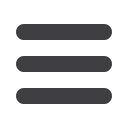
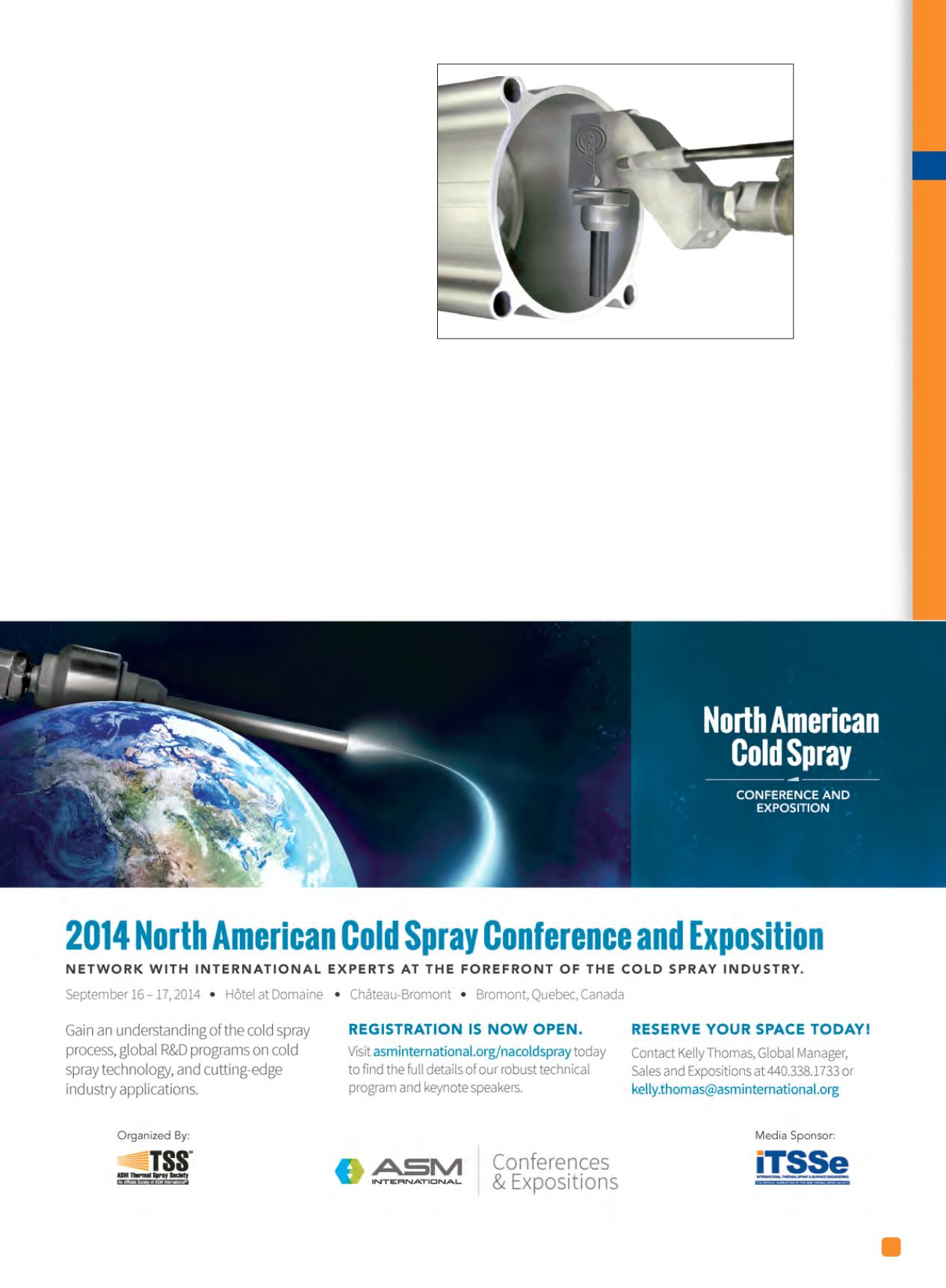
ADVANCED MATERIALS & PROCESSES •
MAY 2014
51
i
T
S
S
e
7
and involves systematic removal of material from bulk
shapes by cutting or drilling to arrive at a final shape. Ad-
ditive manufacturing, on the other hand, builds shapes by
precisely adding and consolidating layers of materials fol-
lowing a 3D digital model
[1]
. Depending on the nature of
the materials involved (e.g., polymers vs. metals) as well as
the application, a wide range of consolidation techniques
may be used including photopolymerization, material jet-
ting, binder jetting, extrusion, powder bed fusion (laser
processing
[3-5]
), direct energy deposition (welding
[2]
and
laser processing
[3-5]
).
Currently, additive manufacturing is mostly used to
create functional prototypes or components made of
polymeric materials because consolidation techniques
for polymers are economical and readily available. At the
other end of the spectrum, additive manufacturing of
functional metallic parts has been limited by the metal-
lurgical challenges associated with consolidating metals
and other elevated temperature engineering materials of
interest. Today, selected metals, such as titanium, cobalt,
chromium, and nickel-base alloys, can be used to create
high-value custom engineered components for aviation
[6]
and medical uses.
The geometrical quality of a complex 3D shape is
dictated by spot size resolution (the smaller the better),
which is why laser beams on powder beads are the pre-
ferred method for producing intricate geometries made
of special alloys. Currently, the smallest spot size for
cold spray deposition is about 4.0 mm, which is suffi-
cient for 3D dimensional restoration of an assortment of
metallic components in the world of remanufacturing or
rapid prototyping (Fig. 3). However, a much smaller
cold spray footprint would be required to produce a
highly finished shape. Manufacturers are already work-
Fig. 2 —
Special right-angle nozzle assembly developed to
access hard-to-reach surfaces.