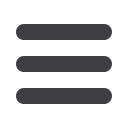
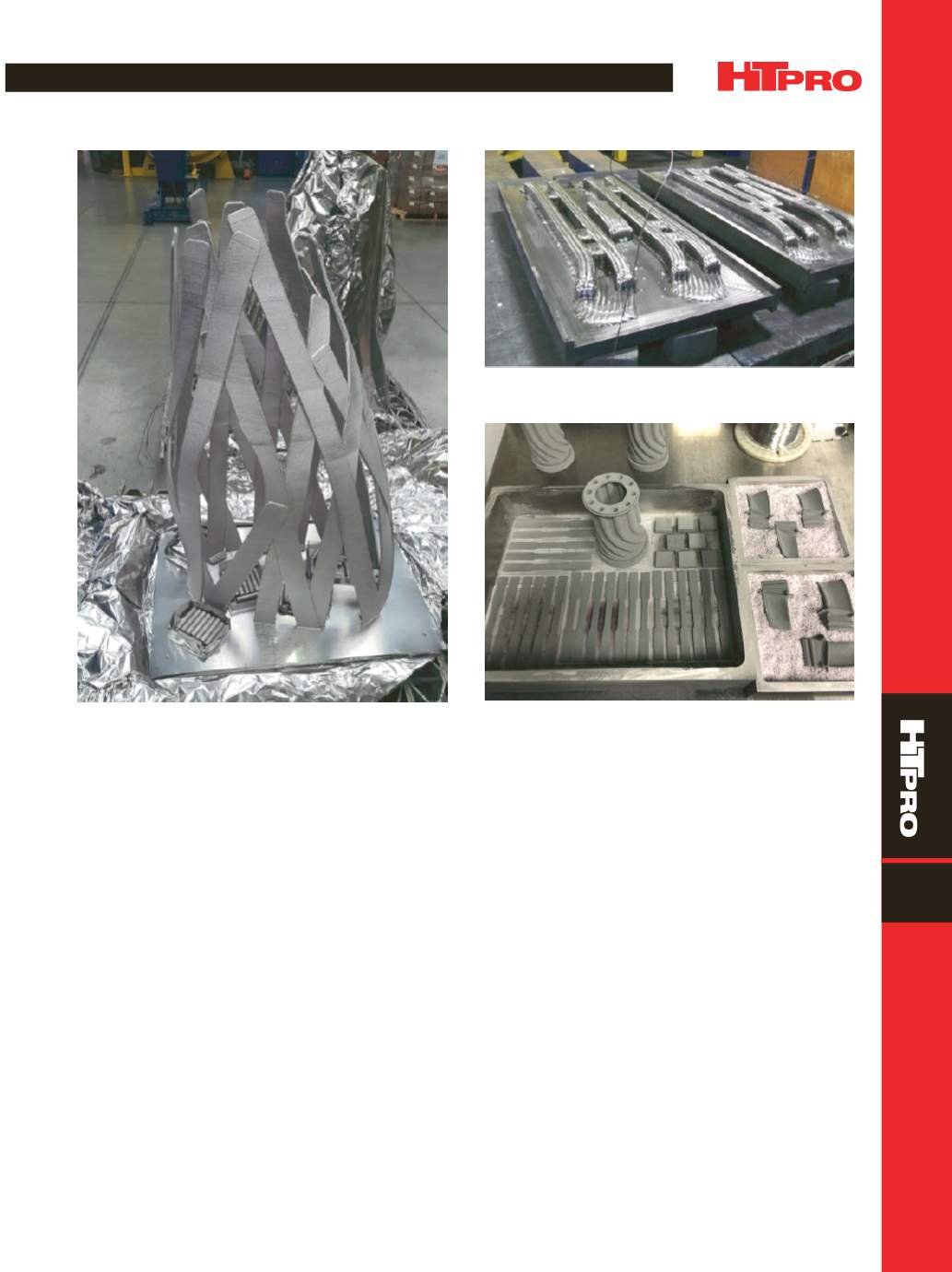
FEATURE
A D V A N C E D
M A T E R I A L S
&
P R O C E S S E S |
M A R C H
2 0 1 6
4 3
9
of similar material within a vacuum chamber. The process
deposits material at a higher rate than DMLS, but the fin-
ished shape is not as fine. Material for EBAM parts that are
vacuum heat treated is predominantly Ti-6Al-4V (Fig. 3).
Binder jet process (BJP)
involves spraying a liquid bind-
er onto a bed of powder at ambient temperature. The con-
glomeration of the binder and powder is solidified using a
very low heat source equivalent to a heat lamp. Each layer
is printed in a manner similar to a printer depositing ink on
paper. The printed part is lowered after each layer solidifies
until the component is complete (Fig. 4). This method has
the lowest manufacturing cost of all additive processes—as
much as 10 times less expensive. However, vacuum heat
treating of BJP parts is more complicated.
VACUUM HEAT TREATING AM PARTS
AM is rapidly developing due to the demand for near-
net shape parts with geometries that are impossible to ma-
chine. Because AM parts require very little material removal
during downstream processing, it is imperative that finished
parts do not have any decarburization or contaminated
surfaces from subsequent thermal processing. Therefore, a
crucial piece of equipment in the additive manufacturing in-
dustry is a well-maintained vacuum furnace, which operates
totally devoid of oxygen, is equippedwith diffusion pumps to
achieve deep vacuum levels, and has very precise tempera-
ture control (Fig. 5).
One of the most important factors for successful inert
vacuum heat treatment of AM parts is a leak-free furnace.
Therefore, a leak rate of less than five microns per hour is
imperative regardless of the chamber size. The furnace must
also be thoroughly baked out at a minimum temperature
of 2400°F prior to an AM furnace cycle. Overall temperature
uniformity is critical for successful thermal processing of any
parts, especially printedparts. For example, BJP components
function as a type of thermocouple sensor. A BJP workpiece
that does not reach or exceed a
±
2°F temperature range ex-
hibits a lack of temperature control in the form of excessive
shrinkage or growth. Therefore, when sintering tempera-
tures (around 2500°F) preclude attaching thermocouples to
the workpiece, a Type S sensor must be strategically located
within inches of the workpiece (Fig. 6). There is tremendous
potential for scrap without precise temperature control.
Solar Atmospheres has processed AM parts of many
shapes and sizes. The DMLS method generally requires
Fig. 2 —
Decorative part for the yacht “Hollow Ribbons” made
using DMLS.
Fig. 3 —
EBAM is used to deposit titaniumwire on a titanium
base.
Fig. 4 —
BJP-printed engine blades and other titanium alloy test
pieces.