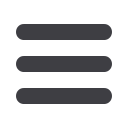
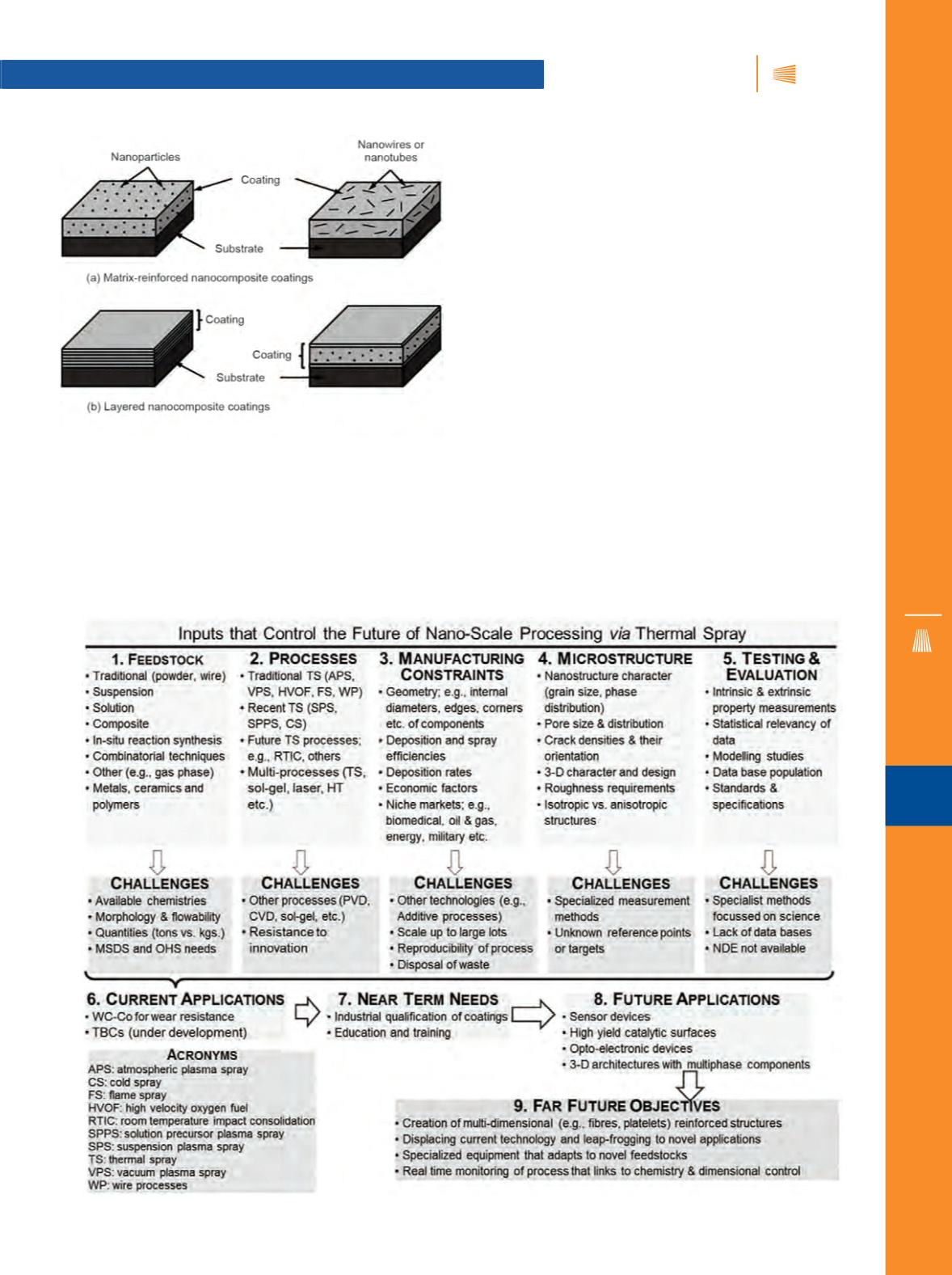
CASE STUDY
iTSSe
TSS
A D V A N C E D
M A T E R I A L S
&
P R O C E S S E S |
M A Y
2 0 1 5
4 1
iTSSe
TSS
9
REVIEW AR ICLE
microstructure of nanocomposite coatings manufactured by
conventional thermal spray processes as well as modern pro-
cesses such as cold spray, suspension, and SPTS. Prominent
nanocomposite materials deposited by thermal spray are as-
sessed in the
Nanocomposite coatings
section, with emphasis
on process-dependent phase transformations and their cor-
relations with nano/microstructure and coating properties.
The properties and applications of selected nanocomposite
coatings with a view towards future uses are presented in the
Properties and potential applications
section.
CHALLENGES AND OUTLOOK
Thermal spray can be segmented into five distinct group-
ings as shown in Fig. 40. The sequence is intended to be logi-
cal—thermal spray starts with an appropriate feedstock and
finishes with testing and evaluation for quality control purpos-
es before being implemented towards specific applications as
indicated in Box 6.
Nanostructured coatings exist in some microstructural
form for the majority of thermal spray coatings, necessitat-
ed by the rapid solidification process
[52,338]
. Thus, microstruc-
tural artifacts such as splat sizes, porosity, cracks, phase
Fig. 6 —
Schematics of nanocomposite coatings: (a) matrix-
reinforced, and (b) multi-layered.
Fig. 40 —
Input criteria that determine the outcomes for nanoscale materials manufactured by thermal spray methods.
powder, wire, or liquid form. (A section of this review is dedi-
cated to their production and characteristics.)
The
Thermal spray deposition: Process and microstruc-
ture
section highlights the formation mechanisms and nano/