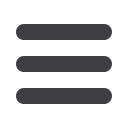
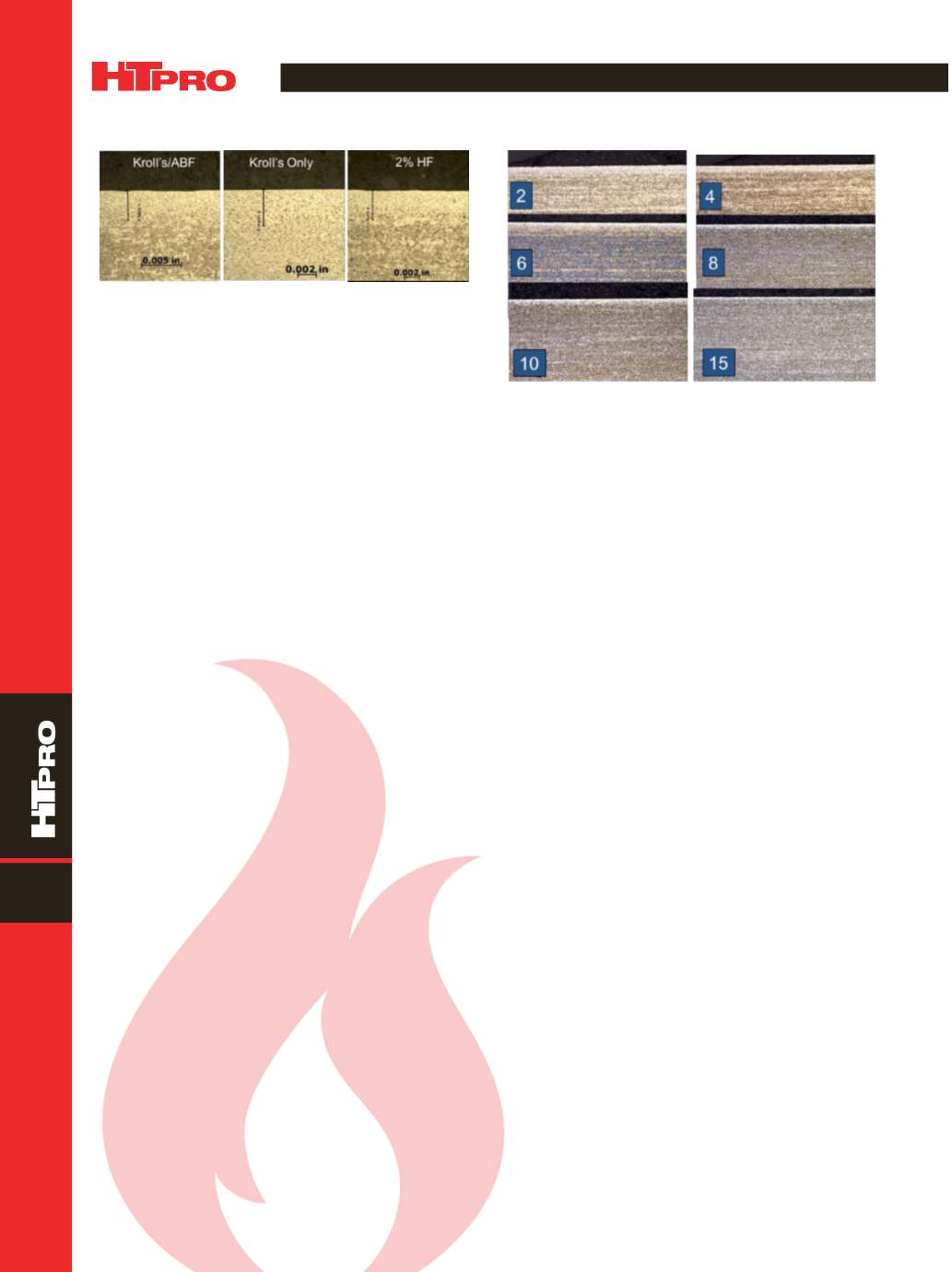
FEATURE
A D V A N C E D M A T E R I A L S & P R O C E S S E S | M A R C H 2 0 1 6
4 8
14
Fig. 6 —
Etchant effect on delineation of alpha case.
Fig. 7 —
Etching time in seconds when etched with 2%HF imme-
diately after polishing.
RGA data reveals that water vapor is the primary oxidiz-
ing residual gas. As temperature increases, carbonmonoxide
and carbon dioxide contribute to alpha case formation in a
graphite-insulated vacuum furnace. Introduction of sacri-
ficial gettering surface area decreased the amount of alpha
case on any given test coupon. Thus, it is most beneficial
to process as many parts (surface area) as feasible in a heat
treatment load. Ramping directly to the hold temperature is
beneficial to production efficiency.
Metallographic comparisons of three etchants indicate
that etchant type and dwell time can considerably influence
the observed depth of alpha case.
For more information:
Donald Jordan is corporate met-
allurgist, Solar Atmospheres Inc., 1969 Clearview Rd.,
Souderton, PA 18964, 800.347.3236,
don@solaratm.com,
www.solaratm.com.
References
1. Matthew J.Donachie, Titanium, A Technical Guide,
ASM International, p 61-62, 2000.
2. Trevor Jones, The Use of a Vacuum Residual Gas Ana-
lyzer and its Evaluation between a Graphite and Molyb-
denum Insulated Hot Zone, presented at Furnaces North
America, Nashville, TN, October 7, 2014.
3. Don Jordan and Harry Antes, Study of Alpha Case
Formation on Heat treated Ti-6-4,
Industrial Heating,
p 45, May/June 2008.
regardless of which etchant is used. Etchant times between
six and 10 seconds using 2%HF delineate comparable alpha
casewhen etched immediately after polishing. Etching times
longer than 10 seconds cause the case to appear shallower
in depth (Fig. 7).
CONCLUSIONS
The surface color or reflectivity of titanium after heat
treatment is independent of the underlying alpha case.
Varying ramp rates or instituting intermediate temperature
holds during outgassing did not minimize the formation of
alpha case, owing to the strong gettering effect of titanium
as revealed by the RGA. Temperature, time, surface area, and
furnace cleanliness all contribute to the extent of alpha case
formation.