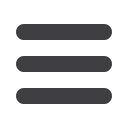
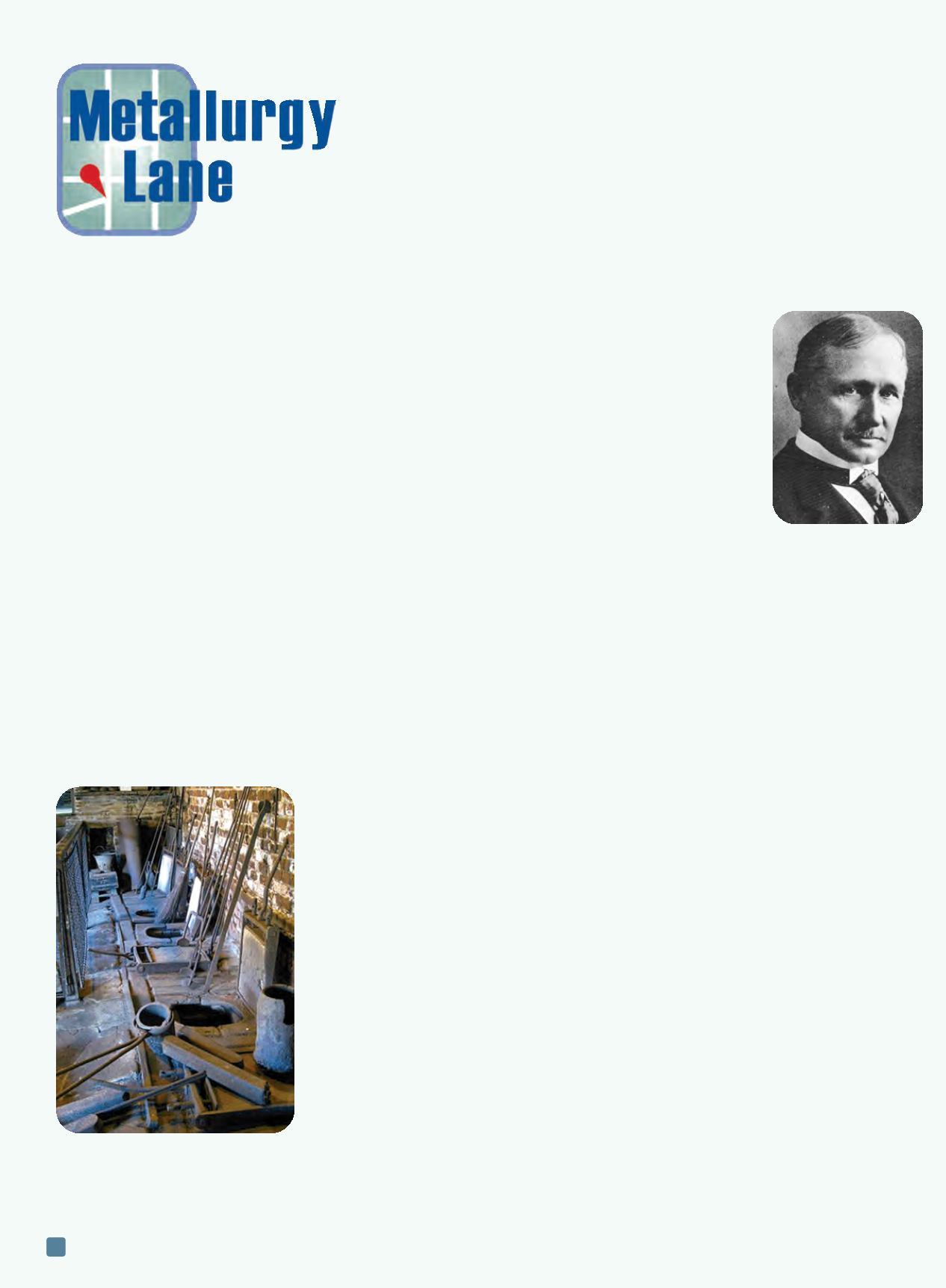
ADVANCED MATERIALS & PROCESSES •
MAY 2014
40
S
imple tools were first devised for hunting
purposes, followed by more complex ones
for agriculture and construction, and always
included efforts to make better weapons for war. Fi-
nally, with the Industrial Revolution, humans began
to invent mass-produced machine tools.
