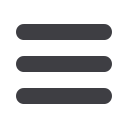
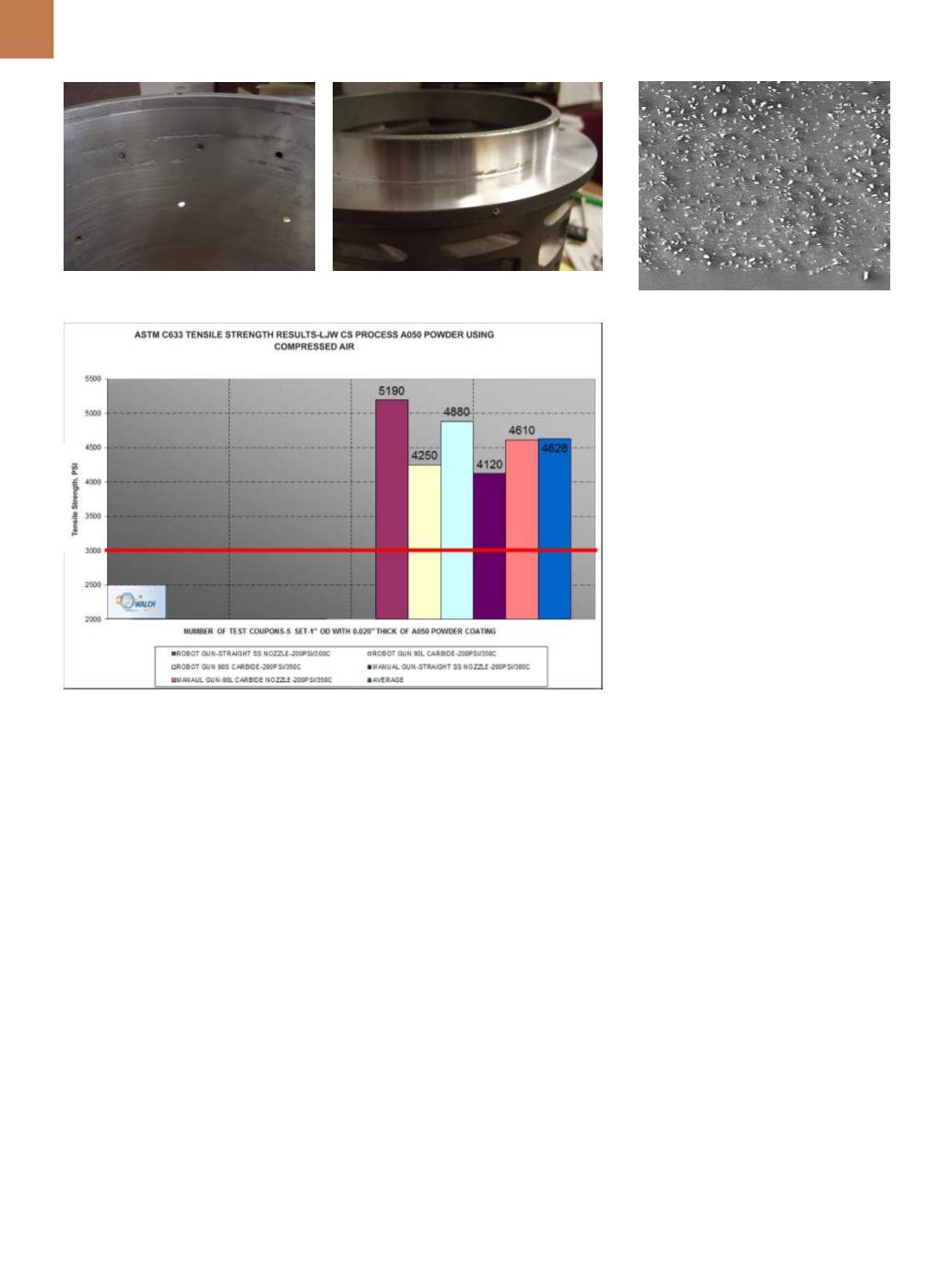
A D V A N C E D M A T E R I A L S & P R O C E S S E S | M A Y 2 0 1 6
2 6
The device’s complex casing is
often made of magnesium or alumi-
num alloys. After years of service, the
housing becomes worn or damaged
beyond normal repair.
Many failures
are located at tight tolerance, heat-
sensitive areas such as stator bores,
exciter bores, pilots, mounting pads,
and mating faces (Fig. 3). These areas
are difficult to dimensionally restore
using conventional thermal methods
such as plasma flame spray.
With the
cold spray approach, these repairs are
both feasible and economically viable.
PROCESS QUALIFICATION
With regard to IDG repairs, pro-
cess qualification included selecting
optimum cold spray grade powders
(in this case, CenterLine SST A050) and
process parameters to produce coat-
ings within the required specifications.
Validation was successfully obtained
by ASTM C633 bond strength tests,
metallographic examination, and 90°
bend tests per the OEM’s repair vali-
dation specifications (Hamilton Sund-
strand SPR52). Bond strength results
indicate that all test samples failed at
stress levels well above the minimum
level required (Fig. 4). Metallographic
examination reveals a microstructure
with porosity levels of less than 2%, no
cracking, and no lack of bonding. A typ-
ical microstructure is shown in Fig. 5.
Further, 90° bend tests with the coating
in tension bent around a 0.25-in. radius
exhibit no spalling or chipping.
REPAIR PROCEDURE AND
QUALITY ASSURANCE
The following steps were taken
to ensure proper surface preparation,
repair, and inspection:
(a) Existing corroded and/or damaged
surfaces were removed.
(b)Spray deposition was facilitated by
pre-machining as necessary.
(c) Grit blasting or other methods
were used to prepare surfaces and
increase surface roughness.
(d)Robotic gun or manual cold spray
took place (Fig. 6a).
(e) Repairs were post-machined per
OEM engineering specifications
(Fig. 6b).
(f) Visual and dimensional inspection
occurred.
(g) Nondestructive examination took
place.
(h) Painting and/or anodizing was
performed as required to improve
corrosion performance (Fig. 7).
The main justification for using
cold spray in the restoration of these
types of components is its ability to
extend component lifespan at a fraction
of their OEM replacement cost, assum-
ing that the part is commercially avail-
able. In many instances, components
are no longer available, thus making
even stronger economic sense for cold
spray restoration. Figure 8 shows exam-
ples of the relative cost of replacement
of IDGs versus the cost of cold spray
restoration to meet required OEM
specifications.
CONCLUSION
Cold spray has become an essen-
tial tool that complements traditional
thermal spray methods for repair
and restoration of IDG housings used
Fig. 3 —
Pitting corrosion damage in a Boeing 747 APU generator housing. Courtesy of L.J. Walch.
Fig. 4 —
ASTM C633 qualification test results. Courtesy of L.J. Walch.
Fig. 5 —
Microstructure of SST A050
cold spray composite deposit showing
well-dispersed aluminum oxide particles
in an aluminummatrix. No lack of bonding
with porosity less than 2%. Substrate is
aluminum 6061. Courtesy of CenterLine
Windsor Ltd.