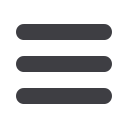
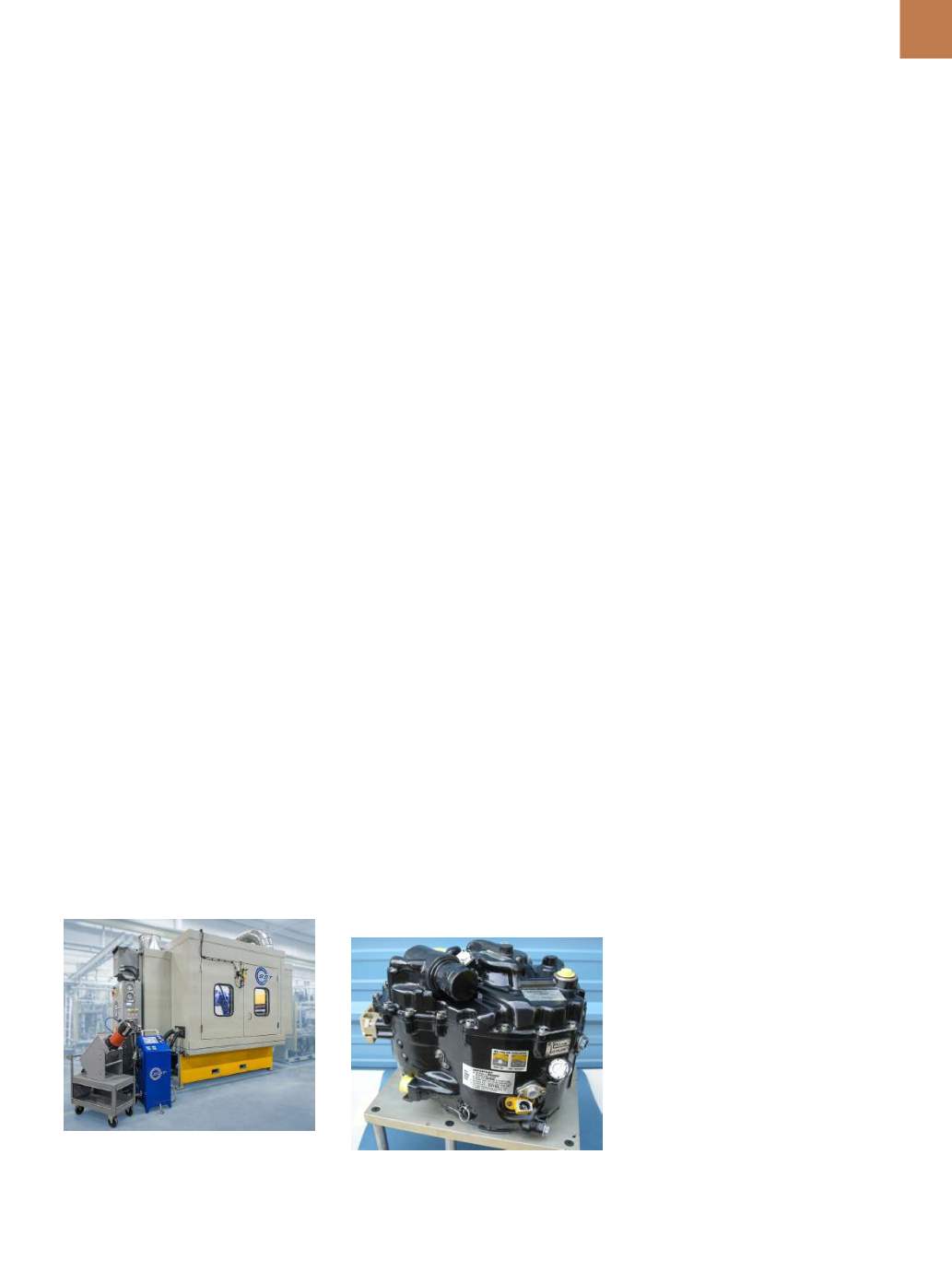
A D V A N C E D
M A T E R I A L S
&
P R O C E S S E S |
M A Y
2 0 1 6
2 5
C
old spray is a solid-state coating
process that uses a high-speed gas
jet to accelerate powder particles
toward a substrate where metal particles
plastically deform and consolidate upon
impact. The technique got its name from
the relatively low temperature involved
in the process, which is typically much
lower than the melting point of both the
spray material and substrate. The con-
cept of “cold spraying” metallic materials
onto substrates dates to the early 1900s.
