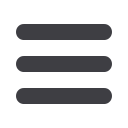
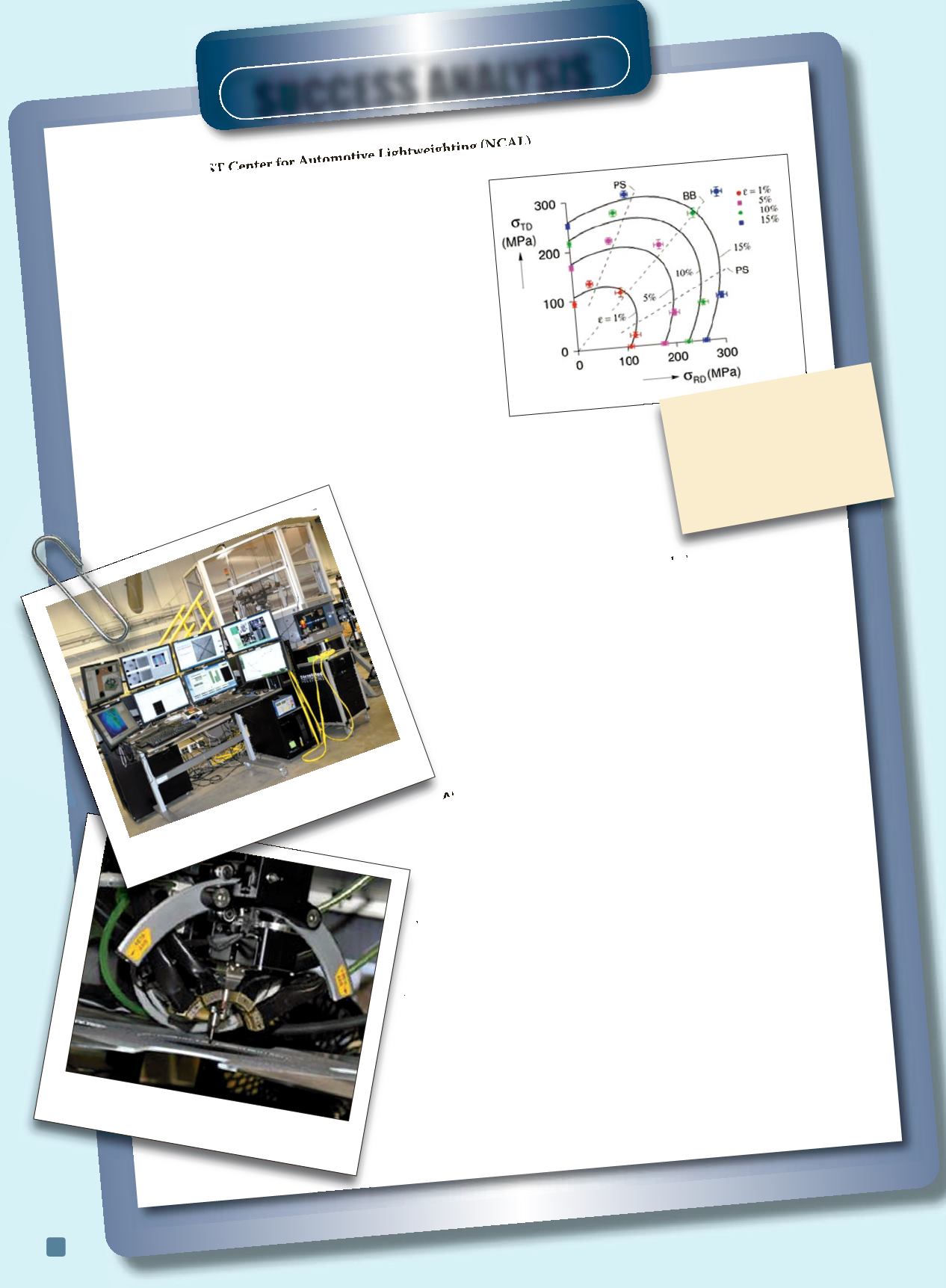
60
Specimen Name:
NIST Center for Automotive Lightweighting (NCAL)
Vital Statistics:
Today’s automakers lack the necessary tools to easily
incorporate lightweight materials (e.g., aluminum alloys, high-
strength steels, and polymer composites) due to inadequate data
and material models. As a result, the U.S. auto industry spends
hundreds of millions of dollars per year reworking metal forming
dies that do not make correct parts.
NCAL is developing the measurement methodology,
standards, and analysis techniques required by auto
manufacturers and base metal suppliers to transition to advanced
materials for auto body components.
The center developed a technique to measure the stress-strain
response of sheet metal along nonlinear multiaxial paths. The
team also measures the sheet’s evolving crystallographic texture
to develop a microstructural understanding of deformation response.
Success Factors:
By directly measuring the mechanical
response of sheet metal being deformed along a
complex path, NCAL is providing the data
needed to develop next-generation models that
will accelerate the use of advanced lightweight
materials in vehicles. This high strain rate data helps ensure safe
performance in collisions and reduces the need for costly physical crash
tests, according to researchers.
Equipment includes a high-rate servohydraulic mechanical testing
machine; next-generation cruciform metal formability system
designed to test sheet metal along any path in strain space relevant to
metal forming operations; a Marciniak testing system with two
punch sizes, x-ray diffraction, and digital image correlation;
SEM, TEM, EBSD, XRD, OIM, optical and neutron diffraction;
computational facilities; and a sample preparation area that
includes plasma cutting and welding.
About the Innovators:
NCAL is led by Tim Foecke and NIST researchers Mark
Iadicola, Thomas Gnaeupel-Herold, Adam Creuziger, Bill Luecke,
Dave Pitchure, and Mark Stoudt. Consortium partners include
Ford, General Motors, Chrysler, ThyssenKrupp, US Steel Corp.,
ALCOA, Carnegie Mellon University, and several others.
What’s Next:
Beyond model generation, there is ongoing work to measure the actual
stress-strain state within the neck of an ASTM E-8 tensile specimen to
determine mechanical properties beyond instability. This high strain data
helps forming simulations, as the constrained deformation during forming
often exceeds that reached by traditional tensile tests.
Contact Details:
Tim Foecke, NCAL Director
NIST Material Measurem
ent Laboratory10
0 Bureau Dr., Gaithersburg, MD 20899-8553
301/975-6592,
timothy.foecke@nist.gov, www.nist.gov/lightweighting
Close-up of x-ray stress measurement
mounted on the cruciform system,
positioned above a deforming sample.
SucceSS AnAlySiS
ADVANCED MATERIALS & PROCESSES •
MARCH 2014
For the first time, the
tensile multiaxial yield
surface of 5754 aluminum
alloy sheet was measured
from initial yield up to
failure. Graph shows the
flow stress of 5754 Al
as a function of strain.
Control center and overview of NCAL’s
metal formability system.