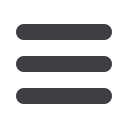
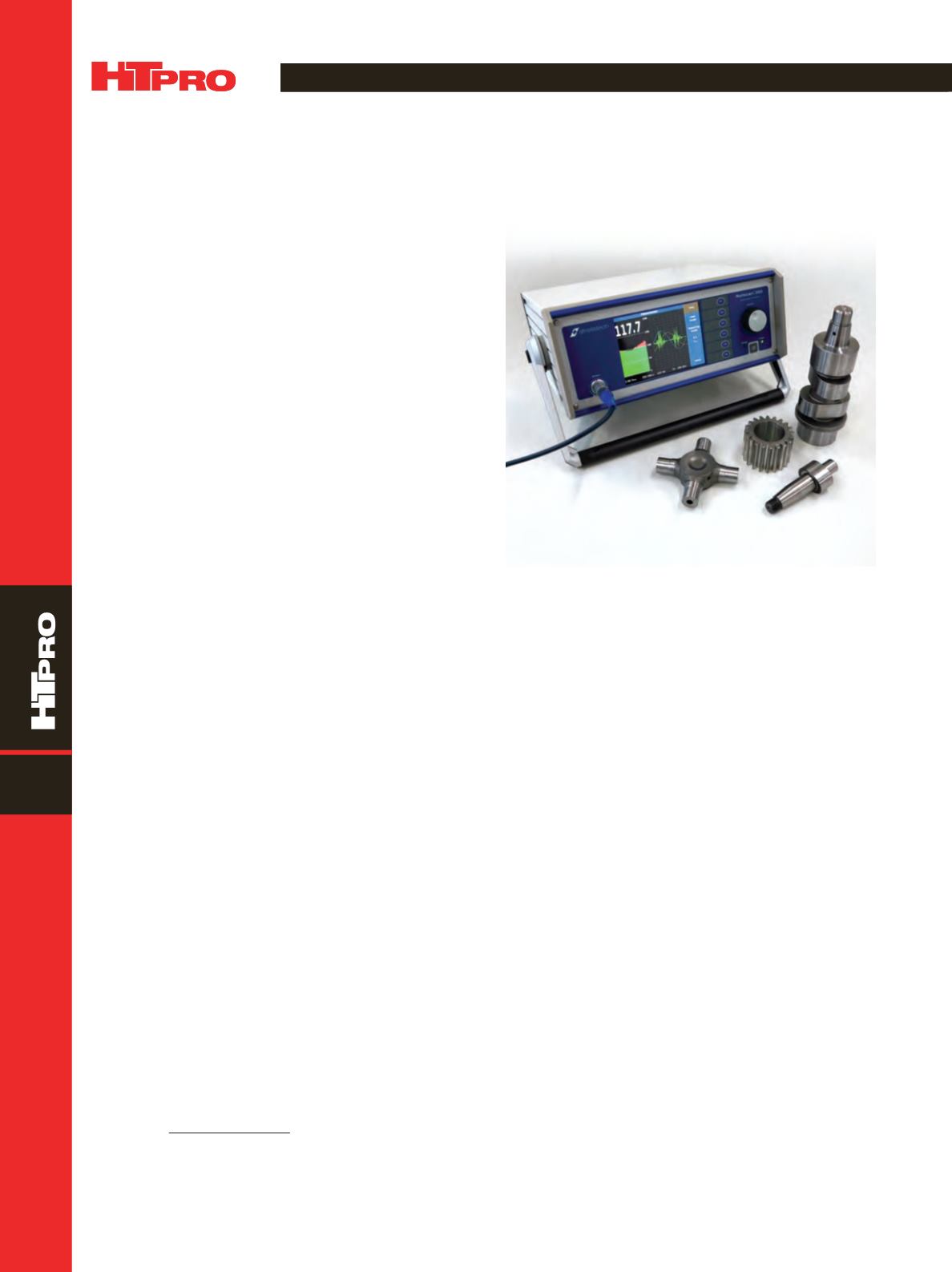
FEATURE
A D V A N C E D M A T E R I A L S & P R O C E S S E S | J U N E 2 0 1 5
3 8
6
T CHNICAL SPOTLIGHT
USING MAGNETIC BARKHAUSEN NOISE TO ANALYZE CASE DEPTH
M
agnetic Barkhausen noise (MBN) analysis is a non-
destructive test method used since the 1980s to
evaluate conditions in a variety of steel components.