However, it was not until the 1980s that
the applicability of this technology was
demonstrated and patented by the Insti-
tute of Theoretical and Applied Mechan-
ics of the Academy of Sciences in Novo-
sibirsk
[1]
(high pressure cold spray) and
then by the Obninsk Center for Powder
Spraying
[2]
(low pressure cold spray) in
the former Soviet Union.
In cold spray equipment, air, nitro-
gen, or helium at prescribed pressures
and temperatures is injected into con-
verging-diverging (de Laval) nozzles
to accelerate the gas jet to supersonic
speeds. The spray material, in powder
form, can be introduced upstream in
the nozzle (high pressure cold spray)
or downstream into the diverging sec-
tion of the nozzle (low pressure cold
spray) and is then propelled by the gas
jet against a substrate at high velocities
(Fig. 1). At a given impact temperature,
each type of spray material requires a
minimum level of kinetic energy, above
which acceptable bonding to the sub-
strate may occur. The type of gas, gas
pressure, and gas temperature deter-
mine the amount of kinetic energy
available to accelerate the particulate.
Many common engineering materials
can be successfully cold sprayed at rel-
atively low pressures (less than 300 psi)
and gas temperatures (below 600°C), by
using nitrogen or air.
Metal powder adheres to the sub-
strate and the deposited material is
achieved in the solid state. Therefore,
cold spray deposit characteristics are
unique, making this technique suitable
for depositing well bonded, low poros-
ity, oxide-free coatings using a range of
traditional and advanced materials on
many types of substrates, especially in
nontraditional, temperature-sensitive
applications, such as high-value aero-
space component repair.
COLD SPRAY IN THE
AEROSPACE INDUSTRY
For many years, aluminum and
magnesium alloys have been the
materials of choice for use on both
structural and nonstructural aircraft
components including castings for
housings of many aircraft components.
Well-known performance characteris-
tics, established fabrication methods,
and recent technological advances are
just a few reasons these alloys are still
preferred. An aircraft lifespan often
surpasses the commercial availability
of standard replacement components.
One challenge for the industry is that
this obsolescence makes replacement
components increasingly expensive
or even impossible to obtain. There-
fore, the ability to economically and
reliably restore damaged components
is an important necessity of aircraft
maintenance.
Thermal spray processes, such as
plasma or arc wire spraying, have tra-
ditionally been used to perform limited
repairs on damaged aircraft compo-
nents. However, excessive heat, porosity,
distortion, oxide inclusions, and other
issues associated with conventional
thermal spray have prevented their
widespread use in a vast number of air-
craft repairs. In addition, the thermal
spray plume is usually very wide and
requires labor-intensive masking proce-
dures to protect areas around the repair
from overspray. Masking often rep-
resents a sizeable portion of repair costs.
Over the past decade, pioneering
thermal spray shops serving the aero-
space industry have developed numer-
ous cold spray repair procedures to
bring back to service hundreds of high-
value aircraft components. This requires
the ability to restore these components
to the same quality standards as origi-
nal OEM components while saving the
industry millions of dollars.
REPAIR OF INTEGRATED DRIVE
GENERATOR (IDG) HOUSINGS
One excellent attribute of
cold
spray technology is its ability to create
well bonded, low porosity, oxide-free
coatings in the solid state and at low
temperatures. This is paramount when
restoring
tight tolerance aircraft cast-
ings made of magnesium and/or alumi-
num, which do not tolerate distortion.
Over the past few years, the use of cold
spray has seen a significant increase in
the repair and restoration of housings
for integrated drive generators (IDG),
which are used in commercial aircraft
such as the Boeing 737NG, 747, 777, and
Airbus A320, A330, and A340 (Fig. 2).
An IDG is an in-flight power gener-
ation device that converts the variable
input rotational speed of an aircraft
engine into constant speed, which is
used to drive an AC generator unit con-
tained within the device. Ultimately,
the IDG supplies constant frequency AC
electrical power to the aircraft, greatly
simplifying the design of the aircraft’s
electrical system.
Fig. 1 —
Commercial downstream injection
cold spray system. Courtesy of CenterLine
Windsor Ltd.
Fig. 2 —
Boeing 747 integrated drive gener-
ator (IDG). Courtesy of L.J. Walch.