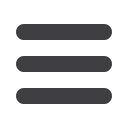
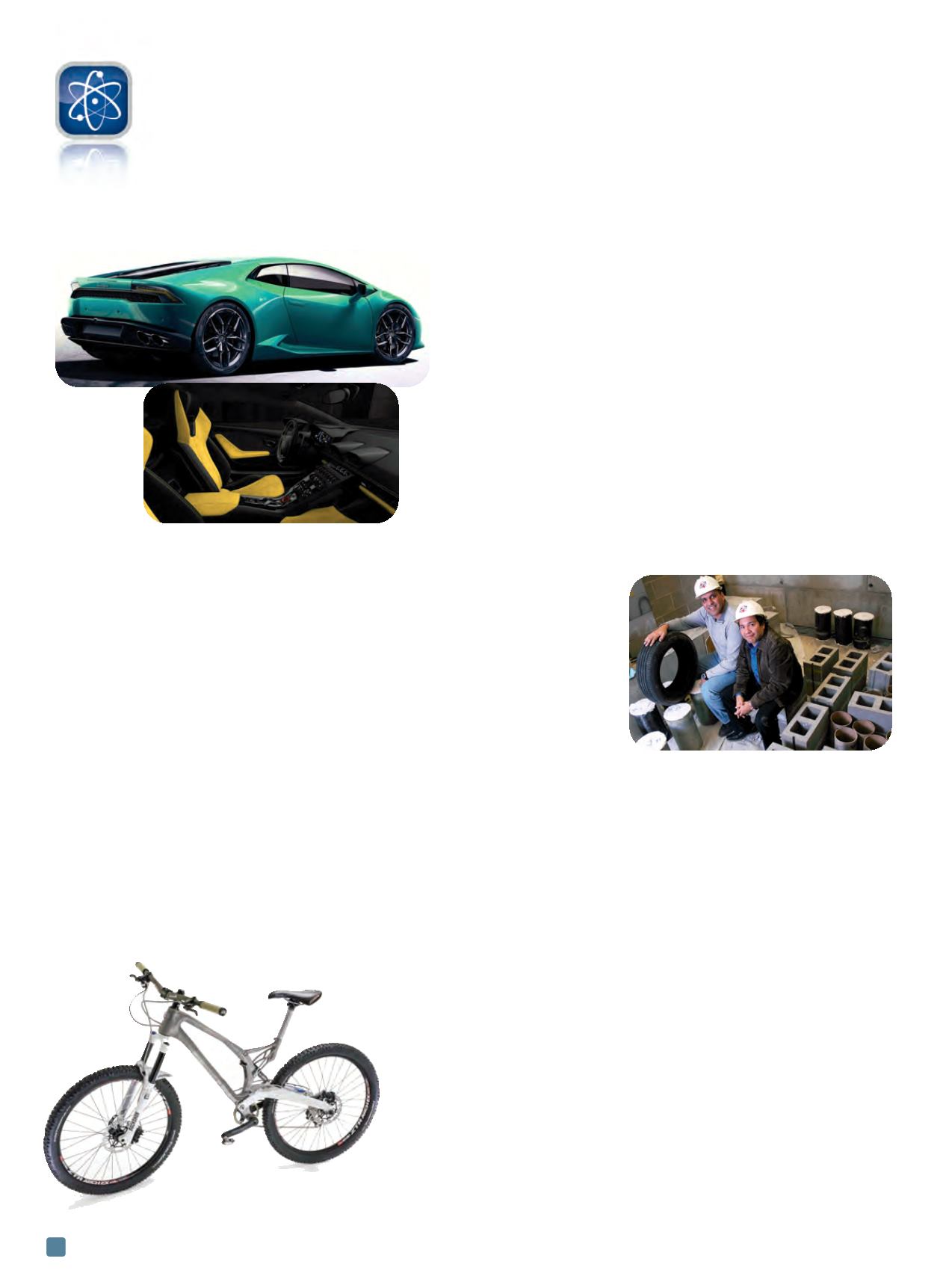
Suede-like material has new Lamborghini covered
The Lamborghini Huracán LP 610-4 offers several cus-
tomizable interior options jointly conceived by Lamborghini
and Alcantara, Italy. The material combines technical and
functional performance features including durability, light
weight, grip, and breathability. The cockpit can be customized
by choosing among seven different options for seats, lower
dashboard, door panels, center console, and glove box.
Alcantara is composed of roughly 68% polyester and 32%
polyurethane for increased durability and stain resistance. Both
the appearance and feel of the material is similar to suede. Alcan-
tara is produced by combining an advanced spinning method with
chemical and textile production processes that interact with each
other. Since 2009, Alcantara remains certified as carbon neutral,
having defined, reduced, and offset all CO
2
emissions derived from
its activity.
www.lamborghini.com,
www.alcantara.com.
Eco-friendly rubber bricks
Mohamed A. ElGawady, a researcher at Missouri University of Sci-
ence and Technology, Rolla, is testing new masonry blocks made from
ground tires. “Rubber has a lot of benefits in addition to its sustainabil-
ity,” says ElGawady, associate professor of civil, architectural, and environ-
mental engineering. “It’s very durable and provides good insulation.
Among their many potential benefits, these new blocks could cut heat-
ing bills by 50%.”
ElGawady has been working with Midwest Block and Brick, Jefferson
City, Mo., to create the blocks, which are made from sand plus scrap tires
ground to fine particles. These rubber-added blocks, called rubberized
blocks, were constructed with a variety of ratios of sand-to-rubber parti-
cles before arriving at the right balance. A compression machine is used to
test and compare the strength of prisms built with the rubberized blocks
to conventional concrete masonry blocks. Both types of blocks are tested in an environmental chamber where they
undergo cycles of extreme temperatures and humidity levels, simulating different weather conditions. The rub-
berized blocks are also tested under cyclic compression loads, simulating earthquake forces. “Construction with
these new blocks could improve a building’s resiliency during an earthquake by acting as shock absorbers,” says
ElGawady.
For more information: Mohamed A. ElGawady, 573/341-6947,
elgawadym@mst.edu,
www.mst.edu.
3D-printed bike frame is light and tough
A 3D-printed titanium bicycle frame was created by Renishaw and Empire Cycles, both in the UK. The frame
was manufactured in sections from a titanium alloy, using additive manufactur-
ing (AM), and then bonded together. The alloys have a high ultimate tensile
strength (UTS) of more than 900 MPa when processed using AM, and achieve near
perfect densities of greater than 99.7%, according to Renishaw. The frame
was designed using a process called topological optimization—an ap-
proach that optimizes material layout within a given design space for a
specific set of loads and boundary conditions so that results meet per-
formance targets. The companies eliminated many downward-facing
surfaces that would otherwise need wasteful support structures. In part-
nership with Swansea University, frame testing will continue, both in the
laboratory and on the mountainside, using portable sensors. Because no tool-
ing is required, continual design improvements can be made easily
and at minimal cost.
www.renishaw.com/en,
www.empire-cycle.com.
ADVANCED MATERIALS & PROCESSES •
MAY 2014
6
interest
of material
Mohamed A. ElGawady, associate professor
of civil, architectural, and environmental
engineering (right) with graduate student
Ahmed Gheni.
Complete bike with 3D-printed titanium
alloy frame and seat post bracket.