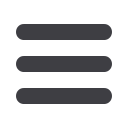
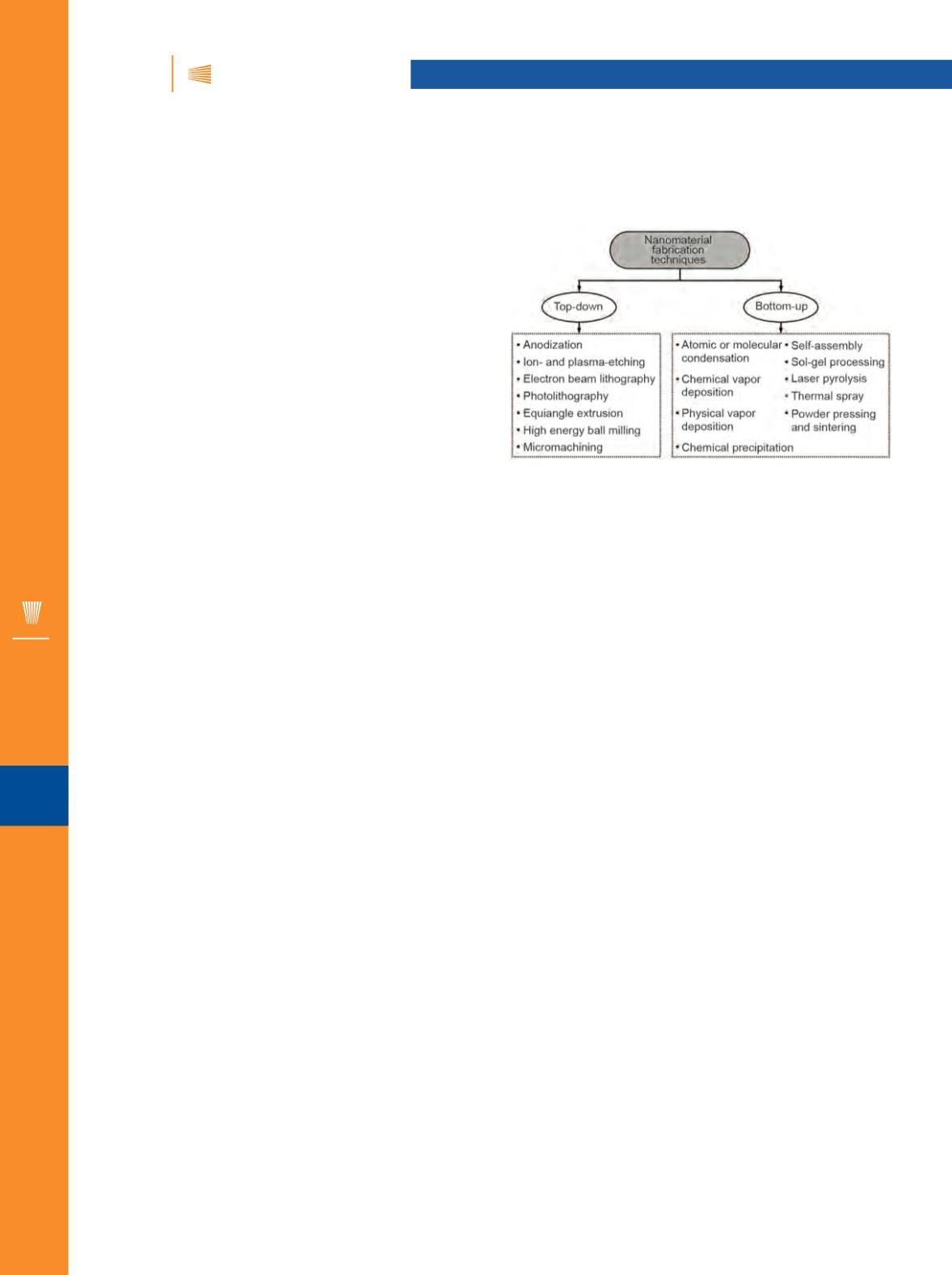
EDITORIAL
iTSSe
TSS
A D V A N C E D M A T E R I A L S & P R O C E S S E S | M A Y 2 0 1 5
4 0
iTSSe
TSS
8
REVIEW RTICLE
NANOCOMPOSITE THERMAL SPRAY REVIEW
Jo Ann Gan
Christopher C. Berndt, FASM*
The following is an excerpt of the full review article, “Nanocom-
posite coatings: Thermal spray processing, microstructure and
performance,” from
International Materials Reviews,
Vol 60
(4), May 2015. The full 50-page review, with 394 references, can
be found at
maneyonline.com/loi/imrthrough mid-June. Copy-
right 2015 Institute of Materials, Minerals and Mining, and ASM
International.
