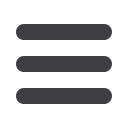
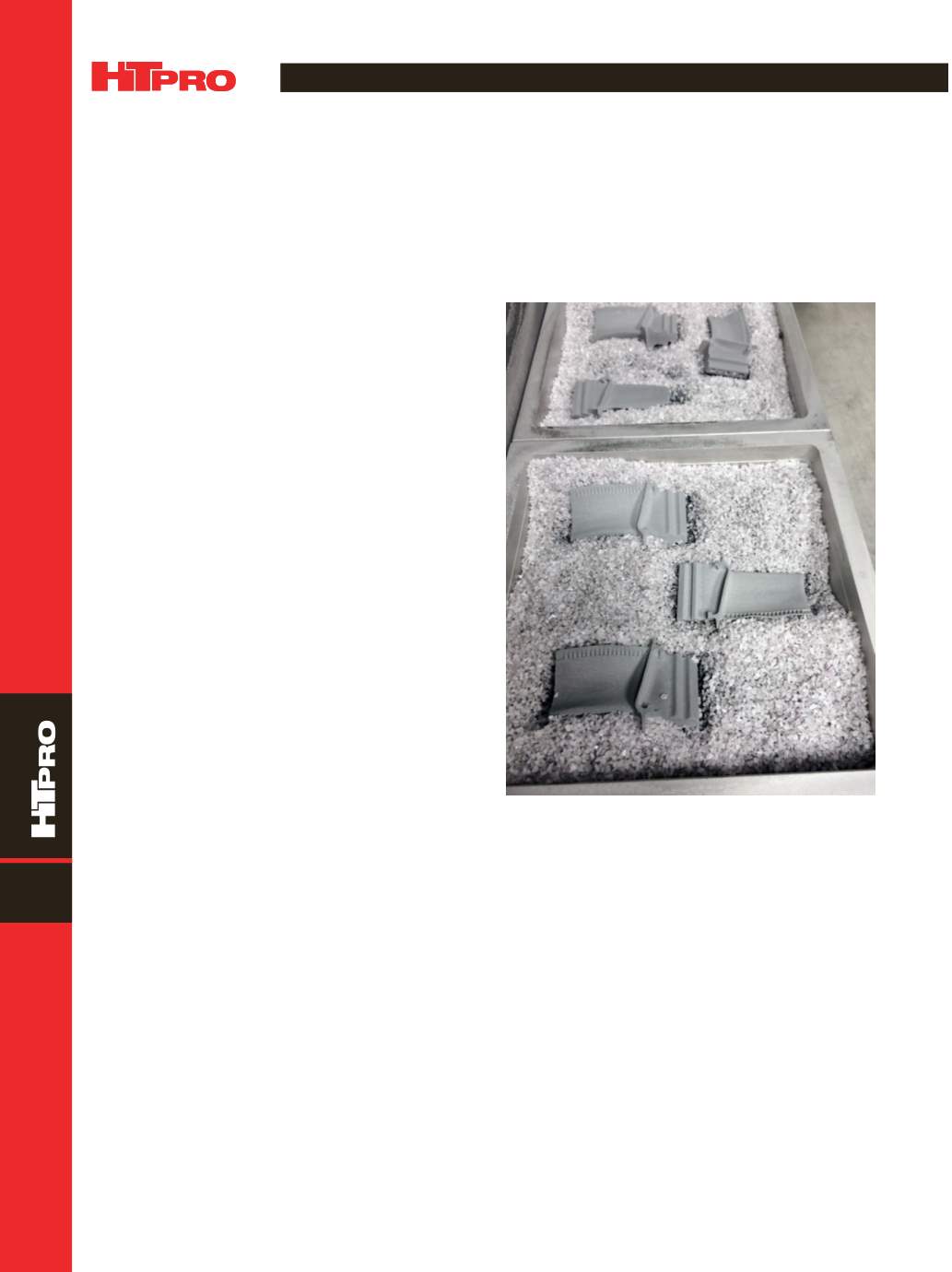
FEATURE
A D V A N C E D M A T E R I A L S & P R O C E S S E S | M A R C H 2 0 1 6
4 2
8
USING VACUUM FURNACES TO PROCESS 3D-PRINTED PARTS
Vacuum heat treating is a crucial step in the additive manufacturing
process cycle to meet required part quality specifications.
Robert Hill, FASM,*
Solar Atmospheres of Western PA, Hermitage, Pa.
A
dditive manufacturing (AM), or 3D printing, is a revo-
lutionary technology that involves converting a digi-
tal model into a net- or near-net shape metallic part
by building up layers of powder or wrought feedstock. Many
believe AM will change the world of manufacturing, while
others believe it will never replace machining, otherwise
known as subtractive manufacturing. The reality probably
lies somewhere between the skepticism and hype.
OPPORTUNITIES AND CHALLENGES
The possibilities and benefits of AM are exciting. A huge
advantage of the process is that it uses only the material
needed to make the part. In addition, unlike subtractive
manufacturing, AM has no design constraints, enabling free-
domof design for functionality. AM also significantly reduces
the time from part design to market: Part manufacturing of-
ten begins within one hour of final design.
The variousmethods of additivemanufacturing are tru-
ly revolutionary technologies, which present many challeng-
es. One of the main hurdles is the high cost of equipment,
where a single printer with ancillary equipment can cost
roughly $1 million. Printer feedstock materials are also ex-
pensive. For example, the price of metallic powders ranges
from $300/lb for alloy steel to $1200/lb for titanium alloys.
The AM field also lacks industry-wide standards. AM
metallurgy consists of multiple recast layers (versus tradi-
tional metallurgy of one homogenous melt of material),
which can result in many inconsistencies. Issues that need
to be resolved include how individual layers of deposited
material are qualified, quantified, and inspected. Acceptable
levels of porosity and density must also be defined. In addi-
tion, certain processes produce parts that exhibit different
mechanical properties longitudinally with the deposit and
transversely across the deposit.
Therefore, the big challenge facing the AM industry is
to identify new, effective quality assurance techniques. In
most cases, certification and validation initiatives for AM
products are being driven by primary contractors such
as General Electric Aviation and Lockheed Martin. Many
aerospace OEMs have spent millions of dollars on the
research and development of new opportunities,
especially for the jet engine. With the design freedom
that AM provides, aeronautical engineers can now
model to the fit, form, and function of a particular part
with minimal constraints. As more AM components
*Member of ASM International
Fig. 1 —
Test turbine engine blades produced by the EBAM
process.
continue to evolve from the lab into production, the
benefits of greater strength, less weight, and significant fuel
savings often outweigh the cost. (Fig. 1).
ADDITIVE PROCESSES
Direct metal laser sintering (DMLS)
is a process in
which metal powder is injected into a high-power
(400-1000 W) focused laser beam operating under tightly
controlled at-mospheric conditions. The laser beam melts
the surface of the target material, generating a small
molten pool of base material. Powder is delivered and
absorbed into the pool, forming a deposit. Typically, the
DMLS process is carried out in an inert chamber to control
oxidation of the metallic pool. Materials processed via this
method include titanium, Inco-nel, and cobalt-chromium
alloys. The low deposition rate of DMLS enables production
of fine details (Fig. 2).
Electron beam additive manufacturing (EBAM)
directs a
high-power electron beam to selectively fuse wire on a plate