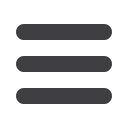
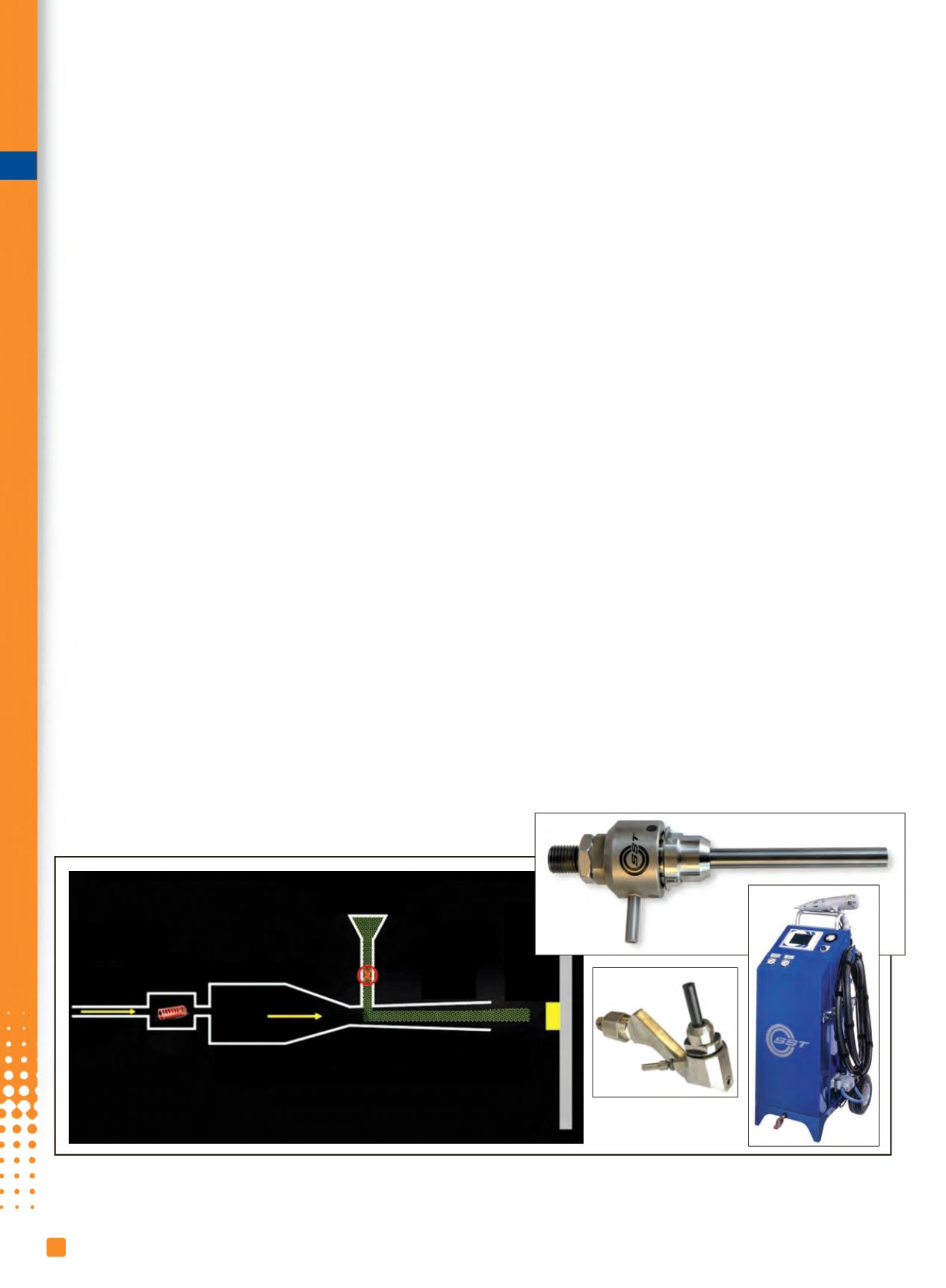
ADVANCED MATERIALS & PROCESSES •
MAY 2014
50
i
T
S
S
e
6
Considering Cold Spray
for Additive Manufacturing
T
hermal spray encompasses a variety of coating
processes that apply metals, polymers, ceramics, cer-
mets, and other materials onto metallic, polymeric, com-
posite, and ceramic substrates. One of these processes is
cold spray, which propels feedstock material against a sub-
strate with enough kinetic energy to produce a dense coat-
ing or freeform at relatively low temperatures.
Cold spray is beneficial in applications that use heat-
sensitive substrate materials or those with difficult-to-reach
spray areas. One example involves spraying inside small-
diameter, heat-sensitive tubes or bores to provide corrosion
resistance. Cold spray produces deposits that are oxide-free
and fully dense with acceptable mechanical properties. The
process requires heating of a pressurized carrier gas (typi-
cally nitrogen or air) that is passed through a “DeLaval”
convergent-divergent nozzle. The divergent section of the
nozzle creates a supersonic gas jet as the carrier gas ex-
pands toward the nozzle exit. The spray material (in pow-
der form) is injected into the gas jet either upstream or
downstream of the nozzle throat.
Depending on the process temperature, each material
requires a specific minimum particle velocity in order to
successfully form a well bonded and dense deposit. The
latter depends on the material’s ability to plastically de-
form upon impact. Therefore, the less ductile the spray ma-
terial, the more particle velocity required to produce
bonding. In practice, a cold-spray-grade powder mix must
contain, at least, one material that can easily deform upon
impact with the substrate surface.
Commercial cold spray systems, including upstream
and downstream injection systems, have been available for
more than a decade. Cold spray was primarily designed for
use in applications that are extremely sensitive to high
process temperatures. Examples include:
• Dimensional restoration of bearing surfaces of cast
aluminum and cast iron for automotive, marine,
locomotive, and earthmoving equipment
• Manufacturing of electrically conductive buses on the
delicate surface of coated conductive glass for heated
glass applications
• Deposition of pure aluminum inside semiconductor
processing chambers to reduce contamination
• Repair of corroded surfaces in magnesium
components for commercial and military aircraft
• Restoration of corrosion damage in nuclear reactor
vessels
In downstream injection cold spray, the spray powder
is injected into the nozzle tube downstream of the throat.
The major benefits of this approach include the ability to
design and build smaller guns for greater accessibility and
maneuverability and the ability to manufacture practical,
low cost, durable engineered consumables that experience
minimal erosion from the spray materials (Fig. 1).
In order to spray inside hard-to-access constrained
spaces, some manufacturers developed special nozzle as-
semblies as seen in Fig. 2. Given the required short stand-
off distance (8-15 mm) and the low temperature of the
process, cold spray is considered superior to other thermal
processes with regard to surgically depositing material onto
hard-to-reach heat-sensitive surfaces, and without the need
for masking.
As manufacturing processes move forward, cold spray
is becoming more attractive as an enabling technology for
3D printing or additive manufacturing. Traditional manu-
facturing relies on subtractive manufacturing techniques,
Julio Villafuerte*
CenterLine (Windsor) Ltd.
Windsor, Ontario
*Member of ASM International and ASM Thermal Spray Society
Fig. 1 —
Downstream injection system SST Series P with manual gun, showing modular easy-access nozzles. All images courtesy of CenterLine
(Windsor) Ltd.
Powder
feeder
Gas supply
Gas heater
Carrier gas
DeLaval
nozzle
Substrate
High-velocity powder
Coating