATERIALS & PROCESSES •
APRIL 2014
28
how many different types of tests must be performed? For
example, a large number of the same test typically requires
one tester, whereas a large number of different tests may
require multiple testers or a universal tester. Capabilities
can be extended by retrofitting in-house testers with addi-
tional controllers and/or fixtures.
The importance of quality and broader business strate-
gies must also be considered. For example, when control
over the materials testing process is critical to a business
process, it is easier to justify the costs of rehabbing existing
machines or purchasing new equipment for in-house test-
ing. For situations that require a large number of routine me-
chanical tests, such as friction or force, and a few highly
complex tests, such as those withmultiple parameters, a mix
of insourcing and outsourcing may be best. A business
known for timely product upgrades would more likely turn
to in-house testing to better accommodate frequent adjust-
ments. The key is to arrive at the insourcing vs. outsourcing
decision after giving appropriate weight to the broader is-
sues that impact product quality and business performance.
Time factors
Time is also an important factor as it involves not only
understanding the limits before product and service quality
decline, but also the turnaround providing the greatest effi-
ciencies in quality and cost. Turnaround speed for receiving
test results is the most important criteria. For example, it is
essential to know how quickly test results are needed for
product development and/or new iterations, if delays in test-
ing create production bottlenecks, or if testing speed im-
pacts the ability to fill orders in a timely manner.
Sometimes too much stock is tied up in external test-
ing facilities, which can easily outweigh the expense of in-
vesting in an in-house tester. It is critical to know if all
products must be tested prior to shipment, or just a repre-
sentative sample. Missed deadlines or penalties due to test-
ing problems should also be considered.
Issues on this “checklist” often clarify the value of in-
house testing or, if these are not concerns, show that out-
sourced testing is the better option. Because of their
immediacy and high visibility, time factors can actually
outweigh cost considerations when it comes to testing.
When combined with quality issues, time considerations
should steer the materials testing debate.
Cost considerations
Cost scenarios are another important factor in revisit-
ing the decision-making around in-house vs. outsourced
testing. The “cost checklist” starts with a deceptively sim-
ple question: How important is it to save money in meet-
ing testing needs?
To answer this question accurately, criteria must be
viewed through the lens of quality and time considerations,
as well as the advances in functionality, relative to cost, of
new testing equipment in the past 10 years. ROI is an effec-
tive cost-measurement method. Capital investment in a
new universal tester vs. dollars spent on external testing
must be measured using the following factors:
• Cost per test
• Number of tests performed each year
• Tied up stock value (at outsourcer)
• Borrowing cost (if necessary) to invest in testing
equipment
• Outsourcer’s turnaround time on tests
• Penalties incurred (if any) due to missed deadlines
• Cost of operator to run testing equipment
• Potential investment in a new system
By bringing these components together (illustrated in
Fig. 1), it is possible to determine a complete ROI picture
of insourcing vs. outsourcing.
Conclusions
Manufacturers must test materials. The challenge lies in
identifying not only the cost, but also the quality and time
factors that will determine if testing should be conducted
in-house, outsourced, or both. Thorough analysis that in-
cludes all business concerns enables a better understanding
of how and where bottom-line testing efficiencies exist. This
process provides a blueprint for optimal testing quality that
meets and even anticipates broader strategic goals.
For more information:
Richard Gedney is CEO for ADMET,
51 Morgan Dr., Norwood, MA 02062, 781/769-0850,
mail- sales@admet.com,
www.admet.com.