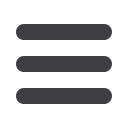
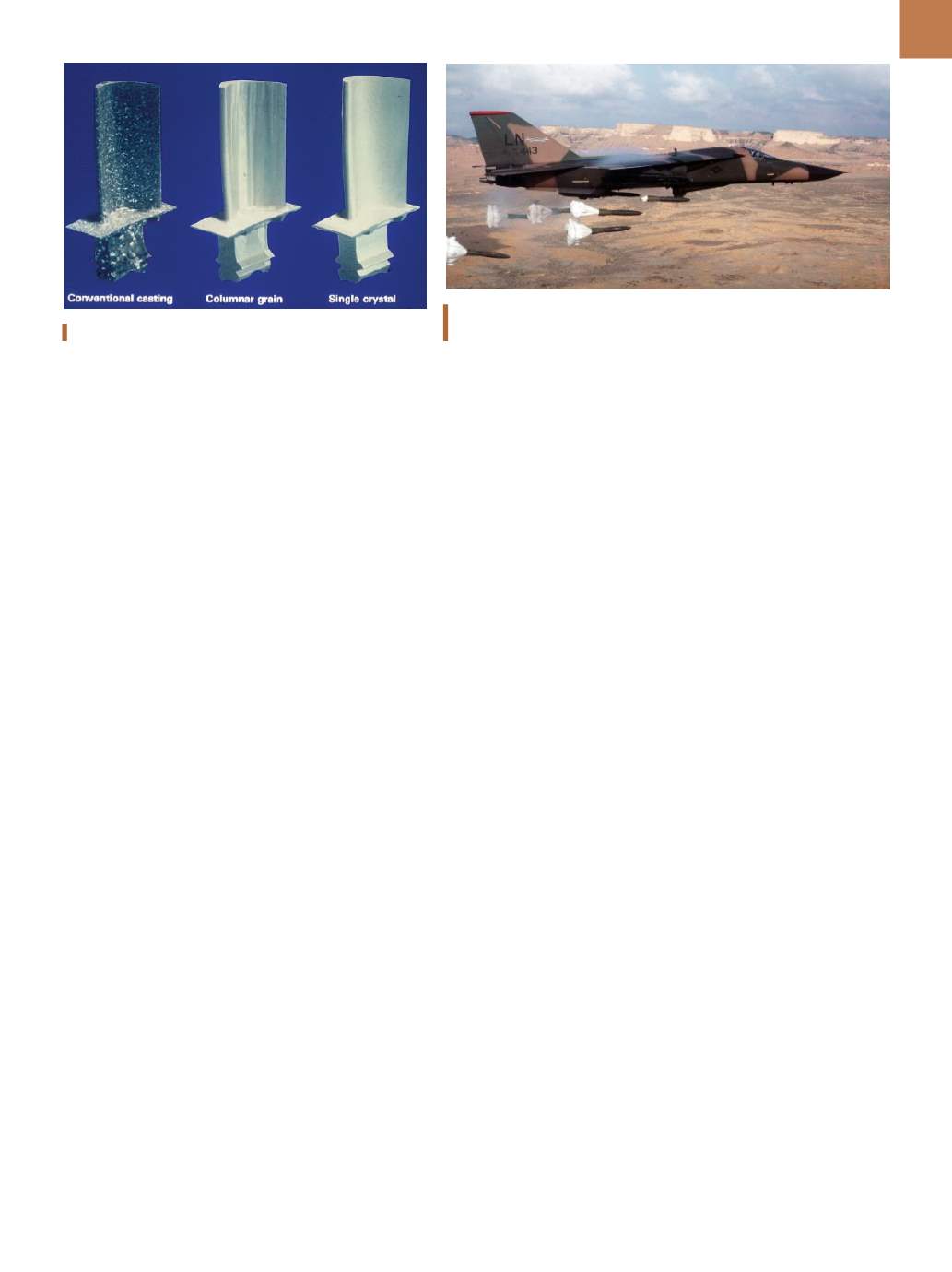
A D V A N C E D
M A T E R I A L S
&
P R O C E S S E S |
M A R C H
2 0 1 6
3 1
direction—the length of the engine
blade—thus eliminating grain bound-
aries across the blade. To accomplish
this, the beginning of solidification
would need to occur from only the bot-
tom of the mold. This required heating
the mold to high temperature to pre-
vent solidification on the mold walls.
