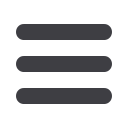

iTSSe
TSS
A D V A N C E D M A T E R I A L S & P R O C E S S E S | M A Y 2 0 1 5
4 8
iTSSe
TSS
16
JTST
HIGHLIGHTS
EFFICIENT LARGE-SCALE COATING
MICROSTRUCTURE FORMATION
USING REALISTIC CFD MODELS
Thomas Wiederkehr and Heinrich Müller
To understand the physical effects during thermal spray
coating layers formation and the deduction of the macro-
scopic properties of a coating, microstructure modeling and
simulation techniques play an important role. A coupled sim-
ulation framework consisting of a detailed, CFD-based single
splat simulation, and a large-scale coating build-up simulation
capable of computing large-scale, 3D, porous microstructures
by sequential drop impingement of more than 10,000 individ-
ual particles on multicore workstation hardware is presented.
Due to the geometry-based coupling of the two simulations,
the deformation, cooling, and solidification of every particle
is sensitive to the hit surface area and thereby pores develop
naturally in the model. The single splat simulation uses the
highly parallel Lattice-Boltzmannmethod, which is well suited
for GPU acceleration. In order to save splat calculations, coat-
ing simulation includes a database-driven approach that reus-
es already computed splats for similar underground shapes at
the randomly chosen impact sites. For a fast database search,
three different methods of efficient pre-selection of candi-
dates are described and compared against each other.
technique. Coatings were produced with a laser power of
2.5 kW, powder-laser spot trailing by 5 s. Coatings were ana-
lyzed for microstructures, microhardness, composition, and
bio-corrosion using SEM-EDS, XRD, hardness tester, and a
Metrohm PGSTAT101 machine. SEM images indicate least
pores and crack-free coating with dark-spots of Ti-HAP for the
20 wt%, HAP as opposed to the 80 wt%, HAP coating, which
was solid, porous, and finely cracked and had semi-melted
Ti-HAP particles. EDS mappings show high content of HAP for
the 80wt%, HAP coating. The diffraction patterns were similar,
even though the Ti-HAP peak was broader in the 80 wt%, HAP
coating and the HAP intensities were lower for this coating ex-
cept for the (004) peak. Hardness values taken at the interface
inferred that the 80wt%, HAP coatingwas least bonded. It was
possible to conclude that when this phase material increased
the hardness dropped considerably. Bio-corrosion tests indi-
cated that the presence of HAP in coatings leads to a kinetical-
ly active coating as opposed to pure titanium coating.
Illustration of the 19 directions e
α
of the D3Q19 lattice model.
MICROSTRUCTURAL AND MECHANICAL
EVALUATION OF LASER-ASSISTED COLD
SPRAYED BIO-CERAMIC COATINGS:
POTENTIAL USE FOR BIOMEDICAL
APPLICATIONS
Monnamme Tlotleng, Esther Akinlabi, Mukul Shukla,
and Sisa Pityana
Bio-composite coatings of 20 wt%, HAP and 80 wt%,
HAP were synthesized on Ti-6Al-4V substrates using LACS
Optimized powder-laser spot interaction.
COMPOSITIONAL DEVELOPMENT AS A
FUNCTION OF SPRAY DISTANCE IN
UNSHROUDED/SHROUDED PLASMA-
SPRAYED CR
3
C
2
-NICR COATINGS
S. Matthews
Thermal spray of Cr
3
C
2
-NiCr composites generates vary-
ing degrees of carbide dissolution into the Ni binder. During
high-temperature exposure, the carbide dissolution zones
precipitate high concentrations of small carbides that devel-
op into finely structured networks. This raises the possibility
of producing unique tailored carbide composite structures
through generation of controlled carbide dissolution and
appropriate heat treatment. The first step in this process is