During the middle of the 18th century, British
clockmaker Benjamin Huntsman rediscovered the
ancient Wootz method of melting small quantities
of wrought iron in clay pots, with wood chips to
supply the carbon, as part of his quest for more uni-
form steel to make clock springs. His method was
further refined years later by the British steelmaker
Robert Mushet who simply added pig iron to crude
sponge iron. For more than 175 years (1740 to
1920), this process was used for making steels for
tools. The crucible process, as it was called, was
well suited for making small batches of high-qual-
ity, controlled-chemistry steel.
The tool steels made in the first 100 years after
crucible melting became widely used were simple
iron-carbon alloys. During the 1860s, Mushet was
doing practical processing work that involved
adding other metals to tool steel. His studies led
him to the 1868 discovery that adding tungsten and
manganese in sufficient amounts
caused steel to be extremely hard on
cooling in air from a red heat. At the
time, conventional wisdom said
hardening could only be done by
rapidly quenching in water.
Mushet’s “Special Steel,” as it was
known, contained 2% carbon, 2.5%
manganese, and 7% tungsten. It is
considered the ancestor of all mod-
ern tool steels because it could with-
stand difficult service conditions
and required less resharpening due
to its greater wear resistance.
Taylor and White
revolutionize tool steel industry
Frederick Taylor, an efficiency
expert working on machining stud-
ies at Bethlehem Steel Co. with the
help of experienced metallurgist
Maunsel White, studied the heat
treating variables that affected alloy
tool steel performance. In
the course of their study,
Taylor and White found that
the higher the heating tem-
perature before the steel was
cooled, the greater the use-
fulness and life of the tool.
“Metals men” had known for
years that if steel was heated
at too high a temperature, it
would be ruined, or “burnt”
as they described it. Taylor
and White simply followed
the clues provided by their
own experimental data.
This led them to tem-
peratures in the 2200° to
2400°F range, almost to the
melting point of their steels.
Alloy steel tools containing
tungsten were so greatly im-
proved when heated to these excessively high tem-
peratures before cooling that they could be
operated under conditions so severe that the cut-
ting point would glow to a dull red. Later, with
some refinement in alloy content, these would be
called high-speed steels, and would be said to pos-
sess “red hardness.” The use of high-speed steels
revolutionized the machining industry. Heavier
machine bases were needed to support the stresses
and vibration of the heavier cuts that could now be
used to remove metal.
Alloy development continues
In the meantime, improved alloys that would
provide maximum response to the Taylor and
White heat treatment were being tested in many
advanced industrial countries. J.A. Mathews of
the Crucible Steel Co. reported the results of a
survey he conducted in 1901 on the common
tool steels in use, “Modern high-speed steels
seem to have sprung fairly fully developed from
a variety of sources at almost the same time.” The
change from the old type to the new that Math-
ews is referring to was a rather drastic change in
chemistry from the Mushet steels containing
1.5-2.0% carbon, 2.5-4% manganese and 7-9%
tungsten to the new steels with 0.6-0.8% carbon,
Metallurgy Lane,
authored by
ASM life member
Charles R. Simcoe
,
is a yearlong series
dedicated to the early
history of the U.S. metals
and materials industries
along with key
milestones and
developments.
The Toolmakers: Part I
Man is a toolmaker. In fact, the entire progress of mankind
has been marked by the ability to develop better tools.
Circa 1829, the crucible furnace at
Abbeydale, England, is the oldest
example of the type developed by
Benjamin Huntsman. Courtesy of
www.steelguru.com.
Frederick Taylor
(pictured) and
Maunsel White
discovered that heat
treatment produces
secondary
hardening in
tungsten tool steels.
Courtesy of Library
of Congress/U.S.
public domain.