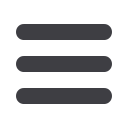
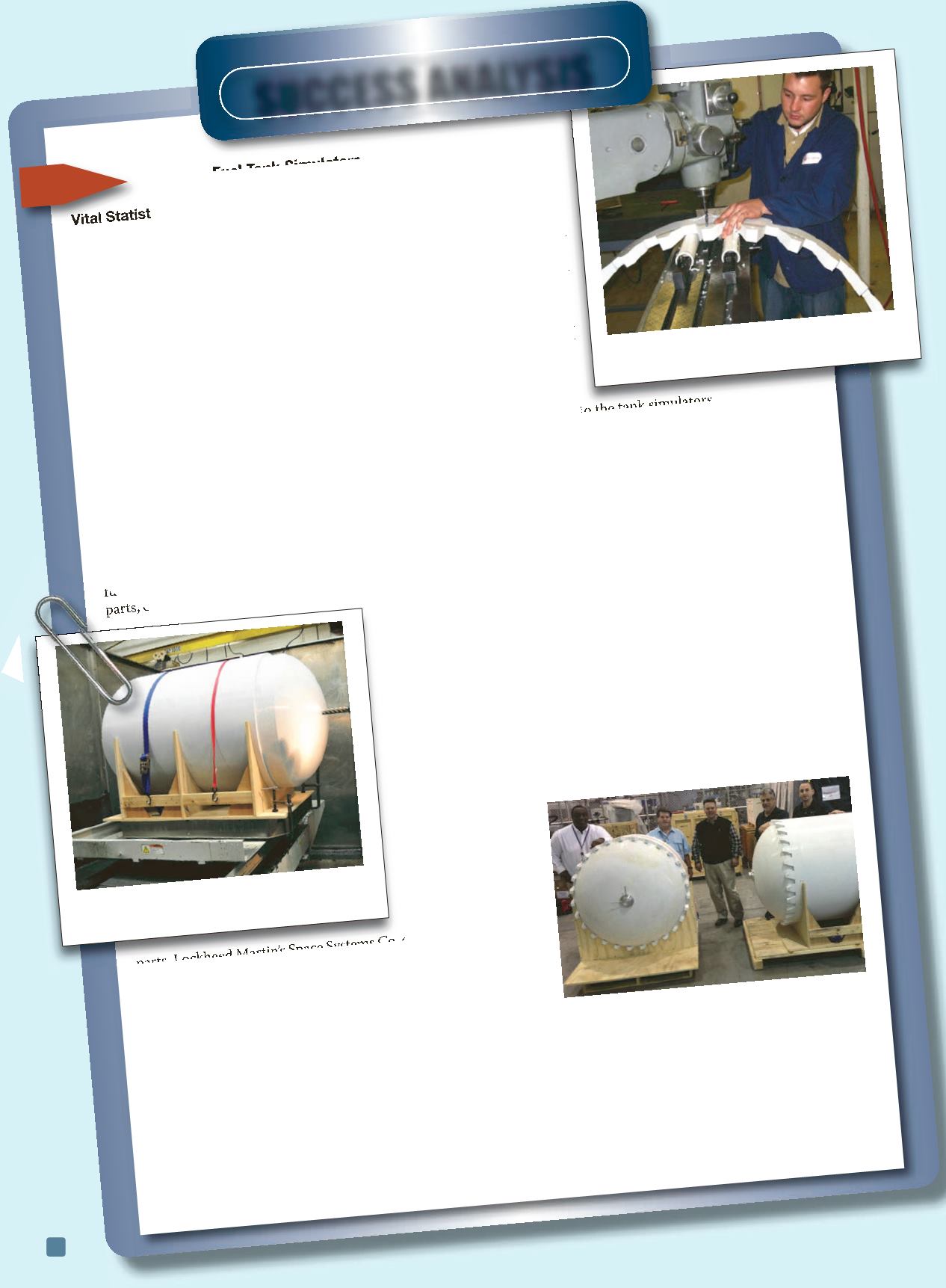
48
Vital Statistics:
In early 2012, Lockheed Martin’s Space Systems Co. began to look for ways to
improve its satellite design. The goal: Devise a satellite that more efficiently uses
the available design footprint to increase payload capacity. This effort required
testing various assembly configurations and producing several simulators and pro-
totypes to validate design changes. One of these changes involved the satellite’s
fuel tanks.
Before building the actual tanks for final use, Lockheed needed to test form,
fit, and function—and assembly—by using tank simulators. However, producing
test parts with traditional manufacturing methods was not an option given the
tight deadlines and financial constraints: Machining the larger tank at 6.75 × 3.8
× 3.8 ft and the smaller one at 3.8 × 3.8 × 3.8 ft would take longer than six months
and cost around $250,000. Recent advancements in large-scale 3D printing moti-
vated Lockheed to apply Stratasys’ fused deposition modeling (FDM) technique to the tank simulators.
Although Lockheed owns several additive manufacturing machines, this particular application involved part sizes and
project deadlines that exceeded its in-house capacity. Parts needed to be built in many pieces and bonded together, re-
quiring an army of machines and a crew of FDM finishing experts. That’s when they turned to the aerospace team at
RedEye, a division of Stratasys Inc.
Success Factors:
The larger tank was built in 10 separate pieces, and the smaller in six, using polycarbonate material. Combined, the
fuel tanks took nearly two weeks to print, requiring approximately 150 hours per section. Based on the sheer size of the
parts, customized fixtures were needed to support the structures as they were bonded together and then shipped to a ma-
chining facility to meet specifications. Once machining was complete, final
assembly took 240 hours.
“These are the largest parts we’ve ever built using FDM,” says Joel Smith,
RedEye’s aerospace and defense account manager. “We completed an exten-
sive design review to determine the best orientation and slice height to en-
sure we could accurately build and bond the sections together in post
processing to meet the dimensional requirements.”
About the Innovators:
As a division of Stratasys, RedEye is one of the world’s largest providers
of rapid prototyping and additive manufacturing services and has a network
of more than 150 3D printers worldwide. RedEye uses Stratasys’ FDM and
PolyJet 3D printing
technologies to help
companies with
all
phases of product de-
velopment, from con-
ceptual modeling to
production of end-use
parts. Lockheed Martin’s Space Systems Co. designs, develops, tests,
manufactures, and operates advanced technology systems for na-
tional security, civil, and commercial customers.
What’s Next:
The tanks went through several quality assurance and accuracy
measurements and were approved for the first concept assembly.
Next, Lockheed will take what they learned from the first phase to optimize design and assembly to print the second
iteration of tanks.
Contact Details:
Joel Smith, Strategic Account Manager for Aer
ospace and DefenseRedEye, a division of Stratasys
Inc. 8081 Wallace Rd., Eden Prairie, MN55344
866.882.6934,
godigital@redeyeondemand.com,redeyeondemand.com
The RedEye and Lockheed Martin team with
the 3D printed tank simulations.
Adding inserts to the 3D printed tank
simulation rings.
ADVANCED MATERIALS & PROCESSES •
JULY 2014
3D Printed Fuel Tank Simulators
Specimen
Name:
SucceSS AnAlySiS
Both 3D printing and traditional
manufacturing methods were used to machine
the 3D printed tank simulations.