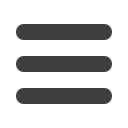
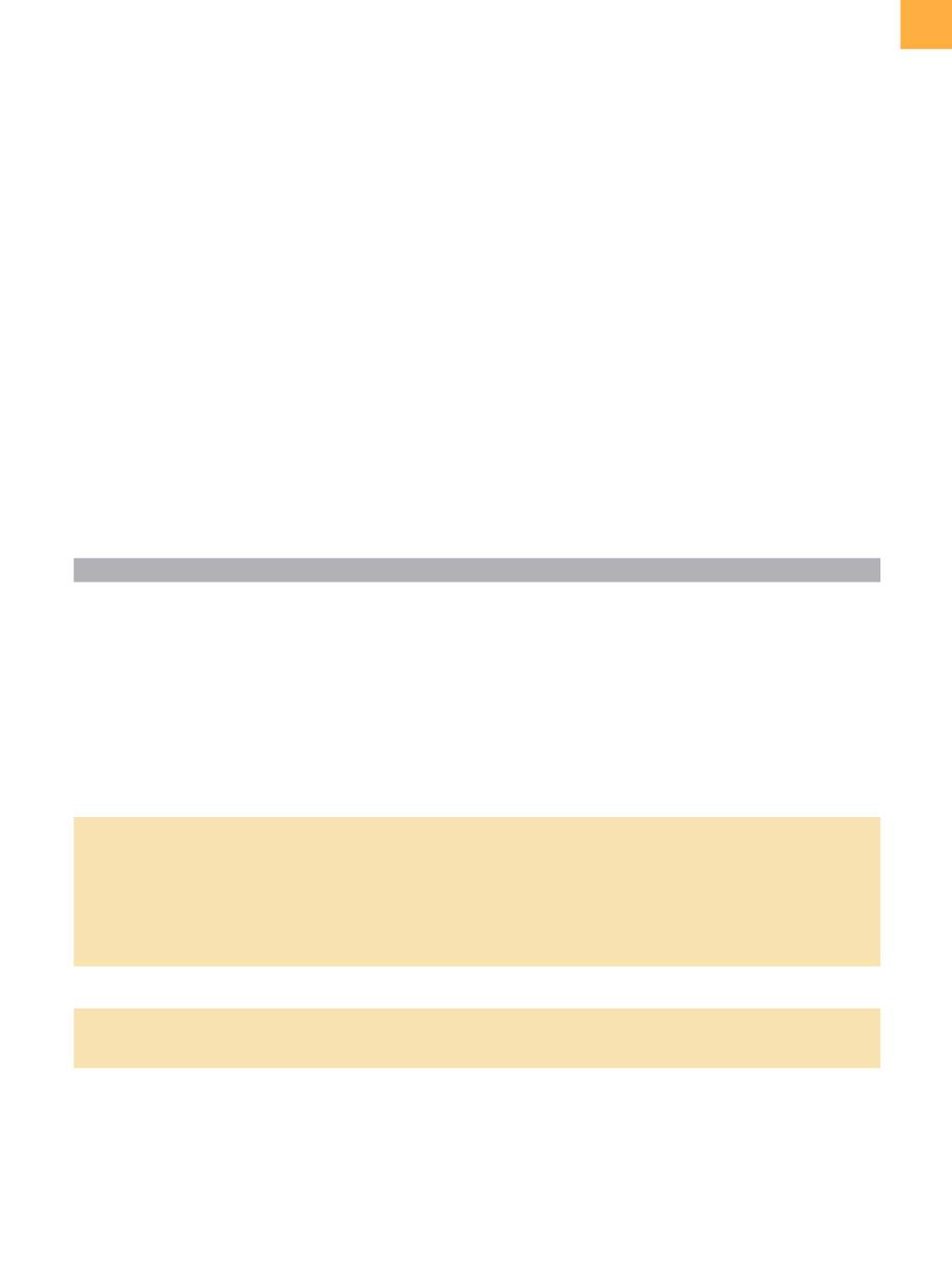
edfas.org
55
ELECTRONIC DEVICE FAILURE ANALYSIS | VOLUME 19 NO. 1
components. This working group has reviewed the
cradle-to-grave process and requirements of each and
has identified 66 potential differences. According to the
ZVEI group, “More and more semiconductors that were
not specifically developed for the automotivemarket and
their use profiles are being used in vehicles. Given the fact
that the automotive value chain increasingly introduces
ADAS and safety functions into vehicles, any failing device
in any relevant electronic control unit (ECU) within the car
can impact the application and endanger human health
or even life. The consequential safety risk impacts not
only the involved companies but may also lead to direct,
personal consequences for the responsible employee or
manager.”
At the FutureCar Workshop, organized by the Georgia
Institute of Technology and Semiconductor Equipment
andMaterials International, participants discussedmany
of the issues associatedwith the development of packag-
ing for automotive electronics, especially considering
the increasing number of safety features, which include
the increased use of sensors as well as combinations of
sensorswith controllers. These sensors operate inenviron-
ments that are harsher than mobile devices.
In many cases, zero-defect quality and 15-plus-year
reliability at the ECU level cannot be accomplished
with standard components alone. Shortcomings can be
mitigated by collaboration among automotive original
equipment manufacturers, Tier 1 suppliers, and compo-
nent makers regarding modifying vehicle and/or device
mission profile and adding system-level solutions, such
as redundancy, external component protection, and/or
cooling. Participants at the workshop agreed that future
cooperation and collaboration is necessary to ensure reli-
ability for automotive electronics.
Table 2 AEC-Q100 qualification tests
Stress
Standard JEDEC conditions
AEC-Q100 Grade 0 AEC-Q100 Grade 1 AEC-Q100 Grades 2 and 3
Preconditioning
MSL 1:
85 °C/85% relative
humidity (RH) for 168 h, unlimited
floor life
MSL 2:
85 °C/60% RH for 168 h,
1 year floor life
MSL 2a:
30 °C/60% RH for 696 h,
4 weeks floor life
MSL 3:
30 °C/60% RH for 192 h,
1 week floor life
Min Level 3, per
J-Std-020
Min Level 3, per
J-Std-020
Min Level 3, per J-Std-020
Temperature cycling
Condition A:
−
55 to 85 °C
Condition B:
−
55 to 125 °C
Condition C:
−
65 to 150 °C
Precondition before
−
55 to 150 °C for
2000 cycles
Precondition before
−
55 to 150 °C for
1000 cycles
−
65 to 150 °C for
500 cycles
Precondition before
Grade 2:
−
55 to 125 °C for 1000 cycles
Grade 3:
−
55 to 125 °C for 500 cycles
Temperature/
humidity bias (THB) THB: 85 °C/85% RH for 1000 h
Precondition before
THB: 85 °C/85% RH for 1000 h
Unbiased highly
accelerated stress
test (HAST)
Unbiased HAST:
130 °C/85% RH for 96 h or
110 °C/85% RH for 264 h
Precondition before
unbiased HAST: 130 °C/85% RH for 96 h
or 110 °C/85% RH for 264 h
High-temperature
storage life
Condition A: +125 °C
Condition B: +150 °C
Condition C: +175 °C
175 °C for 1000 h or
150 °C for 2000 h
150 °C for 1000 h or
175 °C for 500 h
125 °C for 1000 h or
150 °C for 500 h
Note: Typical package-related tests. Additional device tests required: high-temperature operating life, early life failure rate, program/
erase endurance, power and temperature cycling. Source: AEC-Q100, JESD22