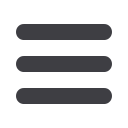
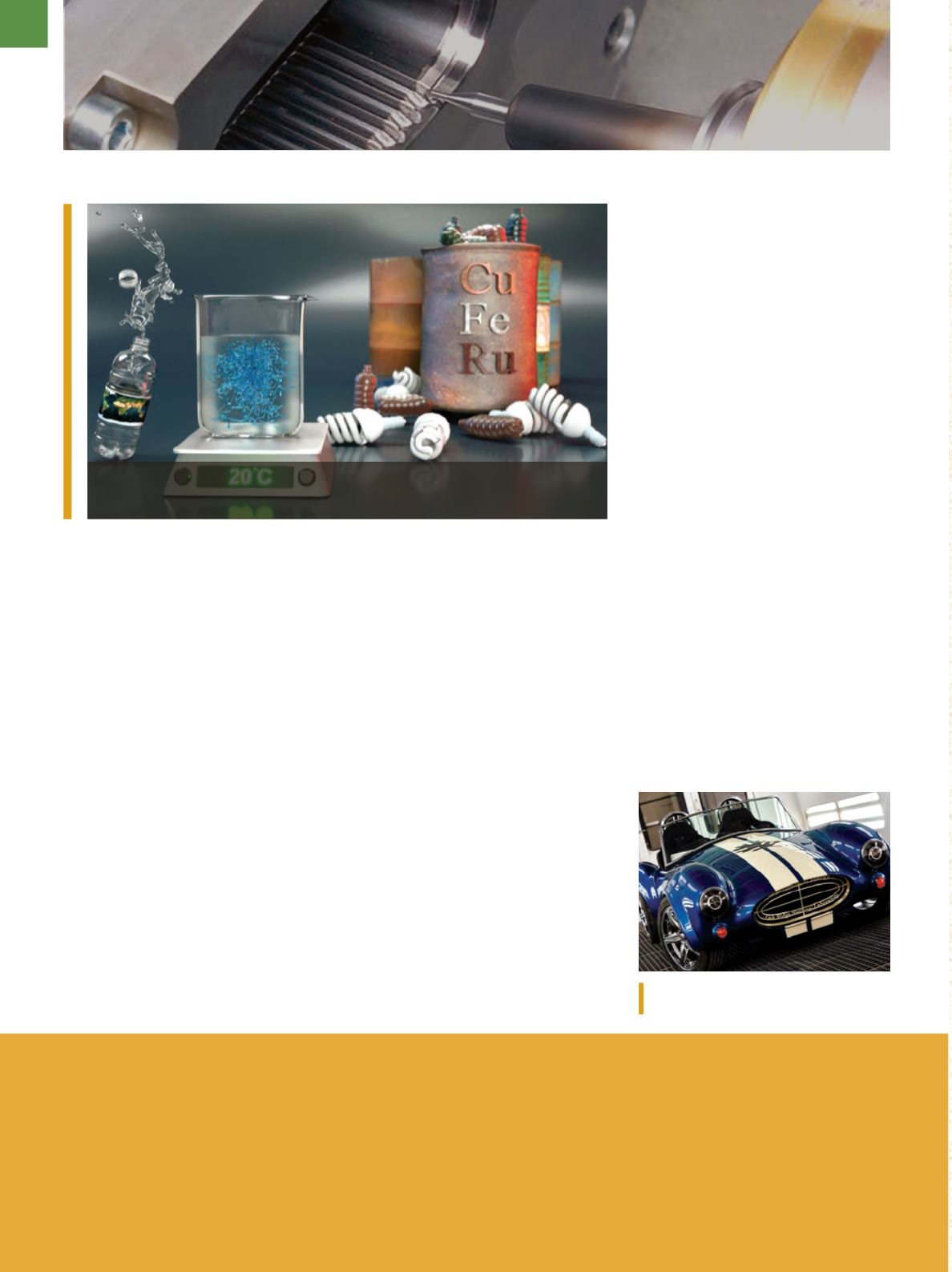
METAL-FREE CATALYST
PROCESSUSES LIGHT FOR
RAPID POLYMERIZATION
Materials science researchers
from University of California, Santa
Barbara, and The Dow Chemical Co.,
Midland, Mich., created a novel way to
overcome a major hurdle preventing
widespread use of controlled radical
polymerization. In a global polymer
industry valued at hundreds of billions
of dollars, a technique called atom
transfer radical polymerization (ATRP)
is emerging as a key process for cre-
ating well-defined polymers for a vast
range of materials, from adhesives to
electronics.
However, current ATRP methods
use metal catalysts, a major roadblock
for applications inwhichmetal contam-
ination is an issue, such as materials
used for biomedical purposes. The new
method does not involve heavy metal
catalysts like copper. Instead, an
organic-based photocatalyst—and light—
serve as the stimulus for the reaction.
“We looked toward developing an
organic catalyst that is highly reduc-
ing in the excited state, and we found
it in an easily prepared catalyst, phe-
nothiazine,” explains Craig Hawker,
director of the Dow Materials Institute
at UCSB. ATRP is already used widely
across dozens of major industries, but
the new metal-free rapid polymeriza-
tion process enables controlled radical
polymerization to be used in new appli-
cations. “Many processes in use today
start with ATRP. This method opens
doors for a new class of organic-based
photoredox catalysts. The develop-
ment of living radical processes, such
as ATRP, is arguably one of the biggest
things to happen in polymer chemistry
in the past few decades,” adds Hawker.
ucsb.edu.
AutoShowfeatures
3D-printedmuscle car
The Department of Energy’s Oak
RidgeNational Laboratory (ORNL), Tenn.,
highlighted its additive manufacturing
research at the 2015 North American In-
ternational Auto Show held in January
in Detroit by showcasing a 3D-printed
Shelby Cobra. The car was printed at
DOE’s Manufacturing Demonstration Fa-
cility at ORNL using the big area additive
manufacturing (BAAM) machine, which
can manufacture strong, lightweight
composite parts in sizes greater than one
cubic meter. The 1400-lb vehicle con-
tains 500 lb of printed parts made of 20%
carbon fiber. It took six weeks to design,
manufacture, and assemble the Shel-
by, including 24 hours of print time. The
new BAAM system, jointly developed by
ORNL and Cincinnati Inc., can print com-
ponents 500 to 1000 times faster than to-
day’s industrial additivemachines. ORNL
researchers say the speed of next-gener-
ation additive manufacturing offers new
opportunities for the automotive indus-
try, especially in prototyping vehicles.
ornl.gov.
PROCESS TECHNOLOGY
A metal-free atom transfer radical polymerization process uses an
organic-based photocatalyst. Courtesy of Peter Allen, UCSB.
BRIEFS
Alcoa,
New York, will invest $190 million in its Davenport Works, Iowa, facility to expand aerospace and industrial products.
Technology to enhance performance of thick aluminum and aluminum-lithiumplate in various applications, including wing ribs
and fuselage frames, will be installed. The investment also includes a very thick plate stretcher for reducing stress introduced
into plate during manufacturing. Company sources say the upgrades will enable production of the largest high-strength
monolithic wing ribs in the industry.
alcoa.com.
3D-printed Shelby Cobra.
Courtesy of ORNL.
A D V A N C E D M A T E R I A L S & P R O C E S S E S | F E B R U A R Y 2 0 1 5
1 2