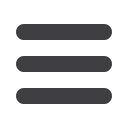
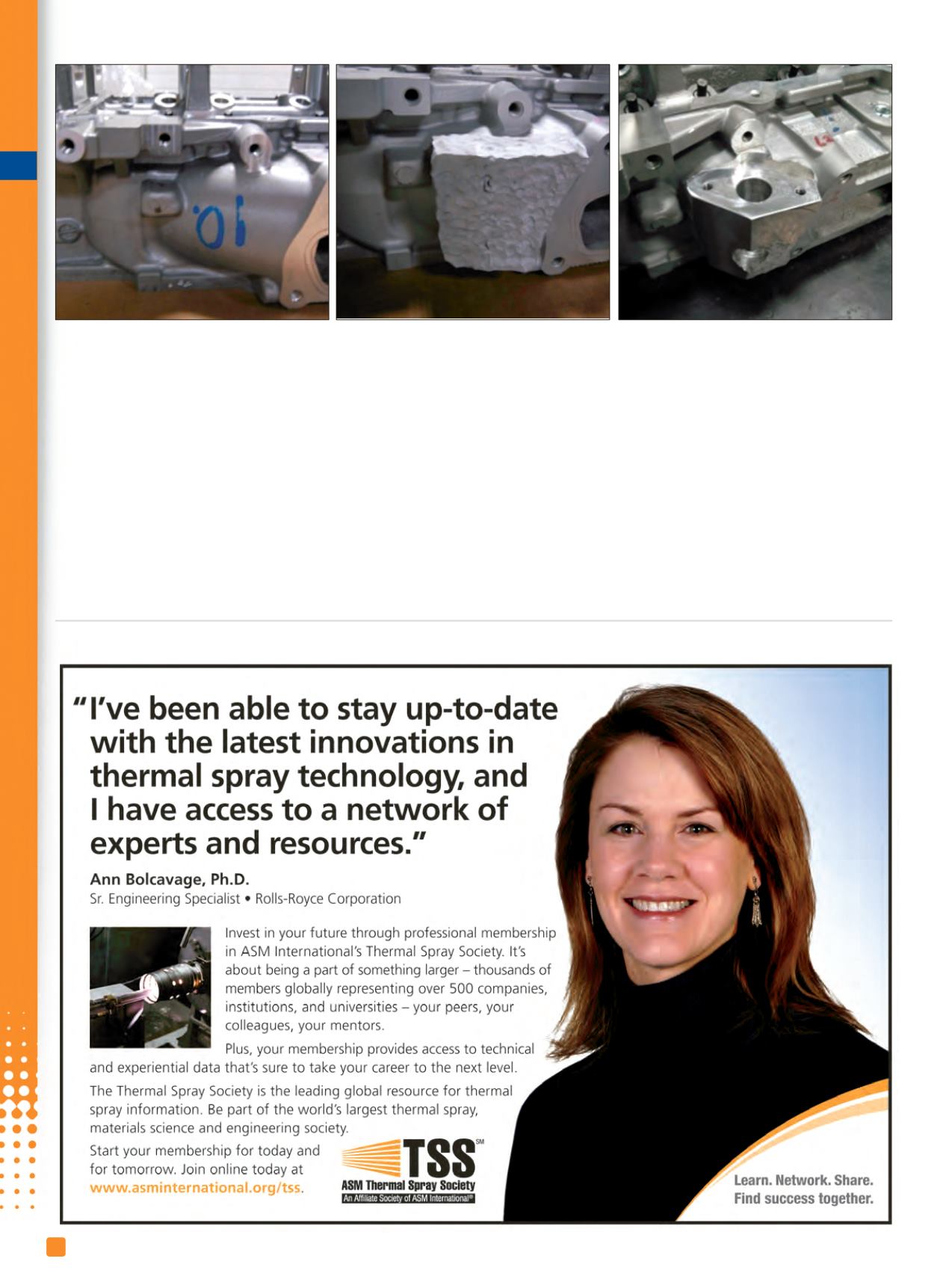
ing on such developments and, in the near future, cold
spray may become a reliable and practical technology
that will enable 3D printing of engineering components
at low temperatures.
iTSSe
For more information:
Julio Villafuerte is corporate technol-
ogy strategist, CenterLine (Windsor) Ltd., 595 Morton Dr.,
Windsor, ON, Canada, 519/734-8868 ext. 4474, julio.villa-
fuerte@cntrline.com,
www.supersonicspray.com.
References
1. ASTM Standard F2792-12a, Standard Terminology for Ad-
ditive Manufacturing Technologies. DOI: 10.1520/F2792-
12A.
2. N.Kapustka and I. Harris, Exploring Arc Welding for Addi-
tive Manufacturing of Titanium Parts,
Weld. J.
, (3), p 32-35,
2014.
3. L. Xue, Laser Consolidation Methodology and Apparatus
for Manufacturing Precise Structures, U.S. Patent 6,504,127,
Jan. 7, 2003.
4. L. Xue and M.U. Islam, Free-Form Laser Consolidation for
Producing Metallurgically Sound and Functional Components,
J. of Laser Applications,
Vol 12, Issue 4, p 160-165, 2000.
5. L. Xue, Y. Li, and S. Wang, Direct Manufacturing of Net-
Shape Functional Components/Test-Pieces for Aerospace, Au-
tomotive, and Other Applications,
J. of Laser Applications,
Vol 23, Issue 4, 2011.
6.
http://www.geaviation.com/company/additive-manufactur- ing.htmlADVANCED MATERIALS & PROCESSES •
MAY 2014
52
i
T
S
S
e
8
Fig. 3 —
Freeform feature added to a prototype machine component by cold spraying. (a) Prior to spraying, (b) as sprayed, (c) finished.
(a) (b) (c)