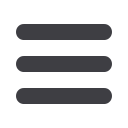
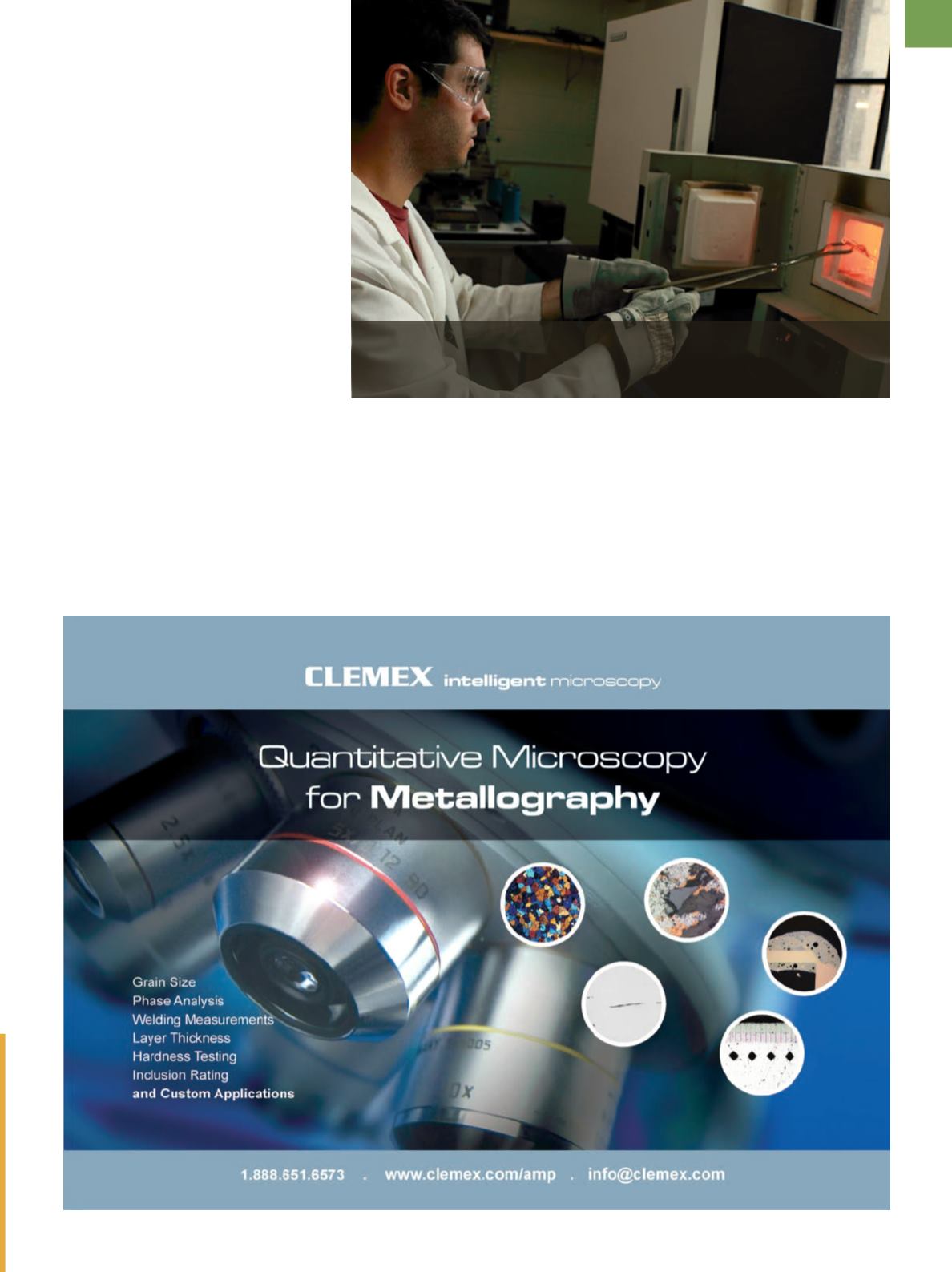
with about 200,000 units per production
line allows the highly concentrated, ef-
ficient use of carbon fiber, while at the
same time meeting all safety require-
ments. Results of an initial rear-impact
crash test demonstrate that the CAMIS-
MA prototype satisfied all of the strength
requirements of current seats built with a
metal structure in large-scale series pro-
duction. In addition to significant weight
savings, CAMISMA offers a further advan-
tage: The manufacturing steps required
in assembly are substantially reduced
through the number of attachment parts
needed, which also saves cost.
johnsoncontrols.com.
Alloying tougher
tungsten
New tungsten alloys being devel-
oped at Massachusetts Institute of Tech-
nology, Cambridge, could replace deplet-
ed uranium in armor-piercing projectiles.
Depleted uranium poses a potential
health hazard to soldiers and civilians.
A new alloy with chromium and
MIT graduate student Zack Cordero removes a vacuum-sealed glass ampoule from a box
furnace operating at 1100°C used to anneal metal powders. Courtesy of Denis Paiste/
Materials Processing Center.
iron (W-7Cr-9Fe) is significantly stron-
ger than commercially available tung-
sten alloys, reports graduate student
Zachary Cordero.
Toachieve this,metal powderswere
compacted in a field-assisted sintering
hot press, with the best result attained
at a processing time of one minute at
1200°C. Cordero achieved ultrafine grain
structure of about 130 nm in the W-7Cr-
9Fe compact, confirmed by electron mi-
crographs. “Using this powder process-
ing route, we canmake big samples up to
2 cm in diameter, or we could go bigger,
with dynamic compressive strengths of
4 GPa.”
For more information: Zachary
Cordero,
zcordero@mit.edu,
www.web.mit.edu.
A D V A N C E D
M A T E R I A L S
&
P R O C E S S E S | F E B R U A R Y
2 0 1 5
9