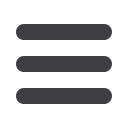
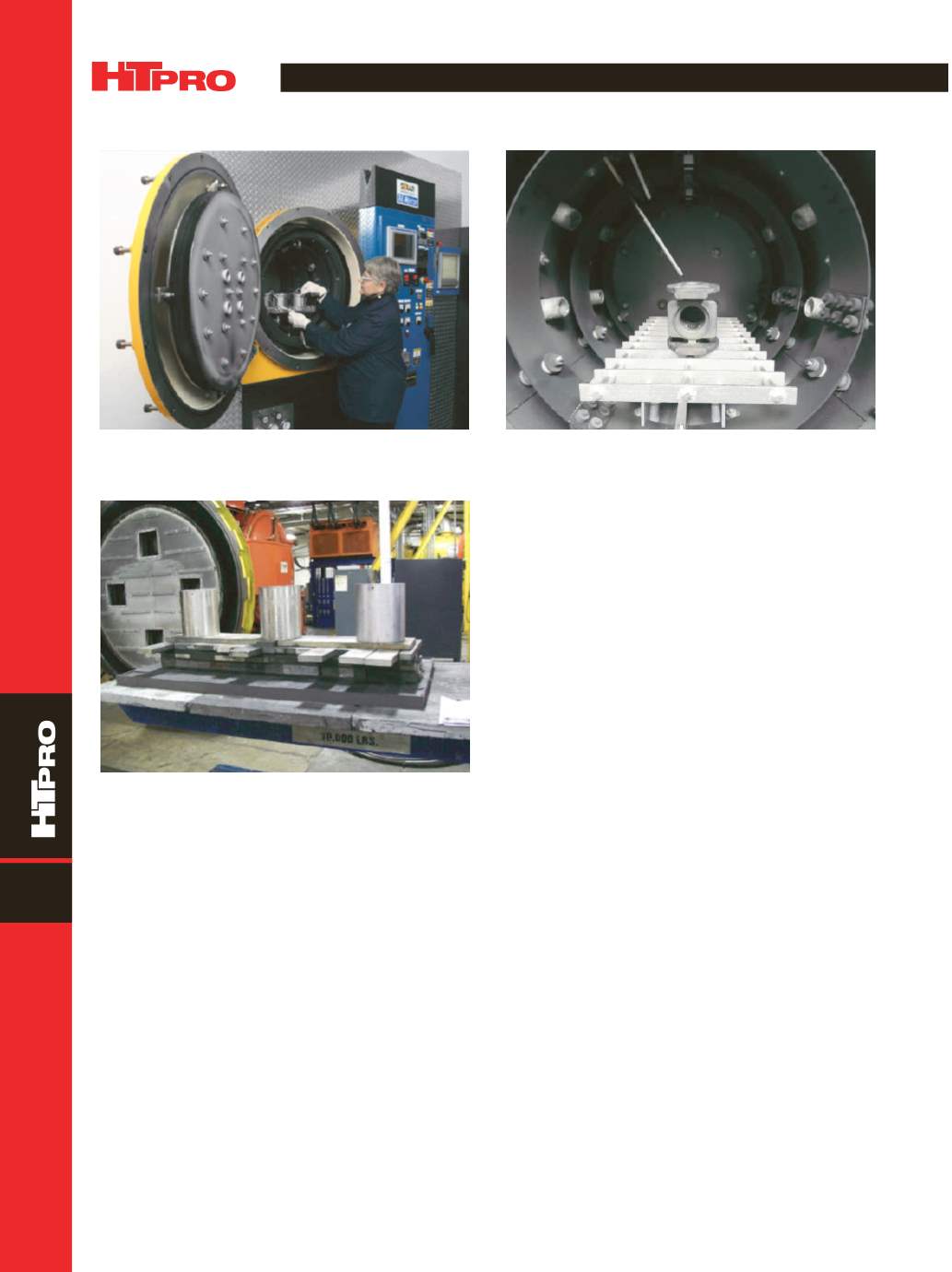
FEATURE
A D V A N C E D M A T E R I A L S & P R O C E S S E S | M A R C H 2 0 1 6
4 4
10
three vacuum heat treating processes per various aerospace
standards—vacuum annealing, vacuum aging, and vacuum
stress relieving.
Typically, prior to heat treating, EBAM baseplates are
severely warped due to high heat concentration of the elec-
tron beam on one side of the base material. To counteract
the warping, AM companies are trying to simultaneously
print on both sides of the base plate. Until the distortion can
be better controlled, vacuum annealing and vacuum stress
relieving processes are used to “creep form” the parts back
into shape so they can be finish machined. Graphite plates,
molds, and stainless steel weights are used to help accom-
plish this task (Fig. 7).
Because BJP involves very little heat during manufac-
turing, downstream heat treating is often challenging. As
with metal injection molding (MIM) metallurgy, the BJP part
must be fully densified by vacuum sintering. Sintering tem-
peratures are often within 10°F of the melting point of the
Fig. 5 —
AM-capable vacuum furnaces range from lab size to
48 ft long.
Fig. 6 —
Heat treating a BJP-printed part requires precise tem-
perature measurement.
base material, so precise pyrometric control is critical. In
addition, slow ramp-up rates and various holding times are
crucial to bake off residual binders remaining within the de-
lubed parts.
CONCLUSIONS
Global 3D printing industry revenues from products
and services exceeded $2.2 billion in 2014. Revenues for the
global market are expected to exceed $21 billion by the year
2020, according to the
Wohlers Report on Additive Manufac-
turing and 3D Printing.
The aerospace industry is not the only niche market
where AM is making its mark. AM in the medical device mar-
ket has also grown significantly. The technology’s geometric
design freedomisparticularlyuseful inorthopedics, enabling
the design of more natural anatomical shapes while printing
the porous surfaces required for bone grafting purposes.
Additive manufacturing is not yet the manufacturing
panacea portrayed by its enthusiasts. Today, 3D printing is
not likely to replace traditional machining, because AM only
eliminates some—and not all—machining. Even the best
finish produced by printing requires final machining and/
or grinding, especially for parts that need to be assembled
to other components. Additive manufacturing is not about
forcing manufacturers and heat treaters to abandon conven-
tional manufacturing processes used for decades. However,
it offers an exciting alternative manufacturing method, espe-
cially when savings can be realized in design flexibility and
fewer manufacturing steps—or even billions of dollars in jet
fuel.
For more information:
Robert Hill is President, Solar At-
mospheres of Western PA, 30 Industrial Rd., Hermitage, PA
16148, 724.982.0660, ext. 2224,
bobh@solarwpa.com,
www. solaratm.com.
Fig. 7 —
Creep-forming is used to flatten a warped EBAM titanium
baseplate by placing weights on the part during heat treatment.