Primary applications include detection of thermal damage
induced during grinding and evaluation of case depth in
case-hardened parts. For example, the StresstechGroup uses
its Rollscan Barkhausen noise analysis equipment (Fig. 1),
which combines MBN technology with x-ray diffraction and
hole drilling to solve processing problems including those
related to heat treatment. Further, MBN can be used as a pro-
cess control tool due to its fast, nondestructive operation.
UNDERSTANDING BARKHAUSEN NOISE
MBN occurs when magnetic domains are forced to
reorient or resize, typically in the presence of an alternat-
ing external magnetic field. In ferromagnetic materials, the
magnetization process is not continuous, but is made up of
a series of discrete changes in magnetization that appear to
be step-like. Each step, or rapid change in magnetization, is
known as a Barkhausen jump. Magnetizing a volume of ma-
terial andmeasuring its magnetization via an inductive pick-
up enables observation of Barkhausen jumps. The signal
containing the jumps, which occur in a stochastic manner,
exhibits white noise-like power spectra up to approximately
2 MHz. The stochastic nature, together with the static sound
heard when the pickup is connected to a speaker, is the
source of the term
Barkhausen noise.
Quantity and intensity
of Barkhausen jumps are affected by mechanical stresses,
both residual and applied, along with microstructural varia-
tions such as hardness and carbon content.
When measuring MBN using the traditional method,
the sample is magnetized with an alternating magnetic
field (typically 125 Hz), and the signal containing Barkhau-
sen noise is amplified and filtered in a frequency range of
hundreds of kilohertz (70–200 kHz is standard on the Rolls-
can analyzer). After all extraneous data is removed, the root
mean square (rms) of the remaining MBN signal is calculated
and reported in real-time. This method is frequently used to
detect grinding retemper burn and heat treatment-related
issues such as decarburization.
Many Barkhausen noise analysis applications require
only near-surface analysis. Measurement depth,
D
(
x
), is de-
termined using the following equation:
D
(
x
) =
∫
ƒ
ƒ
2
1
g
(
ƒ
)
e
[–
Ax
n
√
−
ƒ
]
d
ƒ
∫
ƒ
ƒ
2
1
g
(
ƒ
)
d
ƒ
(Eq 1)
where
g
(
f
) = 1 for randomwhite noise,
A
=
√
πμ/ρ
with perme-
ability
μ
and conductivity
ρ
, and
f
1
and
f
2
are the frequency
limits of 70-200 kHz on the noise-like signal that is MBN.
The calculation yields a skin depth of 0.1 mm in hardened
and tempered steel (assuming conductivity of 10
6
/
Ω⋅
m
and relative permeability of 200). This measurement depth
is effective for evaluating properties such as surface hard-
ness and stress, but not other important characteristics
such as case depth.
EVALUATING CASE DEPTH
Evaluating case depth, which is typically measured
in millimeters, requires greater depth sensitivity. This is
achieved by decreasing the frequency for magnetizing and
analysis, as lower frequencies penetrate deeper. However,
the signal is exponentially damped with depth, which is a
problem with this method. Thus, most of the information
comes from the surface and shallow depths.
The solution used in Stresstech’s equipment is to sim-
ply correct for or remove shallow depth information, thus
leaving information from deeper in the part. Two mea-
surements used to accomplish this are a shallow, high-
frequency magnetizing voltage sweep (MVS) measurement
and a deep, low-frequency MVS measurement (Fig. 2).
An MVS measurement is a constant measure of BN
rms while increasing peak-to-peak voltage of the magne-
tizing signal from zero to some value that results in satu-
ration (similar to
H
in magnetic hysteresis). This provides a
relationship between BN rms and magnetizing voltage for
Fig. 1 —
Rollscan 350 Barkhausen noise analysis equipment.