N
anomaterial and nanocomposite processing have
made advances since the 1990s. The growth and op-
portunities this technology offers is based on research
and development funding trends, science citation index (SCI)
publications, and patent applications. This article reviews the
current state of thermal spray nanocomposite coating de-
velopment, while types of commercially available nanocom-
posite thermal spray feedstock materials, as well as those in
development, are assessed.
Thermal spray approaches to depositing nanocomposite
coatings including conventional plasma spray and high veloc-
ity oxygen fuel (HVOF) processes are discussed, as are more
recently developed processes of cold spray, suspension ther-
mal spray (STS), and solution precursor thermal spray (SPTS).
These processes are assessed in relation to their deposition
mechanisms and the specific nanocomposite materials used
for each technique. The unique microstructure of coatings
deposited by each method is highlighted in relation to pro-
cess and compositional control. The exceptional attributes
of nanocomposite coatings, such as mechanical strength and
toughness, wear resistance, and thermophysical and elec-
trical properties are also highlighted with regard to specific
applications.
NANOMATERIAL PROPERTIES
Nanomaterials demonstrate unique optical
[13,14]
, ther-
mal
[15,16]
, mechanical
[17,18]
, electrical
[19,20]
, and magnetic
[21,22]
properties that are not exhibited by their bulk counterparts.
The attributes of nanostructured materials that are size-de-
pendent arise from surface and grain boundary effects due to
a significant increase of surface-to-volume ratio and quantum
effects due to confinement of electron movement; changes in
the electronic structure and interatomic relation; and defect
presence
[12,23]
. Nanomaterials are found in many practical ap-
plications ranging from electronics to aerospace.
Two basic approaches to producing nanostructured
materials include top-down and bottom-up methods (Fig. 3).
The top-down approach involves the breakdown of a bulk
material structure to reduce crystal size to sub-micrometer or
nanoscale. The bottom-up approach involves processing or
building up a material from the atomic scale or nanoclusters
to retain the original nanoscale structural units.
The focus here is on thermal spray to deposit nanocom-
posites—a bottom-up approach. It might be argued that the
impact process during thermal spray coating formation causes
fragmentation of micrometer-sized particles to the nanoscale,
which is a top-down approach. However, because this is not
the preferred formation process that would retain a lamellar
structure, the bottom-up approach is considered dominant.
NANOCOMPOSITE COATING ADVANTAGES
Despite their advantages, bulk nanocomposites can be
expensive to produce due to nanomaterial production costs
and technical limitations in preserving a nanostructure in a
consolidated product due to excessive grain growth
[40]
. Nano-
composite coatings use lesser amounts of nanostructuredma-
terials because they are quite thin—several micrometers up to
a millimeter depending on the deposition technique, and can
potentially cover large areas. Therefore, nanocomposite coat-
ings offer an alternative that takes advantage of the many re-
markable properties of nanomaterials without the production
costs of bulk nanocomposites. There are two types of nano-
composite coatings: matrix-reinforced, where the reinforcing
phase is within nanoscale, and layered coatings, where the
thickness of individual layers arewithin nanoscale dimensions
(Fig. 6).
Thermal spray processes and nanocomposites have al-
ready been reviewed independently; therefore nanocompos-
ite coatings deposited by thermal spray processes in relation
to their processing, microstructure, and performance will be
reviewed here. Feedstock materials for thermal spray come in
*Member of ASM International and Thermal Spray Society
Fig. 3 —
The top-down and bottom-up approaches for nanomate-
rials fabrication.