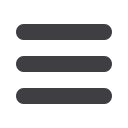
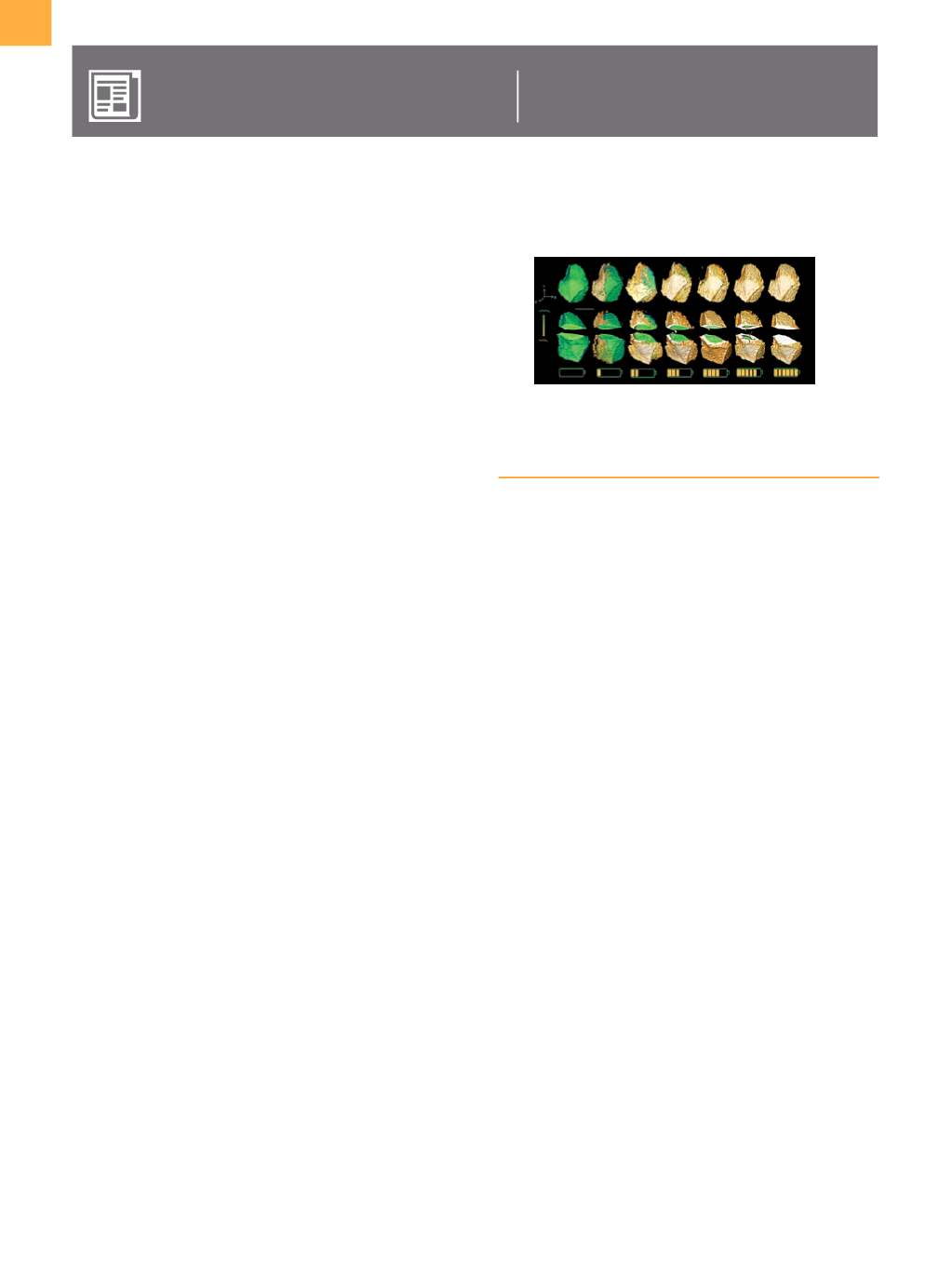
edfas.org
ELECTRONIC DEVICE FAILURE ANALYSIS | VOLUME 18 NO. 4
50
PRODUCT NEWS
CONTINUED FROM
PAGE 48
map and allows the scientists to track chemical reactions
in the battery over time inworking conditions. Their work
was published in the August 12, 2016, issue of
Nature
Communications
.
yield, since the complexity of the advanced IC packages is
increasingwhile the feature sizes are decreasing. The goal
of the EOTPR 5000 is to improve the yield and reliability
of today’s advanced IC packages.
