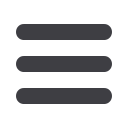
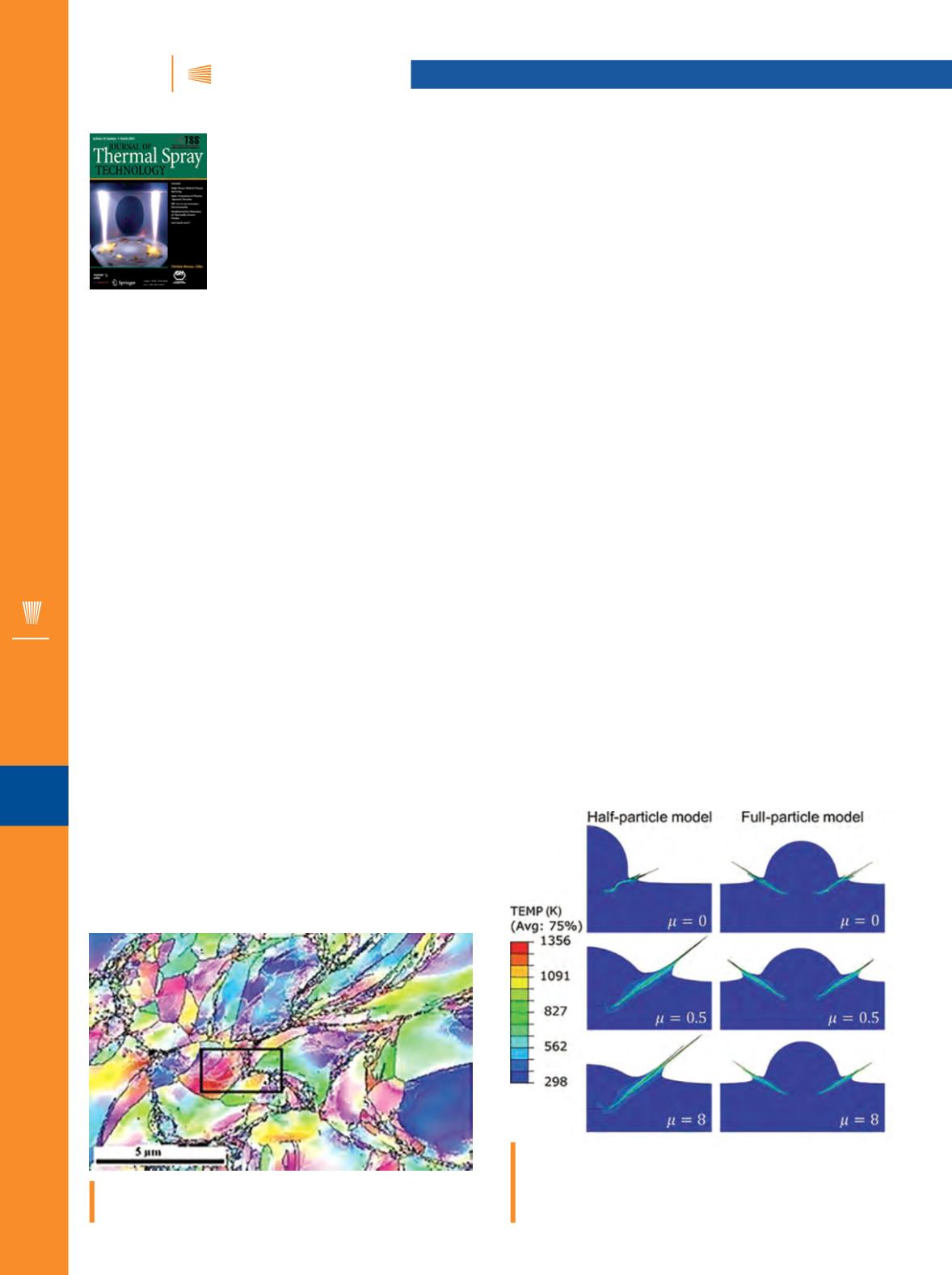
iTSSe
TSS
A D V A N C E D M A T E R I A L S & P R O C E S S E S | M A Y 2 0 1 5
4 6
iTSSe
TSS
14
JTST
HIGHLIGHTS
The
Journal of Thermal Spray Technolo-
gy
(
JTST
), the official journal of the ASM
Thermal Spray Society, publishes con-
tributions on all aspects—fundamental
and practical—of thermal spray science,
including processes, feedstock manu-
facture, testing, and characterization.
As the primary vehicle for thermal spray
information transfer, its mission is to syn-
ergize the rapidly advancing thermal spray industry and relat-
ed industries by presenting research and development efforts
leading to advancements in implementable engineering appli-
cations of the technology. Articles from the February and April
issues, as selected by
JTST
Editor-in-Chief Christian Moreau,
are highlighted here. In addition to the print publication,
JTST
is available online through
springerlink.com. For more infor-
mation, visit
asminternational.org/tss.
MICROSTRUCTURE OF KINETIC
SPRAY COATINGS: A REVIEW
Changhee Lee and Jaeick Kim
Kinetic spray is used in various industries such as au-
tomotive, aviation, and defense because it can produce a
high-performing coating layer. However, because the prop-
erties of the kinetic-sprayed coating layer are significantly
affected by deposited microstructures, the deposited micro-
structures shouldbecontrolledtoacquireanadvancedcoating
layer and a deep understanding of microstructural evolution
must be achieved before controlling the coating layer’s micro-
structure. An overview of contents related to the microstruc-
ture of kinetic-spray deposition is offered. The most powerful
influencing factors in microstructural evolution of the kinet-
ic-spray coating layer are instant generation of thermal energy
and high-strain and high-strain-rate plastic deformation at the
moment of particle impact. A high-density coating layer with
low porosity can be produced, although some micro-cracks
are occasionally induced at the interparticle boundary or
at the particles’ inner region. Also, a microstructure which is
distinct from the inner particle region is created in the vicinity
of the particle-particle or particle-substrate interface region.
However, almost no crystal phase transformation or chemical
reaction is induced since the deposited particles are not heat-
ed directly by a thermal energy source.
THE EFFECTS OF CONTACT CONDITIONS
ON THE ONSET OF SHEAR INSTABILITY
IN COLD-SPRAY
Fanchao Meng, Huseyin Aydin,
Stephen Yue, and Jun Song
Using ABAQUS/Explicit, the effects of contact conditions
between the particle and substrate, including tangential fric-
tion, normal constraint, and contact geometry on the plastic
deformation during the cold spray process are studied. The
onset of shear instability, an event often used to indicate the
establishment of bonding, was found to be very sensitive to
the choice of contact conditions. This suggests that the onset
of shear instability does not serve as an accurate means to
identify the plasticity threshold responsible for bonding. On
the other hand, it is demonstrated that the evolution of the
overall equivalent plastic strain (PEEQ) and the overall von
Mises stress, being linearly proportional toeachother, areboth
independent of contact conditions. Furthermore, it is shown
that an energy value, defined as the product of the PEEQ and
the von Mises stress integrated over all particle elements, can
quantitatively represent the energy dissipated via plastic de-
formation while being independent of contact conditions. The
PEEQ and associated energy value as defined may provide ro-
bust tools to assess the plasticity and the consequent bonding
during cold spray.
EBSD characterization of the as-sprayed Ni coating: (a) Euler
angle map.
Deformed particle/substrate configurations and temperature
contours at the onset of shear instability in a half-particle model
and full-particle model for three representative friction coeffi-
cients
μ
= 0, 0.5, and 8.