Solidification was then limited to a
water-cooled plate at the bottom of
the mold. Although many grains would
form, they would only grow in one direc-
tion as heat was withdrawn through the
casting mold. The process required pre-
cise control of molten metal tempera-
ture, mold shape and wall thickness,
mold temperature, and withdrawing
the mold as the liquid/solid interface
moved up the mold so that the newly
formed solid grains did not remelt.
After this process was perfected in
the laboratory, it had to be translated
into production by the jet engine blade
manufacturers. The first engine to use
directionally solidified (DS) blades was
in the F-111 fighter plane. During the
1970s, DS blades were used in Pratt
& Whitney engines for the Boeing 747
and McDonnell Douglas DC-10, as well
as the new F-15 and F-16 fighter planes.
Engines built by General Electric and
Rolls-Royce used DS blades as well.
SINGLE CRYSTAL
ENGINE BLADES
With the success of laboratory
work on DS blades, attention turned
to making a single crystal version. This
would be the ultimate accomplishment
in the science of metallurgy. Single
crystals had been made and studied in
the past, but they were small samples
from pure metals—copper and zinc. No
attempt had ever been made to make
a single crystal in a metal as complicat-
ed as the nickel base alloys used at the
extreme temperatures of the jet engine,
and no one had ever contemplated
making a useful part. This was virgin
territory for metals technology.
The first breakthrough came when
a member of the team, Steven Copley,
was making a coiled spring to study
the properties of DS crystals. He used a
mold in the shape of a coiled spring sus-
pended in liquid metal with DS crystals
growing from the bottom of the regular
water-cooled plate. As the growing crys-
tals entered the opening of the coiled
mold and grew up the spiral shape, they
had various orientations in space. Crys-
tal orientations grow at different rates
into the liquid metal with one orienta-
tion growing the fastest. As they grew up
the spring mold, the favored orientation
grew ahead of the others until only a
single orientation was present, a single
crystal. This spiral mold, called the “pig
tail,” became the process for producing
single crystal jet engine blades.
ALLOY DEVELOPMENT
The single crystal blade revolu-
tionized the operation of jet engines
and aircraft travel. The engine could
operate at temperatures roughly 100°-
150°F higher than before. The new
blades improved operating efficiency,
fuel economy, and time between en-
gine overhauls. These higher tempera-
tures required new alloys and a new
ceramic coating to protect the blades.
Throughout the program, alloy com-
position had to be adjusted to account
for different grain formations and solid
solution strengthening. The final alloy
had the following composition—10%
chromium, 5% cobalt, 4% tungsten,
1.5% titanium, 5% aluminum, and
12% tantalum. By the end of the 1970s,
single crystal blades replaced the DS
blades in the Boeing 747 and were used
in the new Boeing 757and 767, as well
as the Airbus A310. Single crystal blades
are now standard in all large engines for
commercial and military aircraft.
AWARDS AND HONORS
VerSynder earned his first award
in 1954, the Henry Marion Howe Medal
from ASM International, for his work on
the microstructure of jet engine alloys.
He had only been in research for four
years at this time. For his inventions in
DS and single crystal engine blades, he
received the George J. Mead Medal for
Engineering Achievement from United
Aircraft in 1965, the Clamer Award from
The Franklin Institute in 1973, and the
ASM Engineering Materials Achievement
Award in 1975. He was selected for the
National Academies of Sciences, Engi-
neering Division, in 1981. VerSnyder also
received the highest award given to a ci-
vilian, the National Medal of Technology
and Innovation, presented in the Oval
Office by President Ronald Reagan in
1986. His research and development of
directional solidification and single crys-
tal casting for jet engines is listed by AIME
as one of the 50 greatest advances in the
history of metals. VerSnyder continued
his research at the Pratt & Whitney En-
gine Laboratories for the rest of his ca-
reer. He died in 1989 at the age of 64.
For more information:
Charles R.
Simcoe can be reached at
crsimcoe1@ gmail.com.
Three grain configurations for the same component.
The F-111 fighter jet engine was the first aircraft to employ directionally
solidified blades.