The EOTPR 5000 is truly a one-of-a-kind interconnect
quality inspection tool for advanced IC packaging tech-
nology in high-volume manufacturing environments. No
other tool can inspect and detect like the EOTPR 5000.
Dr. Don Arnone, TeraView’s Chief Executive Officer,
commented, “Weare excitednot only for TeraViewbut also
for the entire terahertz industry to announce the launch
of the EOTPR 5000. This product will be the first terahertz
system ever to be deployed in a mass-production envi-
ronment. It will be deployed to detect weak or marginal
interconnects in advanced IC packages, which no other
testers or inspection equipment can detect. This is a truly
revolutionary inspection system for the world’s leading
IC manufacturers and for outsourced semiconductor
assembly and test.”
According to Martin Igarashi, Vice President of
TeraView’s Semiconductor Business, “Until the EOTPR
5000’s arrival, IC manufacturers did not have 100% con-
fidence in a so-called ‘golden device’ or ‘known good
device’.” How would you know that your golden device is
truly golden? But with the EOTPR 5000, combined with
other existing inspectionmethods, ICmanufacturers now
can breathe a sigh of relief that their devices are reliable,
and when their devices are put in their customers’ smart
phones or tablet devices, their confidence level should
be significantly higher because of the EOTPR 5000. We
are starting beta testing of the EOTPR 5000 at a major IC
manufacturer’s site in Asia shortly, to demonstrate that
this product meets the rigor of the 24/7 ICmanufacturing
environments. This product will be available for custom-
ers in early 2017.”
For more information: Alun Marshall; tel: 44 (0)1223
435380; e-mail:
marketing@teraview.com.
NEW X-RAY IMAGING TECHNIQUE
SLICES THROUGH MATERIALS
Researchers at the U.S. Department of Energy’s
BrookhavenNational Laboratory (Upton, NY) have created
a new imaging technique that allows scientists to probe
the internal makeup of a battery during charging and
discharging, using different x-ray energies while rotating
the battery cell. The technique produces a 3-D chemical
(continued on page 52)
The chemical phase within the battery evolves
as the charging time increases. The cut-away views
reveal a change from anisotropic to isotropic
phase-boundary motion.
Obtaining an accurate image of the activity inside a
battery as it charges and discharges is a difficult task.
Often, even x-ray images do not provide researchers
with enough information about the internal chemical
changes in a batterymaterial, because 2-D images cannot
separate out one layer from the next. Imagine taking an
x-ray image of a multistory office building from above.
Desks and chairs would be seen on top of one another,
and several floors of office spaces would blend into one
picture. It would be difficult to know the exact layout of
any one floor, let alone to track where one person moved
throughout the day.
“It’s very challenging to carry out in-depth study of in
situ energy materials, which requires accurately tracking
chemical phase evolution in 3-D and correlating it to elec-
trochemical performance,” said Jun Wang, a physicist at
the National Synchrotron Source II, who led the research.
Using a working lithium-ion battery, Wang and her
teamtracked thephase evolutionof the lithium-ironphos-
phate within the electrode as the battery charged. They
combined tomography (a kind of x-ray imaging technique
that displays the 3-D structure of an object) with x-ray
absorption near-edge structure spectroscopy (which is
sensitive to chemical and local electronic changes). The
result was a “5-D” image of the battery operating: a full
3-D image over time and at different x-ray energies.
To make this chemical map in 3-D, they scanned the
battery cell at a range of energies that included the “x-ray
absorption edge” of the element of interest inside the
electrode, rotating the sample a full 180° at each x-ray
energy and repeating this procedure at different stages